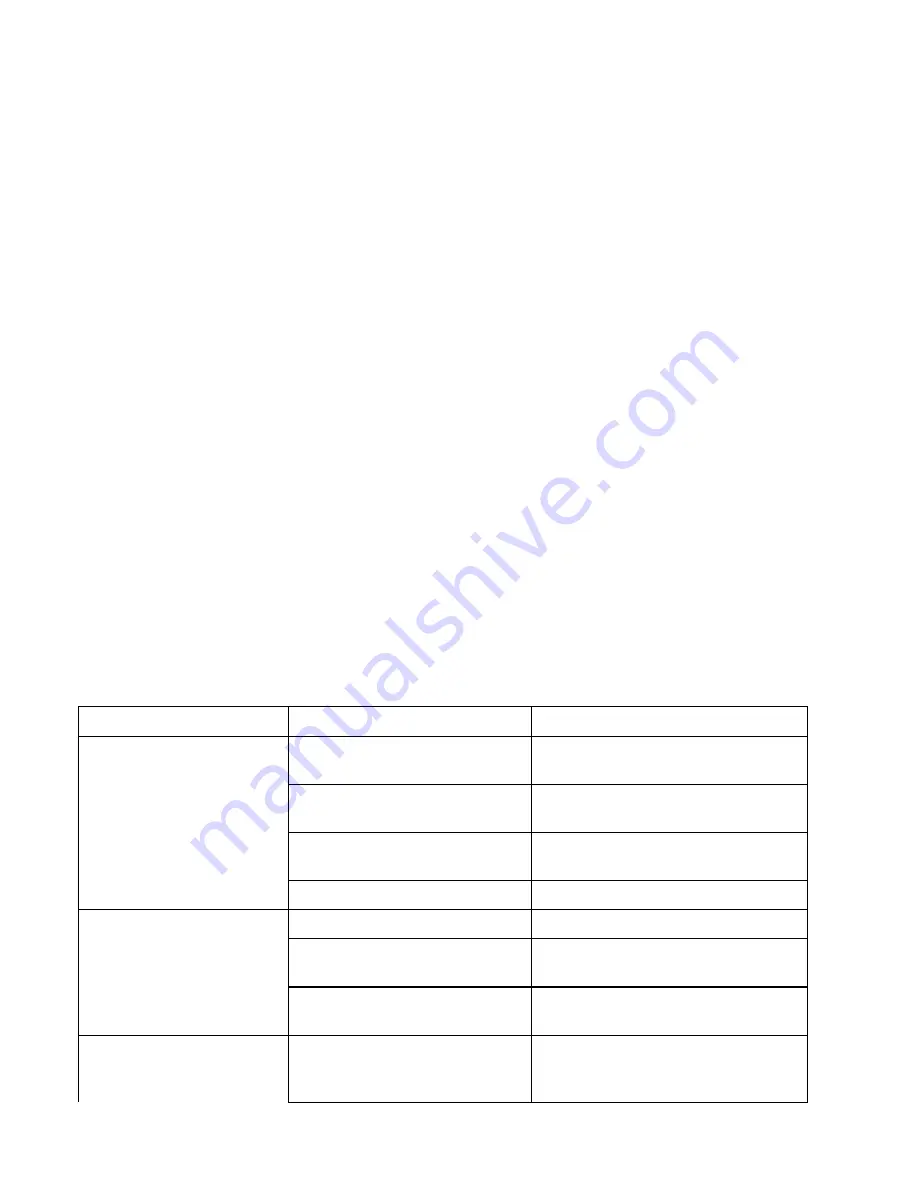
19-10
Using an oil filter can cutter (See Chapter 2 Tools), open filter can and inspect filter
element for debris. If no foreign particles are present, insure oil filter adapter is clean,
lubricate oil filter seal using Dow Corning® DC-4 compound and install new oil filter.
Torque oil filter to 192-216 inch pounds. Safety as required in accordance with Section 9-
2," Lockwire Procedure." If debris is detected on filter element, see Section 19-5," Oil
Filter.
"
NOTE. . . Oil and filter change intervals may vary depending on the type of oil filter used.
See Section 5-2," Oil And Filter Change Interval."
NOTE. . . If the aircraft is exposed to severe conditions, such as training, extreme weather
or infrequent operation, oil change hourly intervals should be decreased.
Install oil sump plug, torque to 190-210 inch pounds. Safety wire in accordance with
Section 9-2," Lockwire Procedure." Refill engine with clean aviation engine oil of the
proper grade and weight, to the correct engine oil quantity in accordance with Chapter 7,
"Servicing Oil."
CAUTION. . . Use only TCM approved oils after break in period. See chapter 7 for TCM
approved oils.
Visually inspect oil sump to crankcase attaching hardware and oil sump drain plug for
security and safetying.
Visually inspect all lubrication system component gasket areas for
oil leaks. Visually inspect all lubrication system components for cracks, dents, stripped
threads, punctures and abnormal wear. Visually inspect oil pressure gauge plumbing for
oil leaks, security and deterioration. Any components exhibiting cracks, dents, punctures
or that are worn beyond serviceable limits must be discarded and replaced with new.
