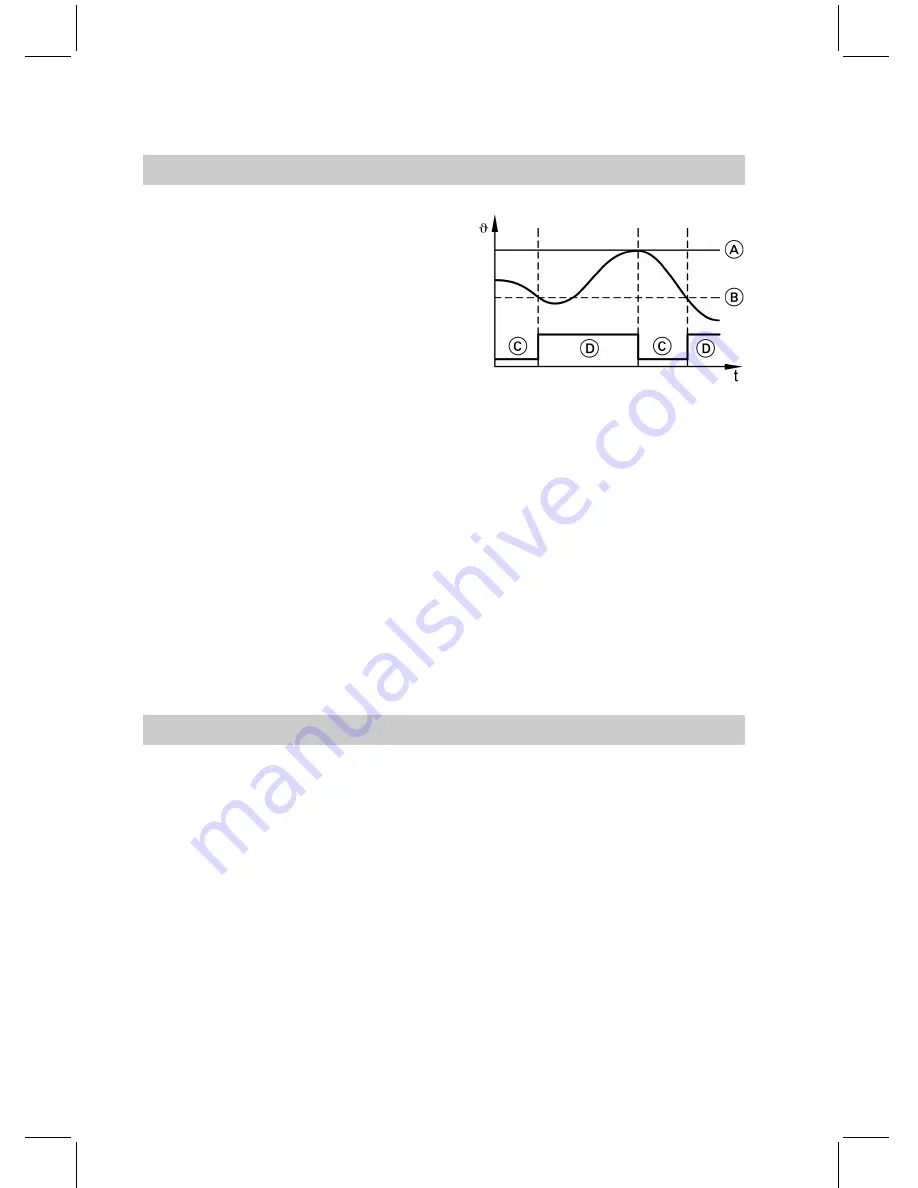
This setting determines, at what
deviation from the selected set tem-
perature the cylinder heating starts or
stops.
Note
If a low loss header is being used,
enter a higher setting
here
than the
one in "Flow hysteresis" (see
page 94).
A
Set temperature
B
Start hysteresis
C
Cylinder heating OFF
D
Cylinder heating ON
Access
&
"
System settings
"
&
"
Program
"
&
"
Buffer storage
"
&
"Hysteresis T top "
(
1
/
!
)
Standard setting
5 K
Setting range
2 to 20 K
Maximum temperature
Setting of the maximum temperature
in the heating water buffer cylinder.
Access
&
"
System settings
"
&
"
Program
"
&
"
Buffer storage
"
&
"max. temperature"
(
1
/
!
)
Standard setting
60 °C
Setting range
1 to 70 °C
Hysteresis temperature
116
Buffer cylinder control settings
55
92
901
GB
Summary of Contents for VITOCAL 300
Page 19: ...Connection diagram Open CLOSE System version 1 cont 19 Preparing for installation 5592 901 GB...
Page 22: ...Connection diagram Open CLOSE System version 2 cont 22 Preparing for installation 5592 901 GB...
Page 137: ...Control PCB 137 Connection and wiring diagrams 5592 901 GB Service...
Page 140: ...Parts lists cont 140 Parts lists 5592 901 GB...
Page 141: ...Parts lists cont 141 Parts lists 5592 901 GB Service...
Page 159: ...159 5592 901 GB...