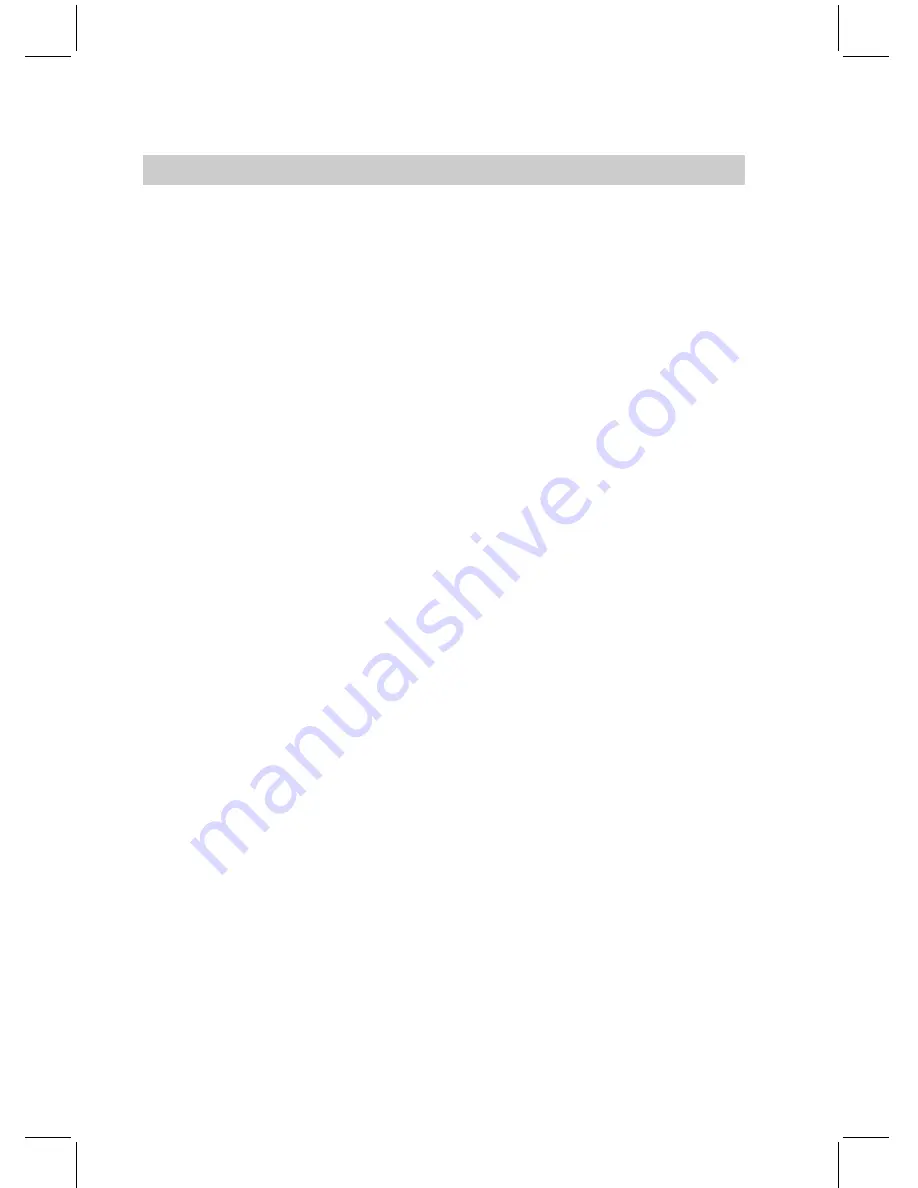
Note
Only use anti-corrosion agents that
have been approved for heat pumps
with DHW heating via single-walled
heat exchangers (DHW cylinders).
1.
Drain the heating water side of the
boiler system and reduce the pres-
sure until the pressure gauge indi-
cates "0".
2.
If the inlet pressure of the dia-
phragm expansion vessel is lower
than the static system pressure,
top up with sufficient nitrogen to
raise the inlet pressure higher than
the static system pressure.
Example:
Static head
(distance between the
heat source and the
highest heating surface)
10 m
= static pressure
1 bar
3.
Top up with water, until the filling
pressure exceeds the inlet pres-
sure of the diaphragm expansion
vessel.
On a cold system, the filling pres-
sure must be approx. 0.2 bar higher
than the static pressure.
Max. operating pressure: 4 bar.
4.
During commissioning, mark this
value on the pressure gauge as
minimum filling pressure.
Only for type BWC: Filling the primary circuit and checking
the pressure
1. Only for commissioning:
Flush the primary circuit.
2. Only for commissioning:
Fill the primary circuit with heat
transfer medium "Tyfocor -15 ° C"
and vent the circuit.
3.
Check the primary circuit pressure.
The pressure should be approx.
2 bar.
4.
Check the inlet pressure of the dia-
phragm expansion vessel and
adjust, if required (see page 43).
Further details regarding the individual steps
(cont.)
44
Commissioning, inspection, maintenance
55
92
901
GB
Summary of Contents for VITOCAL 300
Page 19: ...Connection diagram Open CLOSE System version 1 cont 19 Preparing for installation 5592 901 GB...
Page 22: ...Connection diagram Open CLOSE System version 2 cont 22 Preparing for installation 5592 901 GB...
Page 137: ...Control PCB 137 Connection and wiring diagrams 5592 901 GB Service...
Page 140: ...Parts lists cont 140 Parts lists 5592 901 GB...
Page 141: ...Parts lists cont 141 Parts lists 5592 901 GB Service...
Page 159: ...159 5592 901 GB...