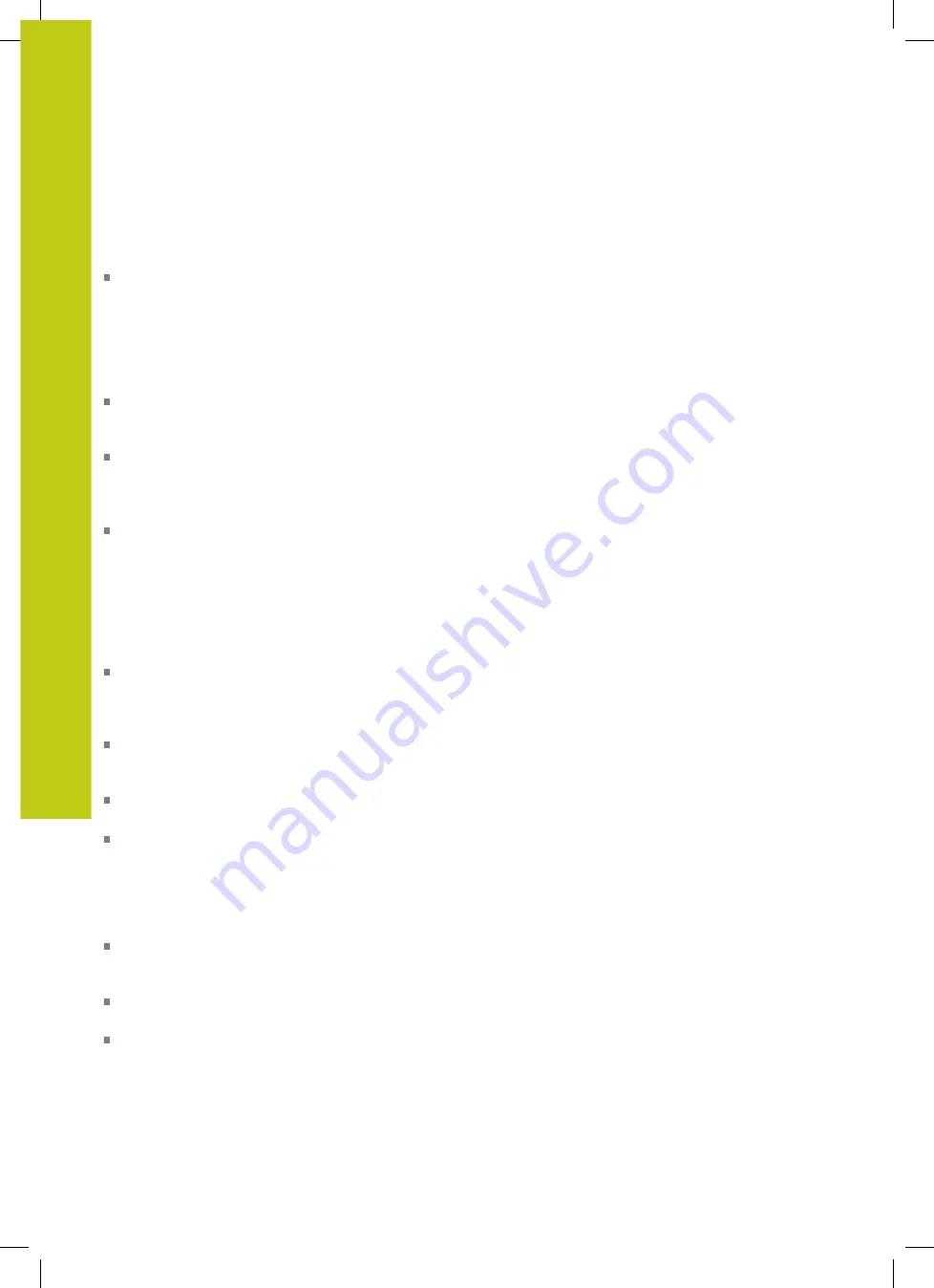
Multiple axismachining
12.6 Running CAM programs
12
470
HEIDENHAIN | TNC 620 | ISO Programming User's Manual | 9/2016
Consider with processor configuration
Take the following points into account with post processor
configuration:
Always set the data output for axis positions to at least four
decimal places. This way you improve the quality of the NC data
and avoid rounding errors, which can result in defects visible to
the naked eye on the workpiece surface. Output to five decimal
places (option 23) may achieve improved surface quality for optical
components and components with very large radii (i.e. small
curvatures), for example forms for the automotive industry.
Always set the data output for the machining of surface normal
vectors (LN blocks, only Klartext conversational programming) to
exactly seven decimal places
Set the tolerance in Cycle G32 so that in standard behavior it is at
least twice as large as the chord error defined in the CAM system
Also note the information in the functional description for Cycle
G32.
If the chord error selected in the CAM program is too large,
then, depending on the respective curvature of a contour, large
distances between NC blocks can result, each with large changes
of direction. During machining this leads to drops in the feed rate
at the block transitions. Recurring and equal accelerations (i.e.
force excitation), caused by feed-rate drops in the heterogeneous
NC program, can lead to undesirable excitation of vibrations in the
machine structure.
You can also use arc blocks instead of linear blocks to connect the
path points calculated by the CAM system. The TNC internally
calculates circles more exactly than can be defined via the input
format
Do not output any intermediate points on exactly straight lines.
Intermediate points that are not exactly on a straight line can
result in defects visible to the naked eye on the workpiece surface
There should be exactly one NC data point at curvature transitions
(corners)
Avoid sequences of many short block paths. Short paths between
blocks are generated in the CAM system when there are large
curvature transitions with very small chord errors in effect. Exactly
straight lines do not require such short block paths, which are
often forced by the continuous output of points from the CAM
system
Avoid a perfectly even distribution of points over surfaces with
a uniform curvature, since this could result in patterns on the
workpiece surface
For 5-axis simultaneous programs: avoid the duplicated output of
positions if they only differ in the tool’s angle of inclination
Avoid the output of the feed rate in every NC block. This would
negatively influence the TNC’s velocity profile
Содержание TNC 620 Programming Station
Страница 1: ...TNC 620 User s Manual ISO programming NC Software 817600 04 817601 04 817605 04 English en 9 2016 ...
Страница 4: ......
Страница 5: ...Fundamentals ...
Страница 28: ...Contents 28 HEIDENHAIN TNC 620 ISO Programming User s Manual 9 2016 ...
Страница 57: ...1 First Steps with the TNC 620 ...
Страница 77: ...2 Introduction ...
Страница 110: ......
Страница 111: ...3 Fundamentals file management ...
Страница 166: ......
Страница 167: ...4 Programming aids ...
Страница 194: ......
Страница 195: ...5 Tools ...
Страница 234: ......
Страница 235: ...6 Programming contours ...
Страница 284: ......
Страница 285: ...7 Data transfer from CAD files ...
Страница 304: ......
Страница 305: ...8 Subprograms and program section repeats ...
Страница 323: ...9 Programming Q parameters ...
Страница 384: ......
Страница 385: ...10 Miscellaneous functions ...
Страница 407: ...11 Special functions ...
Страница 433: ...12 Multiple axis machining ...
Страница 475: ...13 Pallet management ...
Страница 480: ......
Страница 481: ...14 Manual Operation and Setup ...
Страница 549: ...15 Positioning with Manual Data Input ...
Страница 554: ......
Страница 555: ...16 Test Run and Program Run ...
Страница 590: ......
Страница 591: ...17 MOD Functions ...
Страница 622: ......
Страница 623: ...18 Tables and Overviews ...