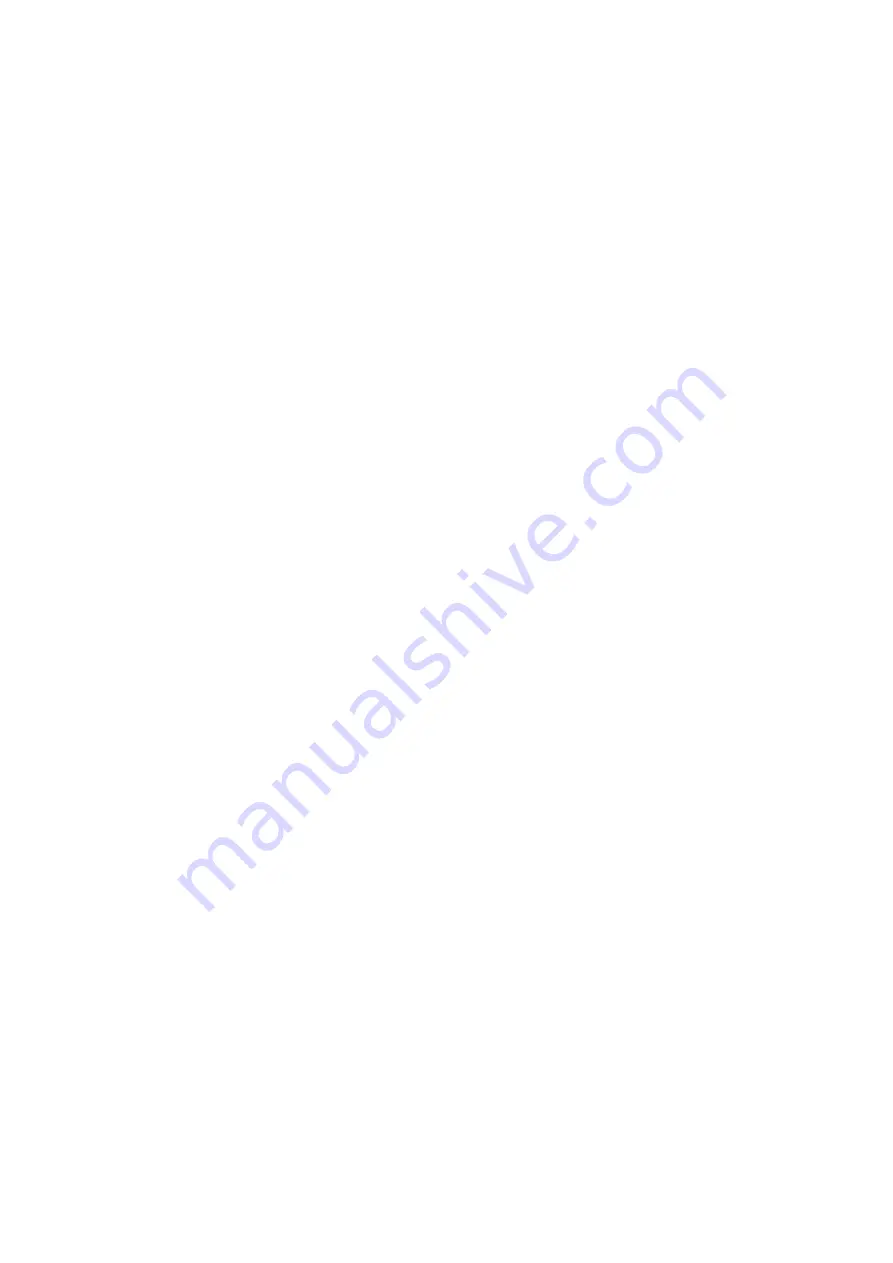
SAFEDOCK®
Safegate Group
Manual
Date: 6 February 2015
Chapter: 4 MAINTENANCE
Version: 2.7
Page 34 of 52
6.4.6
Scan Test
A LASER SCAN ERROR may be caused by one of the following components: stepper
motor, stepper motor card, laser or CU card. The following steps may help to
diagnose which of the components is at fault:
(a) Move one of the mirrors gently by hand. When moving it the LED named LASER
SAFE should light up as an indication of that the stepper motor sensor is detecting
a movement. There should be some resistance when moving the mirror by hand.
