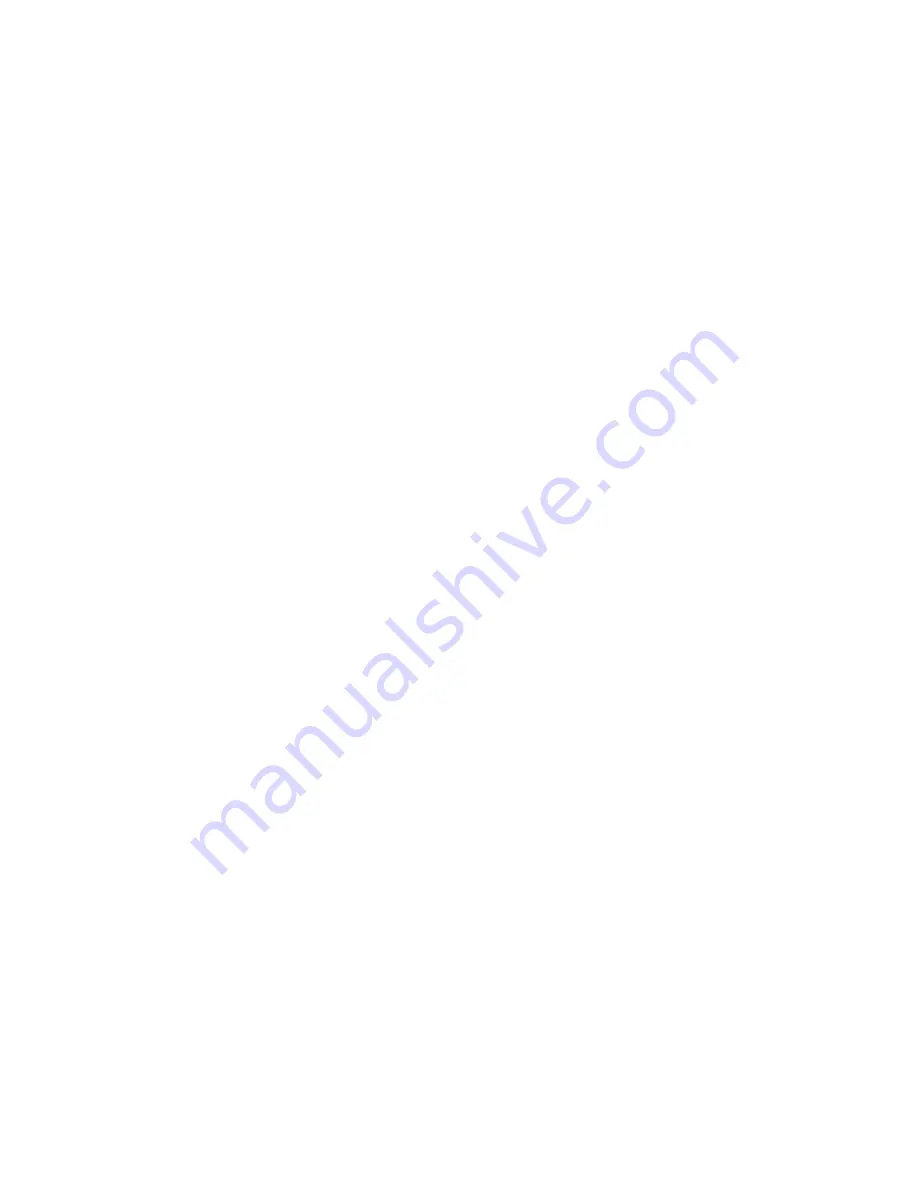
5-9
WARNING
Insure fuel selector is in the off position prior to removing the fuel metering unit inlet
screen.
13. Inspect fuel nozzles, upper deck and fuel injection nozzle reference lines, hoses,
manifolds and fittings for proper routing, support and signs of fuel stains. Inspect
manifold valve for security of installation, proper venting and signs of fuel stains.
14. At the first 100-hour inspection on new, rebuilt or overhauled engines, remove fuel
injection nozzles. Clean nozzles by soaking in lacquer thinner, acetone or methyl ethyl
ketone (MEK). Fuel nozzles must be cleaned every 300-hours or annual inspection.
NOTE . . .
Any environmentally hazardous materials used in cleaning must be contained and
disposed of in accordance with Environmental Protection Agency regulations.
CAUTION ... Never clean nozzles with wire or other similar object. If nozzle jet is plugged and
obstruction cannot be removed by solvent action, REPLACE THE NOZZLE.
15. Inspect all accessories for condition, security of mounting and proper operation. Refer to
aircraft or component manufacturer's Maintenance Manual for specifics.
16. Inspect engine mount legs for cracks. Check engine mount isolators for signs of
deterioration, proper assembly and security.
17. Check all fasteners for integrity and security.
18. Visually inspect the turbocharger center housing for general condition. Inspect the
compressor housing "V" band clamp for security. Inspect the exhaust housing bolts and
lock tabs for security. Inspect the oil inlet and outlet fittings and surrounding area for
evidence of oil leakage.
