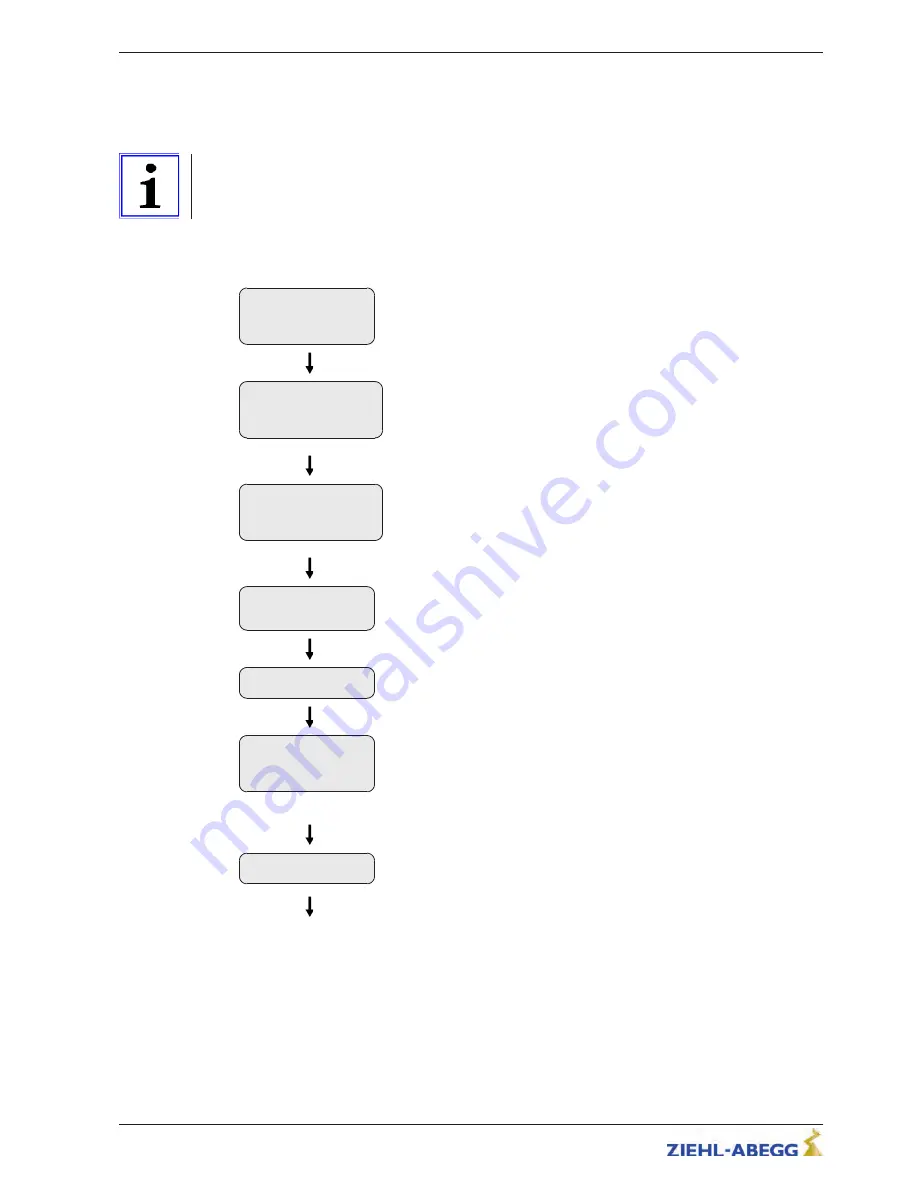
15.2.2
Load-free alignment EnDat-Encoder
When aligning the EnDat encoder, the frequency inverter supplies the motor with direct current. During
this, the rotor jumps to the middle of the nearest poles. In this rotor position, the offset value is stored
in the encoder, which sets the encoder to the
“
0
“
position.
Information
The calibration should always be done twice. Any inaccuracy in the 1st calibration is detected by the
2nd calibration and can be corrected.
Carrying out the load-free alignment with EnDat-encoder
MMC Recorder
->Encoder adjust.
Safety gear
HW-Ident.
Select menu
Encoder adjustment
Encoder-adjust.
|
-
"
ENC_OFF 0.00
DEG
|
-
"
0.00
Encoder Offset
Select parameter
"ENC_OFF"
Enter "ENC_OFF=0"
Encoder-adjust.
|
-
"
ENC_ADJ Off
|
-
"
On
Encoder adjustment
Select parameter
"ENC_ADJ"
Switch on encoder adjustment with "ENC_ADJ=ON"
CHECK or
START adjustment?
[Esc][x][CHK][START]
Start Encoder-adjustment with
[START]
Press inspection!
[Esc]
Keep the inspection run push-button pressed.
Wait.Check encoder
function.
+514 +512 INC/P
The motor is powered in phase U and the rotor to zero of the next pole.
Encoder check, check the motor data for plausibility.
- Display of impulses counted between the poles (e.g. 514)
- Display of number of expected (calculated) impulses / pole pair (e.g. 512)
Wait
+12.9A -6.5A -6.47A
Rotor is held in zero point of the next pole
- Display of motor current of phases U V W
Original operating instructions
ZETADYN 3C
Special functions
R-TBA08_03-GB 1619
Part.-No. 00163322-GB
159/204