If not, the Stepper Motor Driver is possibly broken. Swap the 2 Stepper Motor
Drivers to check if the problem moves to the other stepper motor.
(b) If the LED does not light up, then there is a problem with the cable between the
stepper motor and the CU board, or the stepper motor itself.
6.5
RENEWAL OF CONTROL UNIT
6.5.1
Preparations before Maintenance
Note
: Stand set-up parameters, such as configuration data, calibration values and
aircraft data, are stored in a non-volatile memory of the control unit.
A DISK COPY OF THE STAND SET-UP PARAMETERS SHALL PREVIOUSLY
HAVE BEEN MADE AT THE SAFEDOCK INSTALLATION/SET-UP PHASE AT EACH
STAND.
THIS PROCEDURE HAS BEEN DONE FOR FACILITATING THE EXCHANGE OF
THE CONTROL UNIT IN CASE OF AN ERROR, AND FOR MAKING RESTORATION
OF SOFTWARE AND SET-UP PARAMETERS EASIER AFTER THE EXCHANGE
OF HARDWARE.
THE APPLICABLE STAND SET-UP FILE SHALL BE LOADED INTO THE
MAINTENANCE PC ACCORDING TO INSTRUCTIONS IN
CHAPTER 4A STAND
CONFIGURATION UTILITY.
6.5.2
Dumping Stand Set-Up Parameters from the Control Unit
If the stand parameter back-up file is not available, the procedure described in
Chapter 4A Stand Configuration Utility can be carried out to secure the Stand set-up
parameters, if possible.
(a) Connect the Maintenance PC, loaded with the Safedock Maintenance software,
called SMT.EXE, to the connector at the right side of the Operator Panel.
(b) Dumping the CU memory contents to the PC will be done automatically, as soon
communication between the CU and the PC is established. To make a disk copy,
use
the function “SAVE” in the Safedock Stand Configuration Dialogue Box. The
current configuration will be saved onto disk in the maintenance PC.
If a faulty Control Unit does not allow you to dump its memory contents, the set-up
and calibration procedure has to be done manually again as described in the Chapter
4A Stand Configuration Utility.
Summary of Contents for safedock
Page 1: ...SAFEDOCK Manual...
Page 2: ...Note This page is blank for convenient double sided printing...
Page 225: ......
Page 227: ......
Page 228: ......
Page 232: ......
Page 235: ......
Page 236: ......
Page 237: ......
Page 240: ......
Page 241: ......
Page 242: ......
Page 244: ......
Page 245: ......
Page 250: ......
Page 251: ......
Page 252: ......
Page 253: ......
Page 254: ......
Page 255: ......
Page 256: ......
Page 257: ......
Page 259: ......
Page 260: ......
Page 261: ......
Page 263: ......
Page 264: ......
Page 266: ......
Page 267: ......
Page 268: ......
Page 271: ...CANCEL ENTER...
Page 272: ......
Page 273: ...K73 K74...
Page 274: ......
Page 276: ......
Page 277: ......
Page 278: ......
Page 279: ...K73...
Page 280: ......
Page 282: ......
Page 283: ......
Page 284: ......
Page 287: ......
Page 288: ......
Page 289: ......
Page 290: ......
Page 293: ......
Page 294: ......
Page 295: ......
Page 298: ......
Page 299: ......
Page 300: ......
Page 302: ......
Page 304: ......
Page 310: ......
Page 311: ......
Page 312: ......
Page 313: ......
Page 314: ......
Page 315: ......
Page 316: ......
Page 317: ......
Page 318: ......
Page 319: ......
Page 320: ......
Page 321: ......
Page 322: ......
Page 323: ......
Page 324: ......
Page 325: ......
Page 326: ......
Page 327: ......
Page 328: ......
Page 329: ......
Page 335: ......
Page 336: ......
Page 337: ......
Page 340: ......
Page 346: ......
Page 347: ......