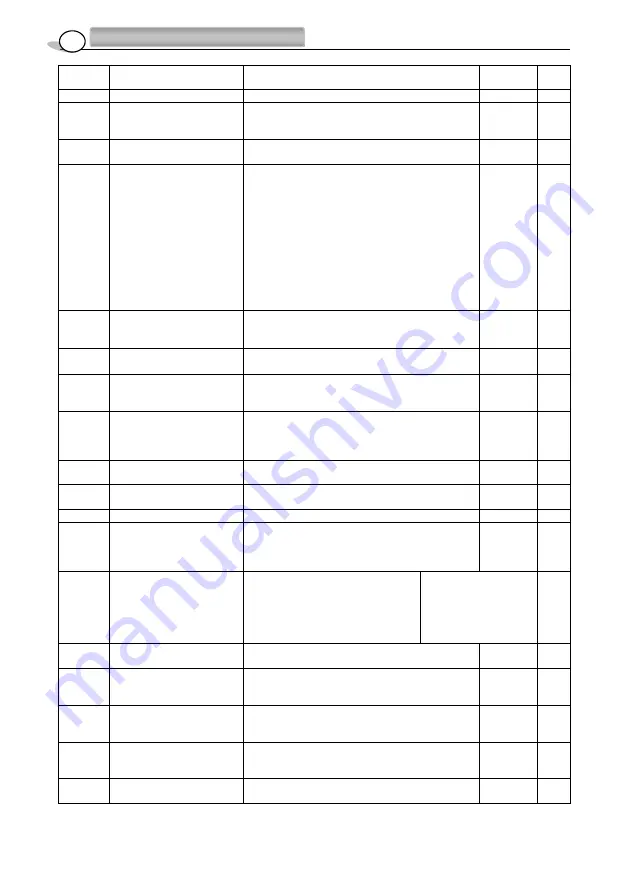
Chapter 5 Function parameter
22
P3-09
VF Slip compensation
gain
0.0%
~
200.0%
0.0%
〇
P3-10 VF Overexcitation gain
0
~
200
64
〇
P3-11
VF Oscillation
suppression gain
0
~
100
Model
depende
nt
〇
P3-12
Oscillation suppression
mode selection
0~4
3
●
P3-13
Voltage source for
V/F separation
0: Digital setting(d3-12)
1: AI1
2: AI2
3: AI3
4: Pulse setting(HDI)
5: Multi-function
6: Simple PLC
7: PID
8: Communication setting
Note:100.0% corresponds to the rated
motor voltage
0
〇
P3-14
Voltage digital
setting for V/F
separation
0 V ~ rated motor voltage
0V
〇
P3-15
Voltage rise time
of V/F separation
0.0s~1000.0s
0.0s
〇
P3-16
VF Separate voltage
deceleration time
0.0s
~
1000.0s
note
:
Indicates the time from 0V changes
to the rated voltage of the motor
0.0s
〇
P3-17 VF Separate shutdown
mode selection
0: frequency / voltage is independently
reduced to 0
1: After the voltage is reduced to 0, the
frequency is reduced again.
0
〇
P3-18
Overcurrent stall
operating current
50~200%
150%
●
P3-19
Over-current
suppression
0 Invalid
、
1 Valid
1
●
P3-20
Over current stall gain
0~100
20
〇
P3-21
Double speed overrun
speed action current
compensation
coefficient
50~200%
50%
●
P3-22
Overvoltage stall
operating voltage
200.0V~2000.0V
Model dependent
220V
:
380V
380V
:
760V
480V
:
850V
690V
:
1250V
1140V
:
1900V
●
P3-23
Overvoltage stall
enable
0 Invalid
、
1 Valid
1
●
P3-24
Overvoltage stall
suppression frequency
gain
0~100
30
〇
P3-25
Overvoltage stall
suppression voltage
gain
0~100
30
〇
P3-26
Overvoltage stall
maximum rising
frequency limit
0~50Hz
5Hz
●
P3-27 Slip compensation time
constant
0.1~10.0s
0.5
〇