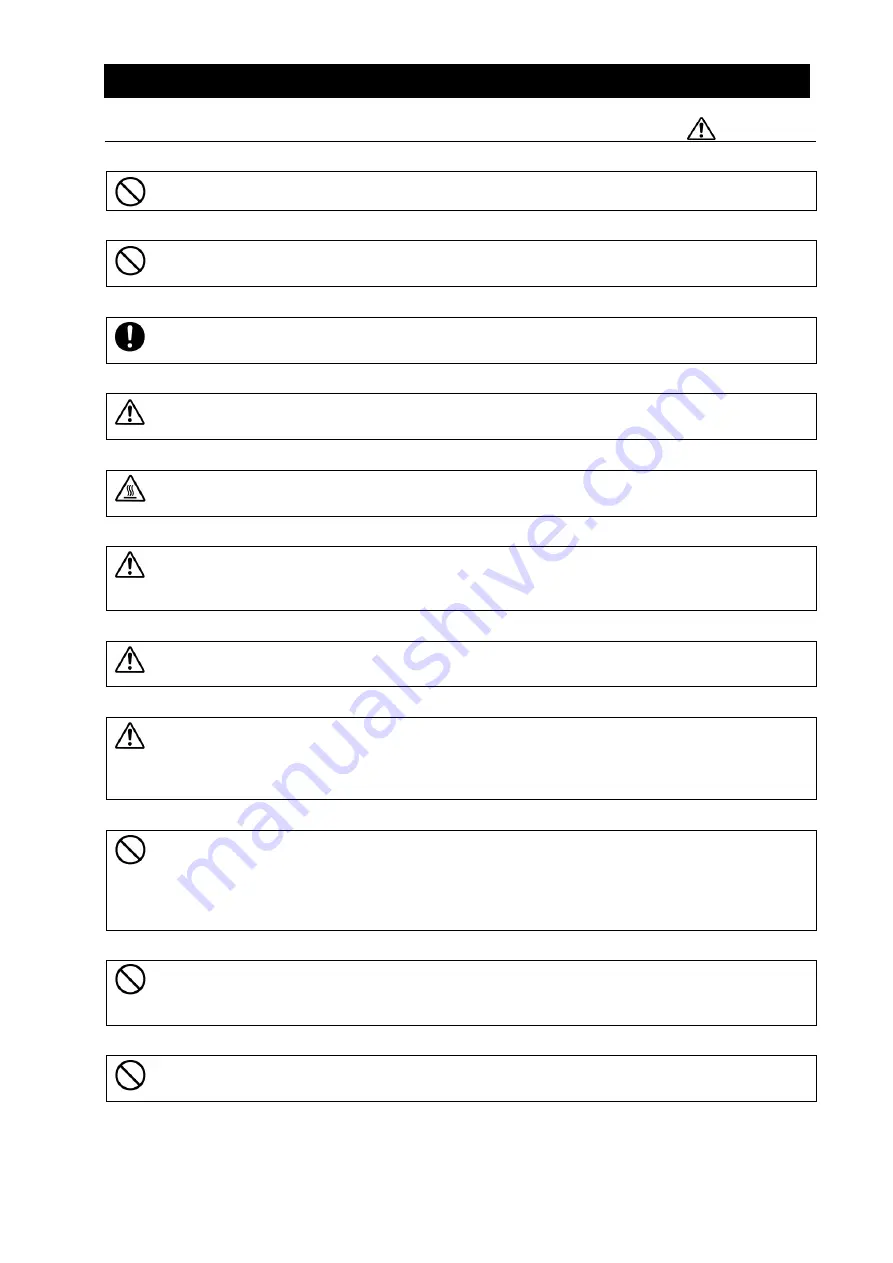
86
5. Handling Precautions
Caution
Do not step on this unit
Do not step on this unit. It will cause injury if this unit fall down or break.
Do not place or drop anything on the unit
Do not place or drop anything on the unit. Since the unit contains precision components, it
may malfunction due to vibration, impact, etc.
During a thunder storm
During a thunderstorm, turn off
the power key immediately, then turn off the circuit breaker
and the main power. If this procedure is not followed, fire or electrical shock may be caused.
Countermeasure for stop operation during night or long-term stop
Turn off the power of earth leakage breaker and disconnect the power cord from the power
source before stopping the operation of equipment overnight or for a long time.
Do not touch the hot section
The temperature on the cover and top board on the chamber are very hot during operation or
just after operation is completed. Do not touch these sections to avoid a burn injury.
When opening the cover…
Make sure that the pressure gauge reading has decreased to 0(zero) MPa before opening
the cover. Open the cover slow carefully. The high-temperature and pressure vapor blows out
if the cover is opened during high pressure.
When opening/closing the door…
Do not put your hands or face into the traveling range (space) of door when it is opened or
closed. The door may contact, which may cause an injury.
When draining water…
The water in the chamber is very hot just after operation is completed. Be careful not to get a
burn injury. Drain the water after the water is sufficiently cooled down.
Do not drain water during operation. The hot water blows out if the drain valve is opened
while the pressure is increasing.
Do not damage the packing on the cover or flange on the chamber
Damage or dirt on these areas may cause the vapor leakage, which may be the cause of
burn injury. Keep these sections always clean. Do not damage them with the rack when
taking out and putting in the sterile samples. The packing degrades wit time. It must be
replaced if vapor leak occurs frequently. In this case consult with the selling office where you
purchased or our sales office.
Replace the packing early
The packing is a consumable. If it shows the sign of damage or hardening, replace it early.
Please consult with the selling office where you purchased or our sales office for the
replacement of packing.
Do not perform procedures other than described in this document
Do not perform procedures other than described in this document. Otherwise an unexpected
accident may occur.