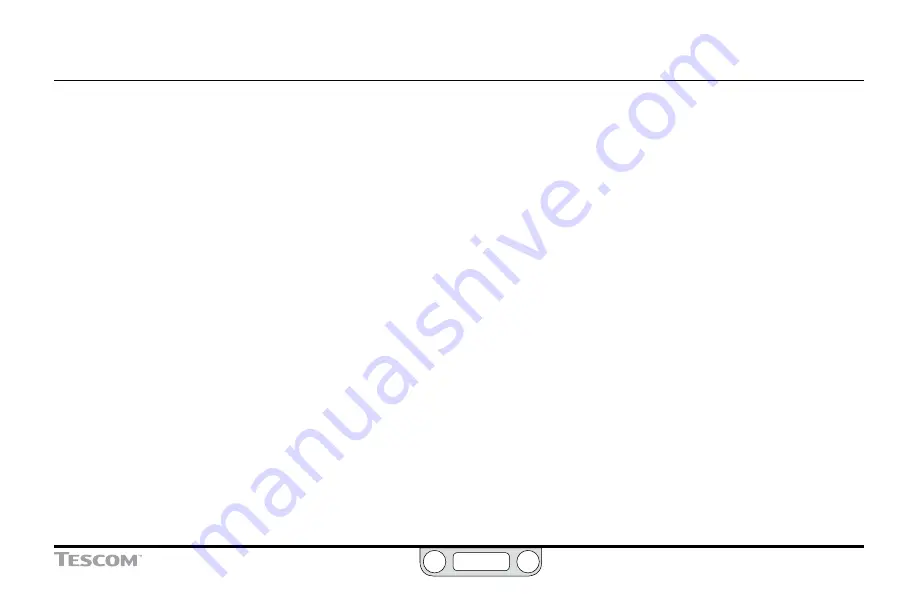
ER5000
—
49
Glossary of Terms
Regulator
Mechanical valve that dynamically controls the pressure of liquid
or gas in a process line by opening or closing in response to
activation of an internal control element. Works to ensure that
the supplied pressure matches the demand of the system.
Ringing
Oscillation around a
Setpoint
, due to a
Proportional
or
Integral
setting that is too high or a
Derivative
setting that is too low.
Proper
Tuning
generally aims to minimize ringing.
Rise Time
Time required for feedback to reach a new
Setpoint
or a certain
percentage of that setpoint, following a
Step Change
. TESCOM™
uses the ISA standard, which specifies rise time as the time it takes
to travel from 10% to 90% of the new setpoint. Proper
Tuning
aims
to minimize rise time without inducing
Overshoot
or
Ringing
.
Segment
One command line within a
Profile
.
Setpoint
The value that a
PID Controller
works to maintain within the system
it controls. The setpoint may remain at one level or change over
time, depending on the requirements of the system. A well tuned
controller will maintain a
Stable State
at setpoint and implement
setpoint changes quickly and accurately. The ER5000 requires a
setpoint signal in order to function. This signal can come from an
external source such as a
PC
or
PLC
or from a
Profile
.
Settling Time
Time required for a system to reach a stable state once it has
reached a new setpoint. Proper
Tuning
generally aims to minimize
Settling Time.
Solenoid Valve
An electromechanical valve controlled by electrical current
through a coil. The ER5000 valves are
Pulse Width Modulation
(PWM)
driven mechanical valves that open and close in
direct proportion to the output signal from the controller’s
microprocessor. Positive output activates the inlet valve,
increasing pressure and negative output activates the exhaust
valve, decreasing pressure.
Содержание Tescom ER5000 Series
Страница 2: ...2 Safety Installation Operations Precautions ...
Страница 9: ...9 Table of Contents ...
Страница 14: ...14 Features and Specifications ...
Страница 25: ...25 What s New ...
Страница 29: ...29 How It Works ...
Страница 44: ...44 Glossary of Terms ...
Страница 57: ...57 Getting Started ...
Страница 76: ...76 Installation Variations ...
Страница 111: ...111 The ERTune Program ...
Страница 116: ...116 The ERTune Program Basic Features ...
Страница 187: ...187 The ERTune Program Power User ...
Страница 196: ...196 ER5000 Software Development Support ...
Страница 202: ...202 Troubleshooting ...
Страница 221: ...221 Internal Variables ...
Страница 236: ...236 Certifications and Warranty ...
Страница 241: ...241 Appendix A Setting up the ERTune Program on Windows 8 PCs ...