100 HOUR
- Perform all inspection requirements of 50 hour inspection and the following.
If oil pressure does not conform with 10 psi minimum 30 to 60 psi normal operation and
100 psi maximum (oil cold) pressure determine the cause and adjust or repair as required.
19-4
LUBRICATION SYSTEM TROUBLESHOOTING
This troubleshooting chart is provided as a guide. Review all probable causes given.
Check other listings of troubles with similar symptoms. Items are presented in sequence
of the approximate ease of checking, not necessarily in order of probability.
TROUBLE
PROBABLE CAUSE
CORRECTION
Oil leakage
Replace leaking oil lines, torque loose
connections, see Section 19-5.
Excessive Oil Consumption
(See Excessive Crankcase
Pressures, See Section 19-5),
Gasket or seal leakage
Replace gasket or oil seals, see Section
19-5.
Improper seasonal weight or grade oil Service engine with proper oil, see Chapter
7, "Servicing Oil".
Worn piston rings or valve guides
See Section 19-6, "Pistons".
High Oil Temperature Indication
Low oil supply, Replenish
See Chapter 7, "Servicing Oil".
Cooler air passages clogged
Clean thoroughly, see Section 19-5. "Oil
Cooler".
Cooler core plugged
Remove cooler and flush thoroughly, see
Section 19-5, "Oil Cooler".
Thermostat damaged or held open by
solid matter
Remove clean valve and seat. If still
inoperative, replace. See Section 19-5,
"Oil Temperature Control Valve".
Summary of Contents for TSIO-360-RB
Page 11: ...1 5 FIGURE 1 1 Engine Description L TSIO 360 RB ...
Page 12: ...1 6 FIGURE 1 2 ENGINE DESCRIPTION L TSIO 360 RB Cont d ...
Page 13: ...1 7 FIGURE 1 2 ENGINE DESCRIPTION L TSIO 360 RB Cont d ...
Page 14: ...1 8 FIGURE 1 2 ENGINE DESCRIPTION L TSIO 360 RB Cont d ...
Page 15: ...1 9 FIGURE 1 2 ENGINE DESCRIPTION L TSIO 360 RB Cont d ...
Page 25: ...3 1 CHAPTER 3 SEALANTS AND LUBRICANTS Sealants Lubricants 3 2 ...
Page 32: ...4 2 INTENTIONALLY LEFT BLANK ...
Page 54: ...6 2 INTENTIONALLY LEFT BLANK ...
Page 58: ...6 6 FIGURE 6 1 INSTALLATION DRAWING ...
Page 59: ...6 7 FIGURE 6 1 INSTALLATION DRAWING cont d ...
Page 60: ...6 8 FIGURE 6 1 INSTALLATION DRAWING cont d ...
Page 61: ...6 9 FIGURE 6 1 INSTALLATION DRAWING cont d ...
Page 64: ...6 12 INTENTIONALLY LEFT BLANK ...
Page 70: ...7 6 INTENTIONALLY LEFT BLANK ...
Page 82: ...10 2 INTENTIONALLY LEFT BLANK ...
Page 85: ...11 3 FIGURE 11 1 INDUCTION AND EXHAUST SYSTEM ...
Page 94: ...11 12 INTENTIONALLY LEFT BLANK ...
Page 110: ...12 16 INTENTIONALLY LEFT BLANK ...
Page 124: ...14 4 INTENTIONALLY LEFT BLANK ...
Page 128: ...15 4 INTENTIONALLY LEFT BLANK ...
Page 132: ...16 4 INTENTIONALLY LEFT BLANK ...
Page 139: ...17 7 FIGURE 17 4 STARTER ADAPTER FITS LIMITS ...
Page 140: ...17 8 INTENTIONALLY LEFT BLANK ...
Page 143: ...18 3 FIGURE 18 1 ACCESSORY CASE DESCRIPTION ...
Page 147: ...19 3 FIGURE 19 1 LUBRICATION SYSTEM SCHEMATIC ...
Page 149: ...19 5 ACCESSORY CASE INTERNAL VIEW TSIO 360 FIGURE 19 2 OIL PUMP DESCRIPTION TSIO 360 ...
Page 150: ...19 6 ACCESSORY CASE INTERNAL VIEW LTSIO 360 FIGURE 19 3 OIL PUMP DESCRIPTION LTSIO 360 ...
Page 158: ...19 14 INTENTIONALLY LEFT BLANK ...
Page 181: ...21 3 FIGURE 21 1 CRANKCASE DESCRIPTION ...
Page 186: ...21 8 INTENTIONALLY LEFT BLANK ...
Page 194: ...22 8 INTENTIONALLY LEFT BLANK ...
Page 203: ...23 9 FIGURE 23 6 CONSTANT SPEED SEA LEVEL PERFORMANCE CURVE ...
Page 204: ...23 10 FIGURE 23 7 FUEL FLOW VS METERED FUEL PRESSURE ...
Page 205: ...23 11 FIGURE 23 8 FUEL FLOW VS BRAKE HORSEPOWER ...