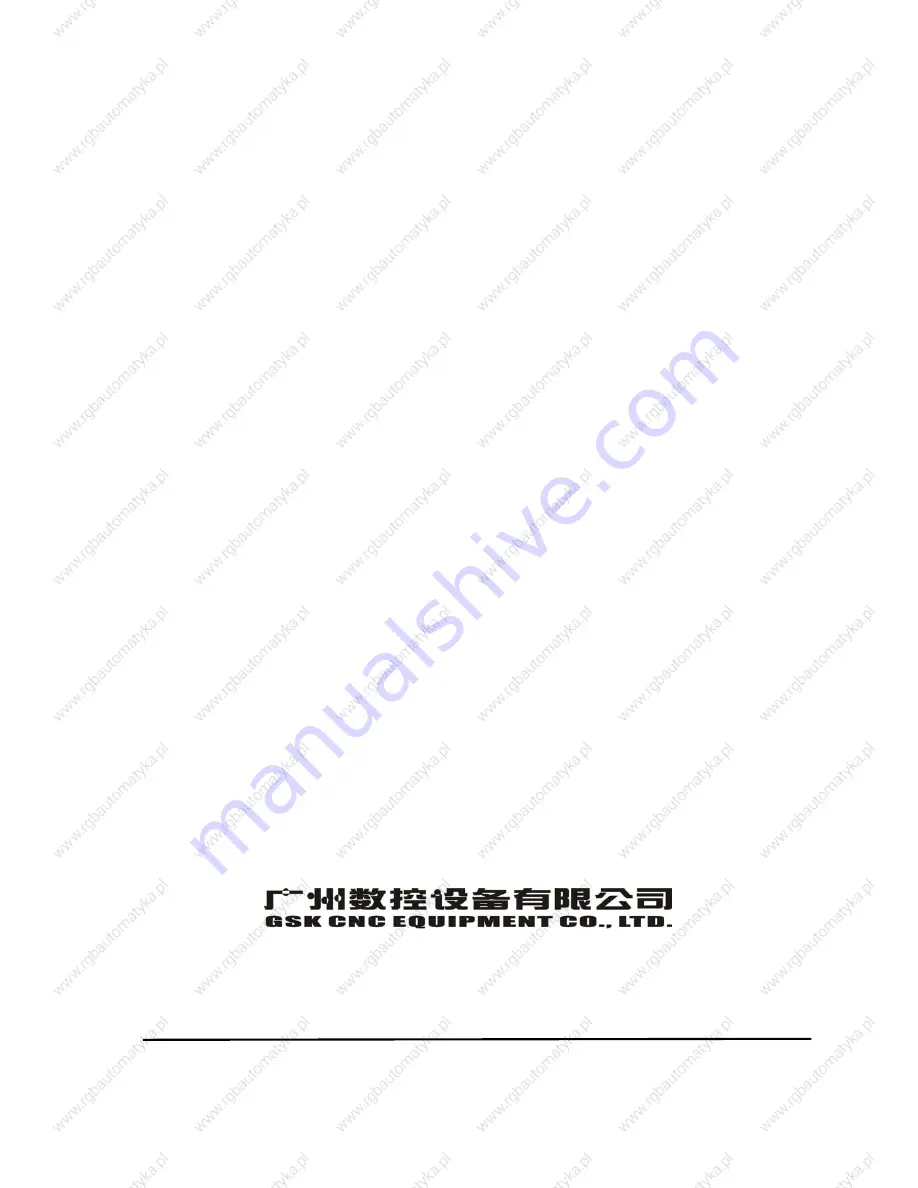
Add: No.52, 1
st
. Street, Luochong North Road, Luochongwei, Guangzhou, 510165, China
Website: http://www.gsk.com.cn E-mail: [email protected]
Tel: 86-20-81796410/81797922 Fax: 86-20-81993683
All specifications and designs are subject to change without notice July 2007/Edition 2
Aug. 2007/Printing 2
Содержание 218M
Страница 3: ...GSK 218M CNC System Connection and PLC Manual...
Страница 15: ...GSK218M CNC System Connection and PLC Manual 12 Volume one Programming...
Страница 70: ...GSK218M CNC System Connection and PLC Manual 67 Volume Two Function...
Страница 140: ...GSK218M CNC System Connection and PLC Manual 137 Volume Three Operation...
Страница 160: ...GSK218M CNC System Connection and PLC Manual 157 Volume Four Connection...
Страница 163: ...GSK218M CNC System Connection and PLC Manual 160 2 Side view 3 Overlook Without PC2 power supply...