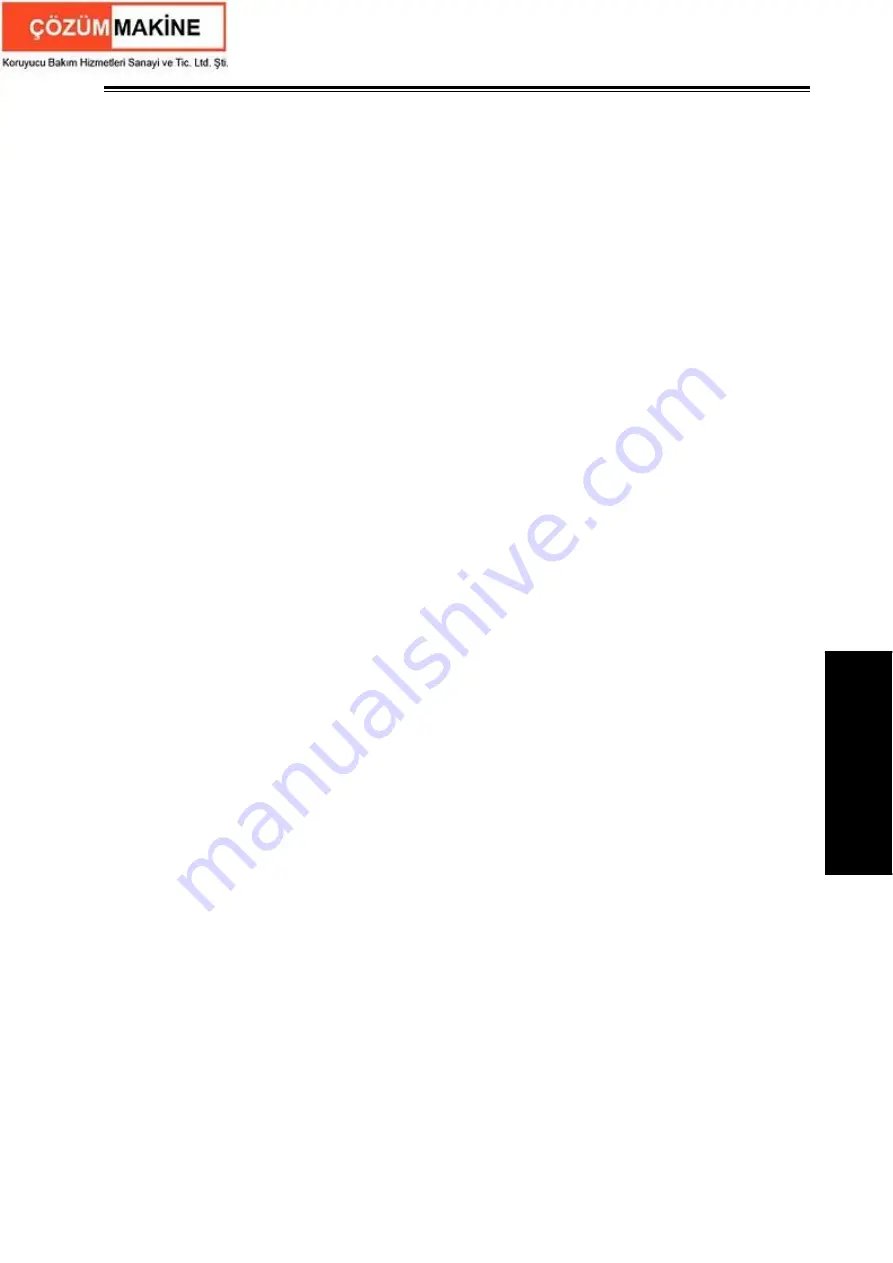
Chapter 4 Machine Debugging methods and Modes
417
Ⅲ
Connection
Data parameter No.089: spindle braking time
4.6.3 Switch volume control of spindle speed
When the machine is controlled by a multi-speed motor, the motor speed codes are S01
~
S04.
The relevant parameters are as follows:
State parameter No.001 Bit4=0: select spindle speed switch control;
4.6.4 Analog voltage control of spindle speed
This function can be obtained by the parameter setting of CNC. By interface outputting 0V
~
10V
analog voltage to control frequency inverter, the stepless shift can be obtained. And the related
parameters needed to be adjusted are:
Bit parameter No.001 Bit4=1: for spindle speed analog voltage control;
Data parameter No.021: offset value as spindle speed code voltage is 10V;
Data parameter No.036: offset value as spindle speed code voltage is 0V;
Data parameter No.037
~
No.040: for max. speed clamping of spindle gear 1
~
4; it defaults the
spindle gear 1 when CNC power on.
Basic parameters are needed to adjust the inverter:
CW or CCW code mode selection: it is determined by terminal VF;
Frequency setting mode selection: it is determined by terminal FR;
If the speed by programming is not consistent with that detected by the encoder, it can be
adjusted to be consistent with the actual one by adjusting the data parameter No.037
~
No.040.
Speed adjustment method: select the corresponding spindle gear, determine the data parameter
is 9999 as for this system gear, set the spindle override for 100%. Input spindle run command in MDI
mode to run the spindle: M03/M04 S9999, view the spindle speed shown on the right bottom of the
screen, then input the speed value displayed into the corresponding system parameter.
When entering S9999 code, the voltage should be 10V, S0 for 0V. If there is a voltage error,
adjust bit parameter No.021 and No.036 to correct the voltage offset value (corrected by
manufacturer, usually not needed).
For the current max. speed gear, if the analog voltage output by CNC is not 10V, set it for 10V by
adjusting the data parameter No.021; when the input speed is 0, if the spindle still slowly rotates, it
means the analog voltage output by CNC is higher than 0V, so set a smaller value for data parameter
No.036.
If the machine is not fixed with an encoder, the spindle speed can be detected by a speed
sensing instrument, input S9999 in MDI mode to set the speed value displayed by the instrument into
the data parameter No.037
~
No.040.
4.7 Backlash Offset
The X axis backlash offset value is input by diameter, Z axis backlash offset value is input by the
actual backlash which can be measured by a dial-indicator, a micrometer or a laser detector. Because
the backlash offset can improve the machining precision only by accurate compensation, it is not
recommended to measure it in MPG or Step mode, but the following method is suggested:
z
Program editing (taking example of Z):
O0001
;
N10 G01 W10 F800
;
N20 W15
;
Содержание GSK980TDc
Страница 17: ...I Programming ...
Страница 18: ...GSK980TDc Turning CNC System User Manual ...
Страница 190: ...GSK980TDc Turning CNC System User Manual 172 Ⅰ Programming ...
Страница 191: ...Ⅱ Operation Ⅱ Operation ...
Страница 192: ...GSK980TDc Turning CNC System User Manua Ⅱ Operation ...
Страница 217: ...Chapter 1 Operation Mode and Display Interface 197 Ⅱ Operation 2 Data parameter page 3 Common used parameter page ...
Страница 326: ...GSK980TDc Turning CNC System User Manual 306 Ⅱ Operation ...
Страница 327: ...Ⅲ Connection Ⅲ Connection ...
Страница 328: ...GSK980TDc Turning CNC System User Manual Ⅲ Connection ...
Страница 470: ...GSK980TDc Turning CNC System User Manual 448 Ⅲ Connection ...