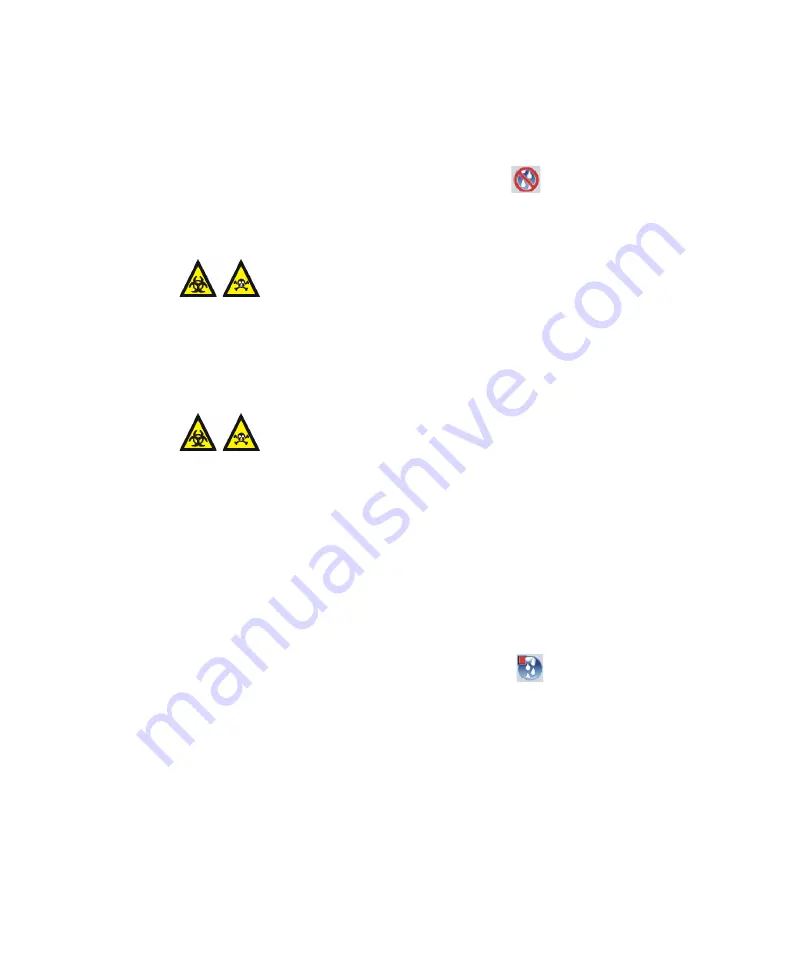
4-16
Maintenance Procedures
Required materials
Chemical-resistant, powder-free gloves
To empty the nitrogen exhaust trap bottle
1. In the Instrument Console, click Stop Flow
to stop the LC flow.
2. Pull the source enclosure release (located at the bottom, right-hand side)
outwards, and swing open the enclosure.
3. Unscrew and remove the nitrogen exhaust trap bottle from the cap and
associated fittings.
4. Dispose of the waste liquid in accordance with local environmental
regulations.
5. Fit and tighten the nitrogen exhaust trap bottle to the cap.
6. Secure the nitrogen exhaust trap bottle in the upright position.
7. Close the source enclosure.
Tip:
An automatic leak test will now be performed.
8. In the Instrument Console, click Start Flow
to start the LC flow.
Warning:
The waste liquid in the nitrogen exhaust trap
bottle comprises ACQUITY UPLC solvents and analytes.
Always wear chemical-resistant, powder-free gloves while
handling the nitrogen exhaust trap bottle.
Warning:
The waste liquid can be contaminated with
biohazardous and/or toxic materials. Dispose of it according
to local environmental regulations.
Summary of Contents for Xevo TQ MS
Page 10: ...x...
Page 42: ...2 10 Preparing the Mass Spectrometer for Operation...
Page 129: ...Replacing the air filter 4 81...
Page 130: ...4 82 Maintenance Procedures...
Page 146: ...B 4 Materials of Construction and Compliant Solvents...
Page 178: ...D 4 Plumbing the IntelliStart Fluidics system...