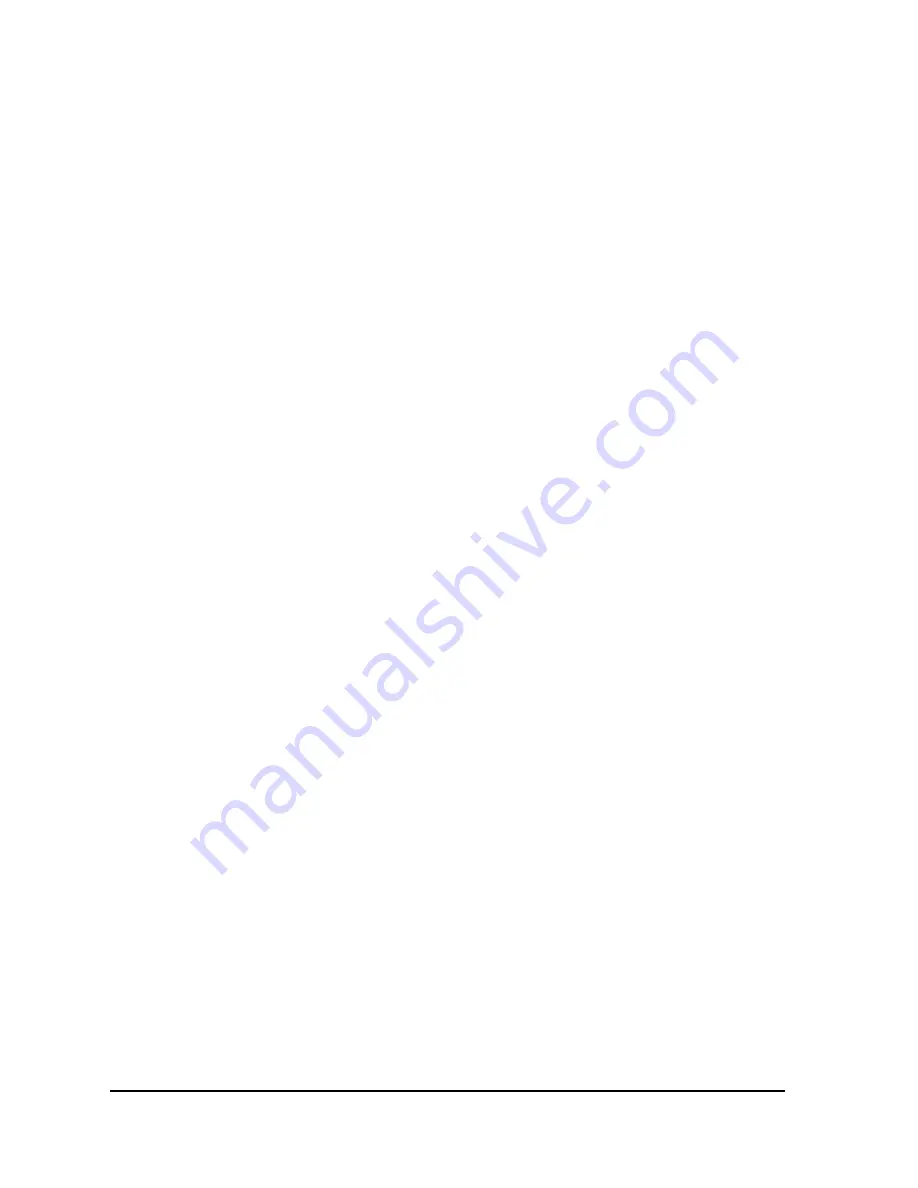
YL9110 Quaternary Pump
precision reduced ; so it is desired to check it periodically. Main cause of mobile phase filter blocking is
growth of bacteria, and two causes to block inlet filter is growth of bacteria and use of solvent containing
impurity. In order to prevent growth of bacteria, use at least 10-20% organic solvent or solvent containing
growth depressing component. If pure water or soluble solution without interfering material is used, many
bacteria will grow in mobile phase filter though it is replaced with fresh solution everyday. Therefore, use
solvent of HPLC grade filtered well at all times for mobile phase. Blocking of in-line filter is caused by
accumulation of small particles generated due to wear of high pressure seal by using of impure solvent
and long use of instrument. In case mobile phase filter and in-line filter are contaminated, condition of filter
may be improved by washing it by ultrasonic cleaner with 10% nitric acid solution for 30 minutes. If it is not
improved by ultrasonic wave cleaning, replace it with new filter.
Change and cleaning of mobile phase filter
1) Separate mobile phase filter from tubing. As the surface of teflon tubing of mobile phase filter of
insertion type is slippery, separate it with tubing held avoiding slippage using #1000 sand paper.
2) In case of performing ultrasonic wave cleaning, wash head part by ultrasonic cleaner with 10%
nitric acid solution for 30 minutes, wash it again by ultrasonic cleaner with pure water for about 10
minutes, then dry it. In order to replace filter with new one, prepare new mobile phase filter of
same size.
3) If washing has been completed, assemble filter to be replaced newly again. Hold teflon tubing
using sand paper and insert mobile phase filter of insertion type with center adjusted into middle
hole.
Changing and cleaning of in-line filter
1) Separate connected tubing from in-line filter assembly using spanner.
2) Separate head part of in-line filter assembly from body using spanner.
3) In case of performing ultrasonic wave cleaning, perform ultrasonic wave cleaning to
head part for 30 minutes with 10% nitric acid solution, perform ultrasonic wave cleaning for 10
minutes with pure water, and then dry it. In order to replace filter with new one, separate filter
located at back side of head part.
4) In case of replacing it with new filter, replace it with new in-line filter located at the location where
it was separated ; and in case ultrasonic wave cleaning has been completed, re-assemble head
part of dried assembly.
5) Using spanner, tighten head part sufficiently so that there may be no leakage of liquid even at
6000 psi.
28
Summary of Contents for YL9100 HPLC
Page 1: ......
Page 2: ...YL9100 HPLC SYSTEM YL9101 VACUUM DEGASSER USER MANUAL...
Page 9: ...YL9100 HPLC SYSTEM YL9110 QUATERNARY SOLVENT DELIVERY PUMP USER MANUAL...
Page 44: ...YL9100 HPLC SYSTEM YL9111 BINARY PUMP USER MANUAL...
Page 79: ...YL9100 HPLC SYSTEM YL9112 ISOCRATIC PUMP USER MANUAL...
Page 114: ...YL9100 HPLC System YL9120 UV Vis Detector USER MANUAL...
Page 136: ...YL9100 HPLC SYSTEM YL9130 COLUMN COMPARTMENT USER MANUAL...
Page 150: ...YL9100 HPLC SYSTEM YL9160 PDA Detector USER MANUAL...
Page 169: ...YL9100 HPLC System YL9170 RI Detector USER MANUAL...
Page 188: ......