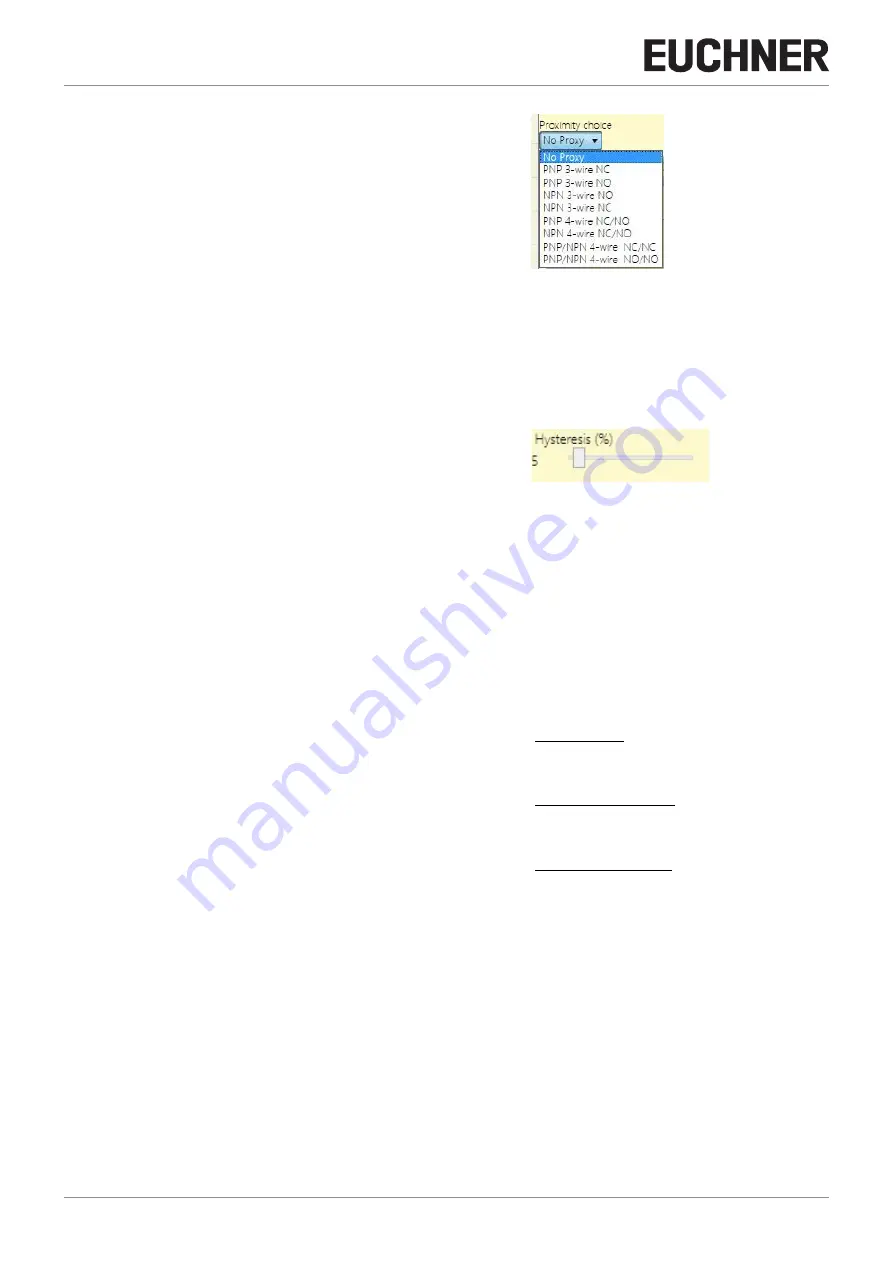
Operating Instructions
Modular Safety Control System MSC
122
(Translation of the original operating instructions) 2121331-04-04/19
Proximity choice: Selecting the proximity switch enables you to select
between PNP, NPN, NO contact, NC contact, 3-wire or 4-wire.
To ensure Performance Level = Pl e, PNP NO must be used (see “Prox-
imity switch input on speed monitoring modules SPM” on page 29).
Encoder Resolution: Entry for the number of pulses/revolution (for a
rotary sensor) or μm/pulse (for a linear sensor) in relation to the 1st
measuring device.
Verification: In this field you can enter the number of pulses/revolution
(for a rotary sensor) or µm/pulse (for a linear sensor) in relation to
the 2nd measuring device.
Figure 131: Proximity choice
Gear Ratio: This parameter is active if there are two sensors on the selected axis. This parameter enables you to enter the
gear ratio between the two sensors. If the two sensors are on the same moving object, the ratio is 1, otherwise the figure
for the ratio must be entered. Example: There is an encoder and a proximity switch and the latter is on the moving object
that (due to a gear ratio) moves at twice the speed of the encoder. For this reason, this value must be set to 2.
Hysteresis (%): Corresponds to the hysteresis (in percent) below
which a speed change is filtered out. Here a value other than 1 is to
be entered to prevent continuous switching of the input.
Figure 132: Hysteresis
High Speed: Enter the maximum value for the speed window in this field. Above this limit the WINDOW output on the function
block is "0" (FALSE). If the speed measured is below the value, but still above the "Low Speed" limit, the WINDOW output
on the function block is "1" (TRUE).
Low Speed: Enter the minimum value for the speed window in this field. Below this limit the WINDOW output on the function
block is "0" (FALSE). If the speed measured is above the value, but still below the "High speed" limit, the WINDOW output
on the function block is "1" (TRUE).
Frequency: Indicates the maximum frequency values calculated fM and fm (reduced by the hysteresis entered).
Ì
If the value indicated is GREEN, the calculated frequency is in the correct range.
Ì
If the value indicated is RED, the parameters given in the following formulas must be changed.
1. Rotary axis, rotary sensor. The calculated frequency is:
f Hz
[ ]
=
rpm rev /min
[
]
60
*
Resolution pulses/rev
[
]
2. Linear axis, rotary sensor. The calculated frequency is:
f Hz
[ ]
=
speed m/min
[
]
*
1000
60
*
pitch mm/rev
[
]
*
Resolution pulses/rev
[
]
3. Linear axis, linear sensor. The calculated frequency is:
f Hz
[ ]
=
speed mm/s
[
]
*
1000
Resolution µm/pulse
[
]
4. Hysteresis. Only to be changed if: fM = green; fm = red
KEY:
f = Frequency
rpm = Rotary speed
Resolution = Measurement
speed = Linear speed
pitch = Pitch
Содержание MSC
Страница 1: ...EN Operating Instructions Installation and use Modular Safety Control System MSC ...
Страница 171: ......
Страница 173: ......