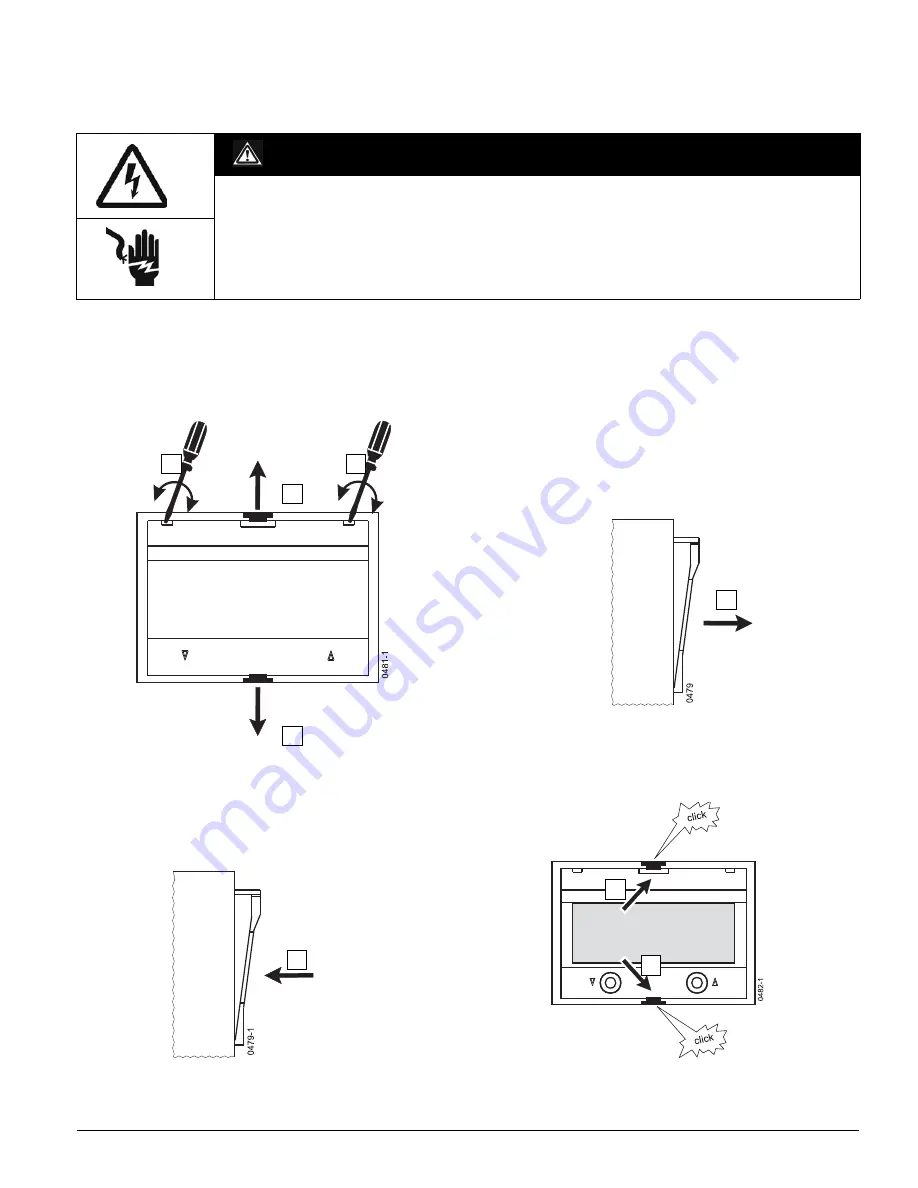
9 – 19
Field installation
The trip units ETU745 and ETU748 can be field installed with an alphanumeric display.
- OPEN circuit breaker and discharge the closing spring
- Disconnect external 24 V DC voltage supply, if applicable
- Remove sealing cap of trip unit, if applicable
Removing dummy flange
Installing display and latching it tight
- Fit and seal trip unit sealing cap, if applicable
- Reconnect external 24 V DC voltage supply, if applicable
DANGER
Hazardous voltage.
Will cause death, serious personal injury, or equipment damage.
Turn off and lock out all power supplying this device before working on this device.
1
2
3
4
5
1
2
3
Summary of Contents for UL 1066
Page 56: ...7 5 7 2 Frame size II fused ...
Page 58: ...7 7 ...
Page 63: ...7 12 8 27 210 0 8 27 210 0 8 27 210 0 3 75 95 2 ...
Page 64: ...7 13 ...
Page 65: ...7 14 7 7 Frame size III fuse carriage ...
Page 66: ...7 15 ...
Page 69: ...7 18 7 9 External sensor for neutral conductor WLNCT2 ...
Page 70: ...7 19 WLNCT3 ...
Page 85: ...9 5 I tripping Ground fault tripping ...
Page 231: ...15 12 Pre assembling the locking module Installing 0767 1 2 3 4 6 5 ...
Page 232: ...15 13 1 Socket head cap screw M5 with washer and nut 7 8 Size 4 5 Nm 45 lb in ...
Page 289: ...23 7 23 3 3 Installing arc chutes 1 2 6 5 PH 2 0043 02 3 4 5 6 For frame size III 3 PH 2 ...
Page 298: ...23 16 6 7 8 9 5 2 1 Size 5 mm ...
Page 333: ......