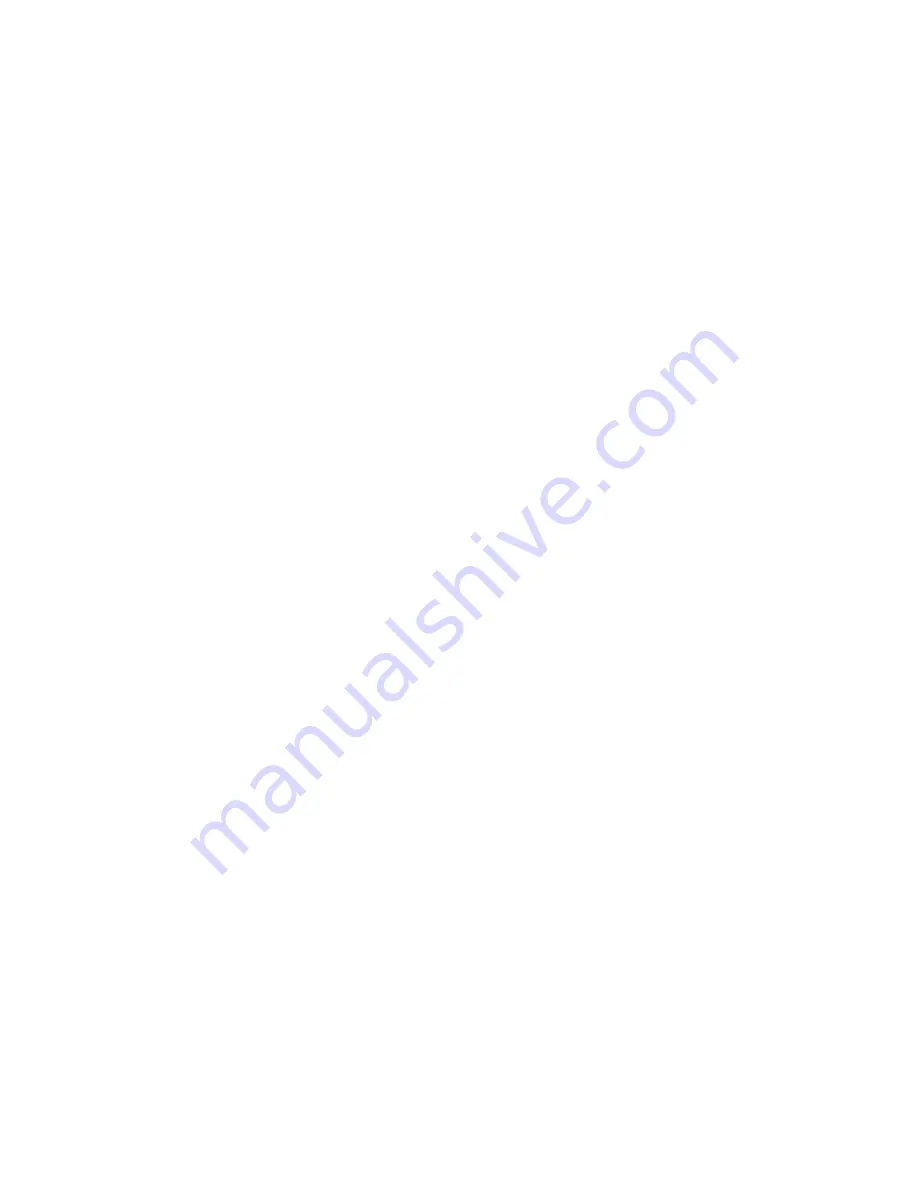
20-11
1. Perform the test as soon as possible after the engine is shut down to insure that the piston
rings, cylinder walls, and other engine parts are well lubricated and at operating conditions.
2. Turn the crankshaft by hand in the direction of rotation until the piston, in the cylinder being
checked, is coming up on its compression stroke.
3. Install an adapter in the spark plug hole and connect the calibrated differential pressure
tester to the adapter. (NOTE: Cylinder pressure valve is in the Closed position). Slowly
open the cylinder pressure valve and pressurize the cylinder, not to exceed 20 pounds per
square inch. Continue rotating the engine against this pressure until the piston reaches top
dead center. Reaching top dead center is indicated by a flat spot or sudden decrease in
force required to turn the crankshaft. If the crankshaft is rotated too far, back up at least
one-half revolution and start over again to eliminate the effect of backlash in the valve
operating mechanism and to keep the piston rings seated on the lower ring lands. This is
critical because the slightest movement breaks this piston ring sealing and allows the
pressure to drop.
WARNING
Care must be exercised in opening the cylinder pressure valve, since sufficient air
pressure will be built up in the cylinder causing it to rotate the crankshaft if the
piston is not at top dead center. The propeller must be secured during check to
prevent rotation.
4. Open the cylinder pressure valve completely. Check the regulator pressure gauge and
adjust, if necessary to 80 pounds per square inch.
