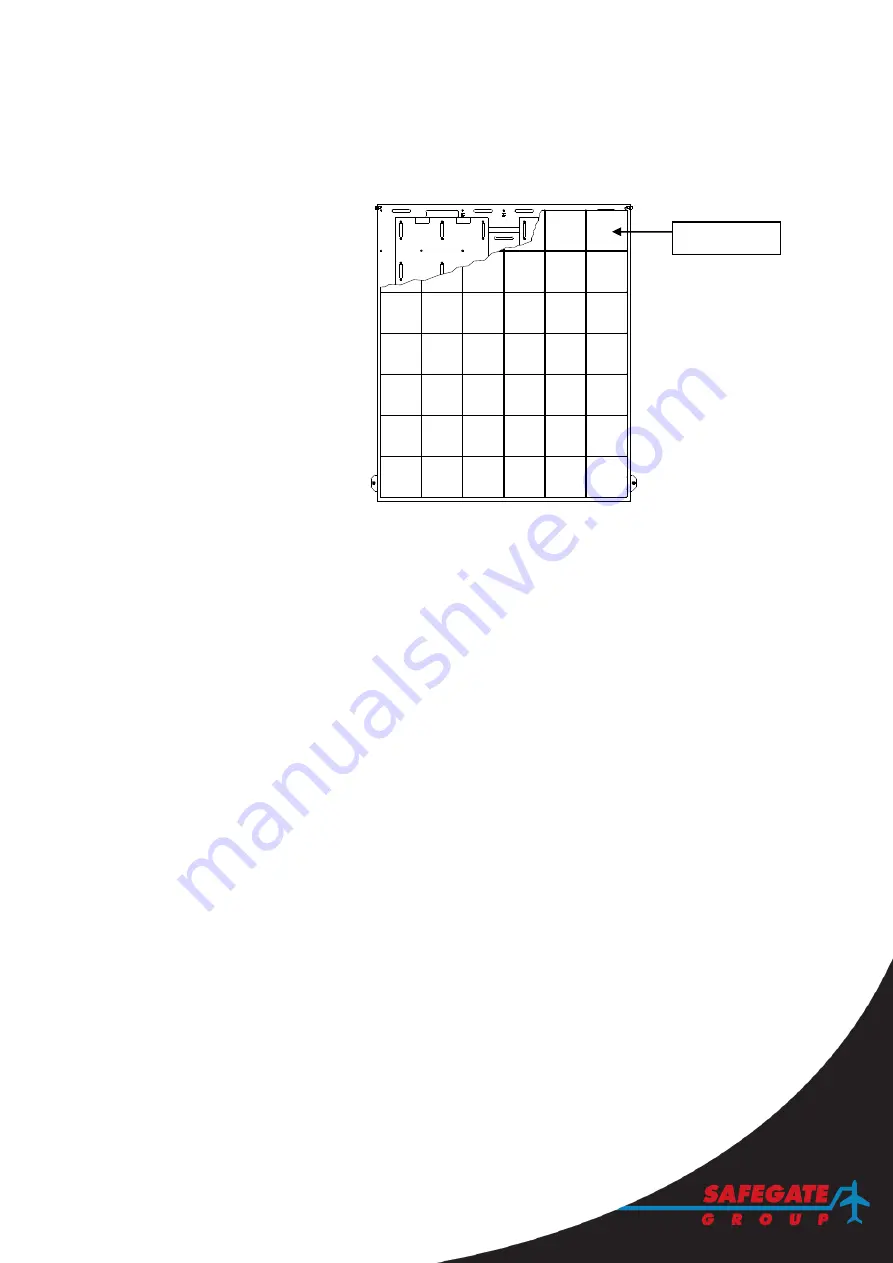
SAFEDOCK®
Safegate Group
Manual
Date: 6 February 2015
Chapter: 4 MAINTENANCE
Version: 2.7
Page 45 of 52
6.8
RENEWAL OF LED MODULE
6.8.1
LED Module Disassembly
The figure below illustrates the LED matrix boards’ connection to the mounting plate.
FIGURE 4.55
– SAFEDOCK T1 LED MODULE
Note
: The front glass is hinged at the top of the display unit.
(a) To gain access to the inside of the display unit, undo and lift the front glass of the
cabinet.
(b) Switch
OFF
and isolate the power supply.
(c) Undo the two lock devices on the outer end of the front glass and let down the
plate with the LED modules on.
(d) Carefully remove the defective LED module.
6.8.2
Inspection
(a) Inspect the front glass for cleanliness. Clean as required.
(b) Inspect the cabinet for extraneous material. Clean as required.
6.8.3
Assembly
(a) Insert the new LED module.
(b) Carefully close the front glass and secure.
6.8.4
Testing
(a) Switch power
ON
.
(b) Run the display test from the Operator Panel to verify the function of the new
board as follows. Push the
Test
key and select
Display Test
and activate
Address test
. The display shows now the alphabet with one letter on each
module. Check if the right letter is displayed on the modules.
LED Module
Summary of Contents for safedock
Page 1: ...SAFEDOCK Manual...
Page 2: ...Note This page is blank for convenient double sided printing...
Page 225: ......
Page 227: ......
Page 228: ......
Page 232: ......
Page 235: ......
Page 236: ......
Page 237: ......
Page 240: ......
Page 241: ......
Page 242: ......
Page 244: ......
Page 245: ......
Page 250: ......
Page 251: ......
Page 252: ......
Page 253: ......
Page 254: ......
Page 255: ......
Page 256: ......
Page 257: ......
Page 259: ......
Page 260: ......
Page 261: ......
Page 263: ......
Page 264: ......
Page 266: ......
Page 267: ......
Page 268: ......
Page 271: ...CANCEL ENTER...
Page 272: ......
Page 273: ...K73 K74...
Page 274: ......
Page 276: ......
Page 277: ......
Page 278: ......
Page 279: ...K73...
Page 280: ......
Page 282: ......
Page 283: ......
Page 284: ......
Page 287: ......
Page 288: ......
Page 289: ......
Page 290: ......
Page 293: ......
Page 294: ......
Page 295: ......
Page 298: ......
Page 299: ......
Page 300: ......
Page 302: ......
Page 304: ......
Page 310: ......
Page 311: ......
Page 312: ......
Page 313: ......
Page 314: ......
Page 315: ......
Page 316: ......
Page 317: ......
Page 318: ......
Page 319: ......
Page 320: ......
Page 321: ......
Page 322: ......
Page 323: ......
Page 324: ......
Page 325: ......
Page 326: ......
Page 327: ......
Page 328: ......
Page 329: ......
Page 335: ......
Page 336: ......
Page 337: ......
Page 340: ......
Page 346: ......
Page 347: ......