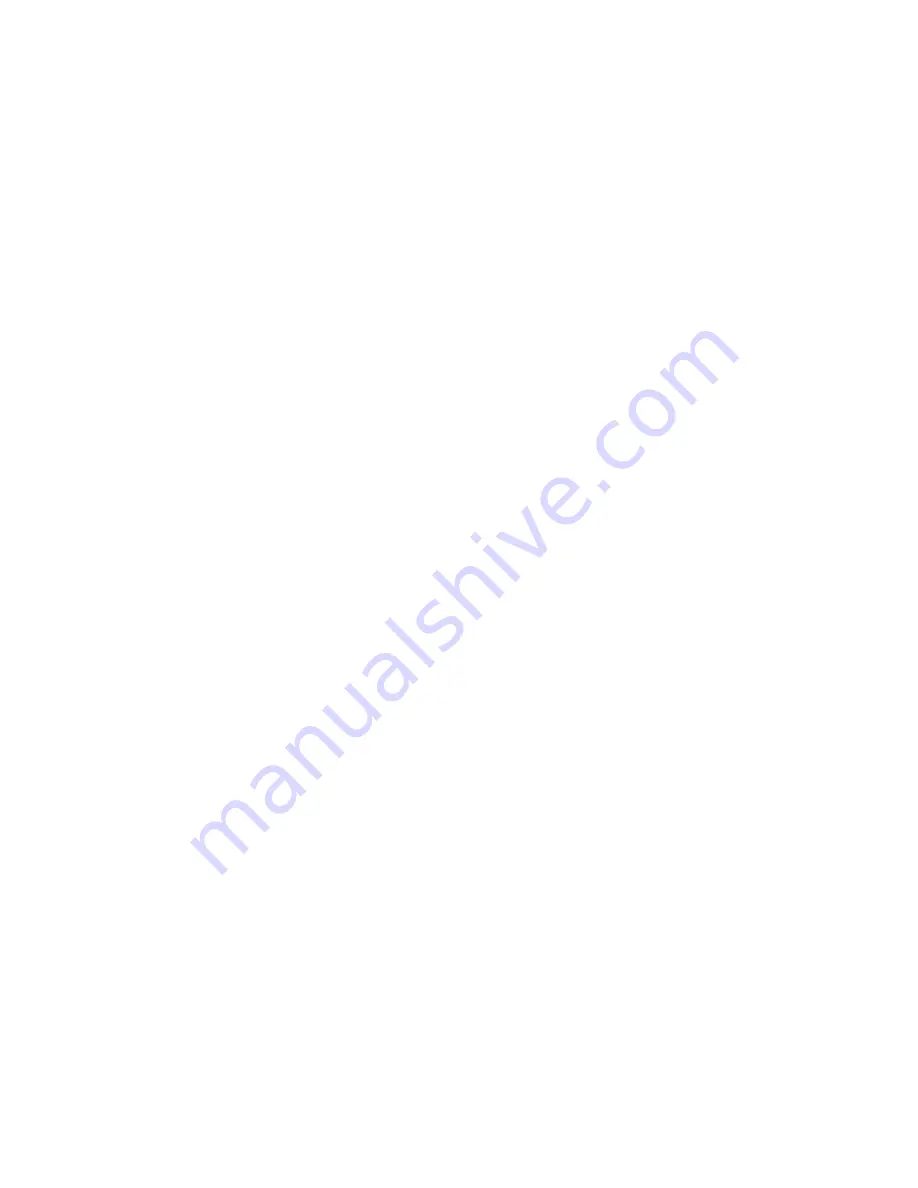
6-10
6-7
ENGINE PRE-OILING
It is important that all engine internal moving parts be properly lubricated before initial
running of engine. Pre-oil engine prior to initial engine operation according to the following
procedure:
1. Pre-oiling may be accomplished using a bladder type pressure pot capable of holding at
least (1) gallon of clean aviation engine oil with an output pressure of 50 not to exceed
60 psi. See Section 7-2, "Approved Ashless Dispersant Oils," for proper type of oil to
use. See Section 1-10, "Operating Limits," for proper seasonal oil grade.
2. Remove rocker box covers from cylinders. Connect pre-oiler supply hose to engine oil
pressure gage line connection (fitting). Open pre-oiler valve and watch cylinder rocker
areas for indication of oil flow. Some engines may take as long as twenty (20) minutes
for oil indication depending on oil temperature.
3. After oil flow has been confirmed, re-install rocker covers using new gaskets, torque
rocker cover screws to limit specified in the L/TSIO-360 Overhaul Manual, Form OH-08.
Close valve on pre-oiler. Disconnect pre-oiler supply hose and cap or re-install engine
oil pressure gage line on pressure gage line connection (fitting) as applicable.
4. Check engine oil gage rod (dipstick) and service to correct capacity. Engine is now
ready for initial run-up and test.
CAUTION . . . Recheck the oil level in the sump. Do not operate the engine with more or
less than the oil sump capacity. See Sections 1-10, "Operating Limits" and 7-1, "Servicing
Oil," for correct grade oil, sump capacity and servicing points.