19. Remove the induction air supply duct to the turbocharger compressor and inspect the
compressor blades for evidence of foreign object damage. Turn compressor wheel by
hand, check for freedom of rotation. Inspect the interior of the air supply duct for general
condition.
20. Remove the turbocharger exhaust stack and inspect the turbine wheel for damage,
freedom of rotation and evidence of oil.
21. Visually inspect exhaust system transition unit at the turbocharger for general condition
and evidence of exhaust leaks, cracks and distortion.
22. Verify operation and accuracy of EGT/TIT system. Note: The aircraft manufacturer may
require the EGT/TIT system to be operational for all categories of flight. Check the
limitations section of the Airplane Flight Manual for specific requirements. Calibration of
the EGT/TIT system may be mandatory at 100 hour intervals. Consult the aircraft
manufacturer's Maintenance Manual for specific instructions.
23. Remove the turbocharger compressor discharge duct and inspect the interior for
evidence of oil. If there is evidence of oil in the duct, further inspection of the
turbocharger is required to determine cause and source of oil. Refer to the turbocharger
manufacturer's information for specific instructions.
24. Inspect all turbocharger control system linkage for correct rigging, looseness and
lubricate link rod pins with Permatex Maintain® Lubricant.
25. Inspect waste gate actuator and butterfly valve for general condition and freedom of
movement. Check link rod pins and levers for wear. Lubricate waste gate butterfly valve
with "Mouse Milk".
Summary of Contents for TSIO-360-RB
Page 11: ...1 5 FIGURE 1 1 Engine Description L TSIO 360 RB ...
Page 12: ...1 6 FIGURE 1 2 ENGINE DESCRIPTION L TSIO 360 RB Cont d ...
Page 13: ...1 7 FIGURE 1 2 ENGINE DESCRIPTION L TSIO 360 RB Cont d ...
Page 14: ...1 8 FIGURE 1 2 ENGINE DESCRIPTION L TSIO 360 RB Cont d ...
Page 15: ...1 9 FIGURE 1 2 ENGINE DESCRIPTION L TSIO 360 RB Cont d ...
Page 25: ...3 1 CHAPTER 3 SEALANTS AND LUBRICANTS Sealants Lubricants 3 2 ...
Page 32: ...4 2 INTENTIONALLY LEFT BLANK ...
Page 54: ...6 2 INTENTIONALLY LEFT BLANK ...
Page 58: ...6 6 FIGURE 6 1 INSTALLATION DRAWING ...
Page 59: ...6 7 FIGURE 6 1 INSTALLATION DRAWING cont d ...
Page 60: ...6 8 FIGURE 6 1 INSTALLATION DRAWING cont d ...
Page 61: ...6 9 FIGURE 6 1 INSTALLATION DRAWING cont d ...
Page 64: ...6 12 INTENTIONALLY LEFT BLANK ...
Page 70: ...7 6 INTENTIONALLY LEFT BLANK ...
Page 82: ...10 2 INTENTIONALLY LEFT BLANK ...
Page 85: ...11 3 FIGURE 11 1 INDUCTION AND EXHAUST SYSTEM ...
Page 94: ...11 12 INTENTIONALLY LEFT BLANK ...
Page 110: ...12 16 INTENTIONALLY LEFT BLANK ...
Page 124: ...14 4 INTENTIONALLY LEFT BLANK ...
Page 128: ...15 4 INTENTIONALLY LEFT BLANK ...
Page 132: ...16 4 INTENTIONALLY LEFT BLANK ...
Page 139: ...17 7 FIGURE 17 4 STARTER ADAPTER FITS LIMITS ...
Page 140: ...17 8 INTENTIONALLY LEFT BLANK ...
Page 143: ...18 3 FIGURE 18 1 ACCESSORY CASE DESCRIPTION ...
Page 147: ...19 3 FIGURE 19 1 LUBRICATION SYSTEM SCHEMATIC ...
Page 149: ...19 5 ACCESSORY CASE INTERNAL VIEW TSIO 360 FIGURE 19 2 OIL PUMP DESCRIPTION TSIO 360 ...
Page 150: ...19 6 ACCESSORY CASE INTERNAL VIEW LTSIO 360 FIGURE 19 3 OIL PUMP DESCRIPTION LTSIO 360 ...
Page 158: ...19 14 INTENTIONALLY LEFT BLANK ...
Page 181: ...21 3 FIGURE 21 1 CRANKCASE DESCRIPTION ...
Page 186: ...21 8 INTENTIONALLY LEFT BLANK ...
Page 194: ...22 8 INTENTIONALLY LEFT BLANK ...
Page 203: ...23 9 FIGURE 23 6 CONSTANT SPEED SEA LEVEL PERFORMANCE CURVE ...
Page 204: ...23 10 FIGURE 23 7 FUEL FLOW VS METERED FUEL PRESSURE ...
Page 205: ...23 11 FIGURE 23 8 FUEL FLOW VS BRAKE HORSEPOWER ...