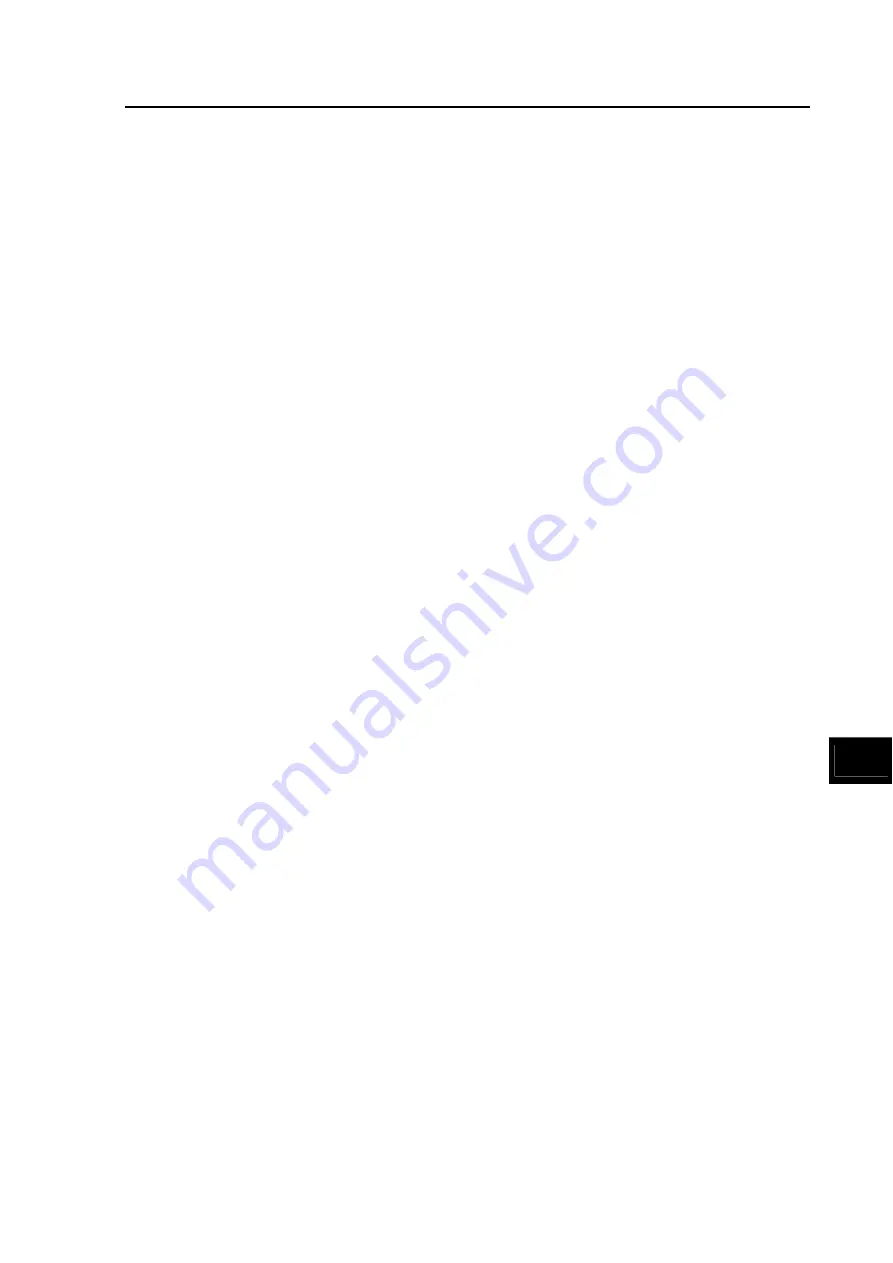
Commissioning and Maintenance
P746/EN
CM/F21
MiCOM P746
(CM) 10-17
CM
6. SETTING
CHECKS
The setting checks ensure that all of the application-specific relay settings (i.e. both the
relay’s function and programmable scheme logic settings), for the particular installation, have
been correctly applied to the relay.
Note 1:
The trip circuits should remain isolated during these checks to prevent
accidental operation of the associated circuit breaker.
Note 2:
For busbar protection stability reasons, whatever is the maintenance
mode selected, the Check Zone will never be disabled, thus, the time
to inject current shall be shorter than the ID>1 set timer to avoid
Circuitry Fault alarms.
6.1
Apply application-specific settings
There are two methods of applying the settings to the relay:
−
Transferring them from a pre-prepared setting file to the relay using a portable PC
running the appropriate software via the relay’s front EIA(RS)232 port, located under
the bottom access cover. This method is preferred for transferring function settings as
it is much faster and there is less margin for error. If the programmable scheme logic
other than the default settings with which the relay is supplied is to be used then this is
the only way of changing the settings.
