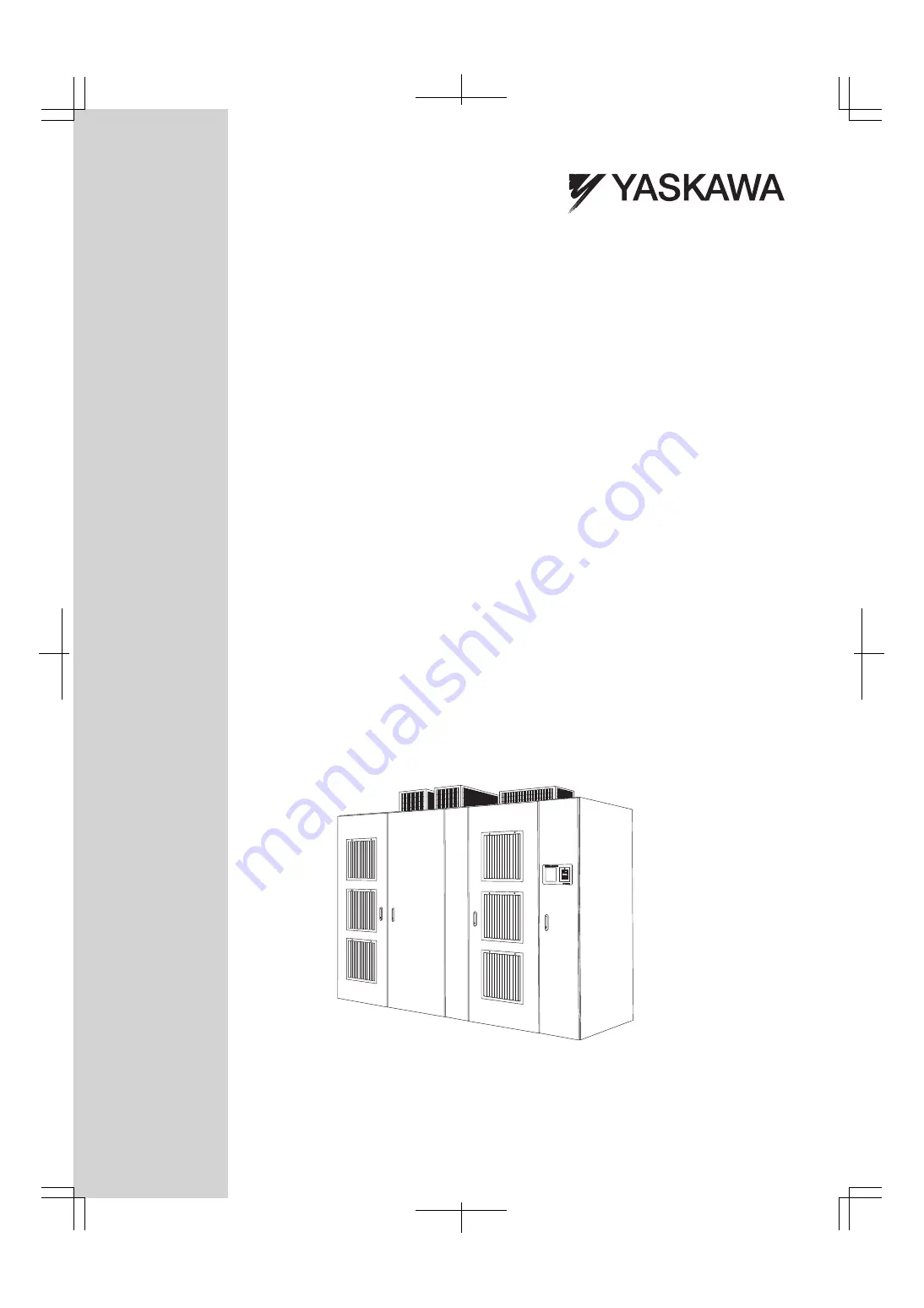
FSDrive-MV1000
Parameter Guide
MANUAL NO. TOEP C710687 03B
To properly use the product, read this manual thoroughly and retain
for easy reference, inspection, and maintenance. Ensure the end user
receives this manual.
2.4 kV Class, 3 kV Class, 4.16 kV Class, 6 kV Class, 11 kV Class
Super Energy-Saving Medium-Voltage AC Drive