5. Observe the pressure indication on the cylinder pressure gage. The difference between
this pressure and the pressure shown by the regulator pressure gauge is the amount of
leakage through the cylinder. If the cylinder pressure gauge reading is higher than the
previously determined master orifice calibrated pressure reading, proceed to the next
cylinder and perform leak check. If the cylinder pressure gauge reading is lower, proceed
with the following:
NOTE. . . Document cylinder compression pressure.
Static Seal Check(See Figure 20-8, "Static Seal.")
6. First check the static seal for leakage. Positive identification of static seal leakage is
possible by listening for air flow sound at the exhaust or induction system port. When
checking for cylinder head to barrel leakage, use a soapy solution between the fins and
watch for bubbles. Use a soapy solution around both spark plug seals for leakage. NO
LEAKAGE IS ALLOWED IN STATIC SEALS.
7. If leakage is occurring in the intake or exhaust valve areas, See Section 20-6, "Cylinder
Maintenance" for staking valves. Leakage by the valves must be eliminated before a
dynamic seal check can be performed.
8. If leakage is noted between the cylinder head and barrel, REPLACE THE CYLINDER, See
Section 20-6, "Cylinder Maintenance."
Dynamic Seal Check (See Figure 20-9, "Dynamic Seal.")
9. To check the dynamic seal of a cylinder, proceed with the leakage test and observe the
pressure indication of the cylinder pressure gauge. The difference between this pressure
and the pressure shown by the regulator gauge is the amount of leakage at the dynamic
seal.
Summary of Contents for TSIO-360-RB
Page 11: ...1 5 FIGURE 1 1 Engine Description L TSIO 360 RB ...
Page 12: ...1 6 FIGURE 1 2 ENGINE DESCRIPTION L TSIO 360 RB Cont d ...
Page 13: ...1 7 FIGURE 1 2 ENGINE DESCRIPTION L TSIO 360 RB Cont d ...
Page 14: ...1 8 FIGURE 1 2 ENGINE DESCRIPTION L TSIO 360 RB Cont d ...
Page 15: ...1 9 FIGURE 1 2 ENGINE DESCRIPTION L TSIO 360 RB Cont d ...
Page 25: ...3 1 CHAPTER 3 SEALANTS AND LUBRICANTS Sealants Lubricants 3 2 ...
Page 32: ...4 2 INTENTIONALLY LEFT BLANK ...
Page 54: ...6 2 INTENTIONALLY LEFT BLANK ...
Page 58: ...6 6 FIGURE 6 1 INSTALLATION DRAWING ...
Page 59: ...6 7 FIGURE 6 1 INSTALLATION DRAWING cont d ...
Page 60: ...6 8 FIGURE 6 1 INSTALLATION DRAWING cont d ...
Page 61: ...6 9 FIGURE 6 1 INSTALLATION DRAWING cont d ...
Page 64: ...6 12 INTENTIONALLY LEFT BLANK ...
Page 70: ...7 6 INTENTIONALLY LEFT BLANK ...
Page 82: ...10 2 INTENTIONALLY LEFT BLANK ...
Page 85: ...11 3 FIGURE 11 1 INDUCTION AND EXHAUST SYSTEM ...
Page 94: ...11 12 INTENTIONALLY LEFT BLANK ...
Page 110: ...12 16 INTENTIONALLY LEFT BLANK ...
Page 124: ...14 4 INTENTIONALLY LEFT BLANK ...
Page 128: ...15 4 INTENTIONALLY LEFT BLANK ...
Page 132: ...16 4 INTENTIONALLY LEFT BLANK ...
Page 139: ...17 7 FIGURE 17 4 STARTER ADAPTER FITS LIMITS ...
Page 140: ...17 8 INTENTIONALLY LEFT BLANK ...
Page 143: ...18 3 FIGURE 18 1 ACCESSORY CASE DESCRIPTION ...
Page 147: ...19 3 FIGURE 19 1 LUBRICATION SYSTEM SCHEMATIC ...
Page 149: ...19 5 ACCESSORY CASE INTERNAL VIEW TSIO 360 FIGURE 19 2 OIL PUMP DESCRIPTION TSIO 360 ...
Page 150: ...19 6 ACCESSORY CASE INTERNAL VIEW LTSIO 360 FIGURE 19 3 OIL PUMP DESCRIPTION LTSIO 360 ...
Page 158: ...19 14 INTENTIONALLY LEFT BLANK ...
Page 181: ...21 3 FIGURE 21 1 CRANKCASE DESCRIPTION ...
Page 186: ...21 8 INTENTIONALLY LEFT BLANK ...
Page 194: ...22 8 INTENTIONALLY LEFT BLANK ...
Page 203: ...23 9 FIGURE 23 6 CONSTANT SPEED SEA LEVEL PERFORMANCE CURVE ...
Page 204: ...23 10 FIGURE 23 7 FUEL FLOW VS METERED FUEL PRESSURE ...
Page 205: ...23 11 FIGURE 23 8 FUEL FLOW VS BRAKE HORSEPOWER ...