If a setting file has been created for the particular application and provided on a digital
medium, this will further reduce the commissioning time and should always be the
case where application-specific programmable scheme logic is to be applied to the
relay.
−
Enter them manually via the relay’s operator interface. This method is not suitable for
changing the programmable scheme logic.
Note: It is essential that where the installation needs application-specific
Programmable Scheme Logic, that the appropriate .psl file is downloaded
(sent) to the relay, for each and every setting group that will be used. If the
user fails to download the required .psl file to any setting group that may be
brought into service, then factory default PSL will still be resident. This may
have severe operational and safety consequences.
6.2
Demonstrate Correct Relay Operation
The purpose of these tests is as follows:
−
To determine that the primary protection function of the relay, current differential, can
trip according to the correct application settings.
−
To verify correct setting of any phase overcurrent protection.
−
To verify correct assignment of the inputs, relays and trip contacts, by monitoring the
response to a selection of fault injections.
6.2.1 Current
Differential Bias Characteristic
To avoid spurious operation of any Overcurrent, earth fault or breaker fail elements, these
should be disabled for the duration of the differential element tests. This is done in the relay’s
CONFIGURATION column. Ensure that cells, [Overcurrent Prot], [Earth Fault Prot] and [CB
Fail & I<] are all set to “Disabled”. Make a note of which elements need to be re-enabled
after testing.
Summary of Contents for MiCOM P746
Page 4: ......
Page 5: ...Pxxx EN SS G11 SAFETY SECTION...
Page 6: ......
Page 8: ...Pxxx EN SS G11 Page 2 8 Safety Section BLANK PAGE...
Page 16: ...P746 EN IT G31 Introduction MiCOM P746...
Page 18: ...P746 EN IT G31 Introduction IT 1 2 MiCOM P746 IT BLANK PAGE...
Page 26: ...P746 EN TD G31 Technical Data MiCOM P746...
Page 38: ...P746 EN GS G31 Getting Started MiCOM P746...
Page 78: ...P746 EN ST G31 Getting Started MiCOM P746...
Page 80: ...P746 EN ST G31 Settings ST 4 2 MiCOM P746 ST BLANK PAGE...
Page 112: ...P746 EN ST G31 Settings ST 4 34 MiCOM P746 ST BLANK PAGE...
Page 114: ...P746 EN OP G31 Operation MiCOM P746...
Page 136: ...P746 EN OP G31 Operation OP 5 22 MiCOM P746 OP BLANK PAGE...
Page 138: ...P746 EN AP G31 Application Notes MiCOM P746...
Page 142: ...P746 EN AP G31 Application Notes AP 6 4 MiCOM P746 AP BLANK PAGE...
Page 194: ...P746 EN AP G31 Application Notes AP 6 56 MiCOM P746 AP BLANK PAGE...
Page 196: ...P746 EN PL G31 Programmable Logic MiCOM P746...
Page 238: ...P746 EN MR A11 Measurements and Recording MiCOM P746...
Page 240: ...P746 EN MR A11 Measurements and Recording MR 8 2 MiCOM P746 MR BLANK PAGE...
Page 258: ...P746 EN FD G31 Firmware Design MiCOM P746...
Page 280: ......
Page 348: ...P746 EN MT A11 Maintenance MiCOM P746...
Page 350: ...P746 EN MT A11 Maintenance MT 11 2 MiCOM P746 MT BLANK PAGE...
Page 364: ...P746 EN MT A11 Maintenance MT 11 16 MiCOM P746 MT BLANK PAGE...
Page 366: ...P746 EN TS G31 Troubleshooting MiCOM P746...
Page 368: ...P746 EN TS G31 Troubleshooting TS 12 2 MiCOM P746 TS BLANK PAGE...
Page 382: ...P746 EN SC G31 SCADA Communications MiCOM P746...
Page 424: ...P746 EN SC G31 SCADA Communications SC 13 42 MiCOM P746 SC BLANK PAGE...
Page 426: ...P746 EN SG F21 Symbols and Glossary MiCOM P746...
Page 438: ......
Page 440: ...P746 EN IN G31 Installation IN 15 2 MiCOM P746 IN BLANK PAGE...
Page 468: ......
Page 470: ...P746 EN HI G31 Remote HMI HI 16 2 MiCOM P746 HI BLANK PAGE...
Page 500: ...P746 EN HI G31 Remote HMI HI 16 32 MiCOM P746 HI BLANK PAGE...
Page 502: ......
Page 504: ...P746 EN CS A11G31 Cyber Security CS 17 2 MiCOM P746 CS BLANK PAGE...
Page 524: ...P746 EN VH G31 Firmware and Service Manual Version History MiCOM P746...
Page 529: ......