If the magneto attaching nuts were loosened or the magnetos rotated during engine
installation, magneto to engine timing must be adjusted to specification prior to starting. See
Section 12-5 Ignition System Maintenance of this manual.
Apply Champion® thread lubricant to spark plugs in accordance with the manufacturer's
instructions (see Chapter 3). Install the upper spark plugs and torque to 300-360 inch
pounds.
Install the ignition harness "B" nuts on the spark plugs. The nuts are stamped with a
position identifier, i.e. "1t" which means the top spark plug of the number one cylinder.
6-8
PREFLIGHT AND RUN-UP
NOTE . . . Engines that have a complete set of overhauled or new cylinders and new piston
rings installed must be serviced with Engine Break-In and Preservation oil conforming with
MIL-C-6529 TYPE II until it has been determined that the engine oil consumption has
stabilized (approximately 25 hours of operation.)
Thereafter, the engine must be serviced with the appropriate grade (depending on ambient
temperature) of ashless dispersant oil. See Section 7-2, "Approved Ashless Dispersant
Oils."
Start the engine in accordance with the procedures in the airframe manufacturer's Airplane
Flight Manual (AFM).
High power ground operation resulting in cylinder and oil temperatures exceeding normal
operating limits can be detrimental to cylinders, pistons, valves and rings.
The fuel system must be adjusted prior to flight in accordance with this manual. See Chapter
23, "Fuel System Adjustment."
An operational inspection in accordance with section 5-3 of this manual must be performed
prior to releasing the aircraft for test flight. The operational inspection must be performed to
insure that no induction system, exhaust system, oil system, fuel system leaks or any other
Summary of Contents for TSIO-360-RB
Page 11: ...1 5 FIGURE 1 1 Engine Description L TSIO 360 RB ...
Page 12: ...1 6 FIGURE 1 2 ENGINE DESCRIPTION L TSIO 360 RB Cont d ...
Page 13: ...1 7 FIGURE 1 2 ENGINE DESCRIPTION L TSIO 360 RB Cont d ...
Page 14: ...1 8 FIGURE 1 2 ENGINE DESCRIPTION L TSIO 360 RB Cont d ...
Page 15: ...1 9 FIGURE 1 2 ENGINE DESCRIPTION L TSIO 360 RB Cont d ...
Page 25: ...3 1 CHAPTER 3 SEALANTS AND LUBRICANTS Sealants Lubricants 3 2 ...
Page 32: ...4 2 INTENTIONALLY LEFT BLANK ...
Page 54: ...6 2 INTENTIONALLY LEFT BLANK ...
Page 58: ...6 6 FIGURE 6 1 INSTALLATION DRAWING ...
Page 59: ...6 7 FIGURE 6 1 INSTALLATION DRAWING cont d ...
Page 60: ...6 8 FIGURE 6 1 INSTALLATION DRAWING cont d ...
Page 61: ...6 9 FIGURE 6 1 INSTALLATION DRAWING cont d ...
Page 64: ...6 12 INTENTIONALLY LEFT BLANK ...
Page 70: ...7 6 INTENTIONALLY LEFT BLANK ...
Page 82: ...10 2 INTENTIONALLY LEFT BLANK ...
Page 85: ...11 3 FIGURE 11 1 INDUCTION AND EXHAUST SYSTEM ...
Page 94: ...11 12 INTENTIONALLY LEFT BLANK ...
Page 110: ...12 16 INTENTIONALLY LEFT BLANK ...
Page 124: ...14 4 INTENTIONALLY LEFT BLANK ...
Page 128: ...15 4 INTENTIONALLY LEFT BLANK ...
Page 132: ...16 4 INTENTIONALLY LEFT BLANK ...
Page 139: ...17 7 FIGURE 17 4 STARTER ADAPTER FITS LIMITS ...
Page 140: ...17 8 INTENTIONALLY LEFT BLANK ...
Page 143: ...18 3 FIGURE 18 1 ACCESSORY CASE DESCRIPTION ...
Page 147: ...19 3 FIGURE 19 1 LUBRICATION SYSTEM SCHEMATIC ...
Page 149: ...19 5 ACCESSORY CASE INTERNAL VIEW TSIO 360 FIGURE 19 2 OIL PUMP DESCRIPTION TSIO 360 ...
Page 150: ...19 6 ACCESSORY CASE INTERNAL VIEW LTSIO 360 FIGURE 19 3 OIL PUMP DESCRIPTION LTSIO 360 ...
Page 158: ...19 14 INTENTIONALLY LEFT BLANK ...
Page 181: ...21 3 FIGURE 21 1 CRANKCASE DESCRIPTION ...
Page 186: ...21 8 INTENTIONALLY LEFT BLANK ...
Page 194: ...22 8 INTENTIONALLY LEFT BLANK ...
Page 203: ...23 9 FIGURE 23 6 CONSTANT SPEED SEA LEVEL PERFORMANCE CURVE ...
Page 204: ...23 10 FIGURE 23 7 FUEL FLOW VS METERED FUEL PRESSURE ...
Page 205: ...23 11 FIGURE 23 8 FUEL FLOW VS BRAKE HORSEPOWER ...