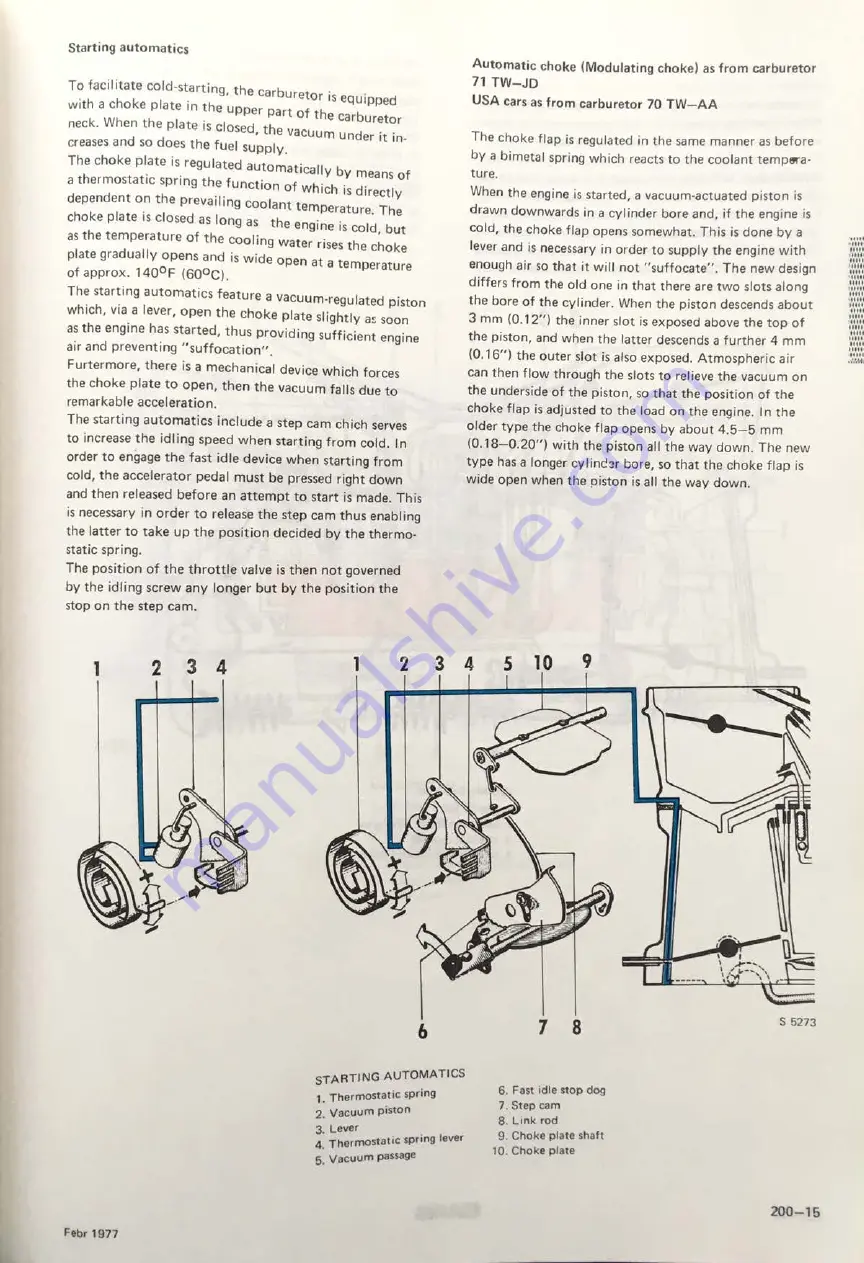
Starting automatics
plate gradually opens and is wide ope
of approx.
140°F
(60°C).
The starting automatics feature a vacuum-regulated piston
which, via a lever, open the choke plate slightly as soon
as
the
engine
has
started,
thus
providin
air and
preventing
"suffocation".
Furtermore, there is a mechanical device which forces
the choke plate to open, then the vacuum falls due to
remarkable acceleration.
The starting automatics include a step cam chich serves
to
increase
the
idling
speed
when
starting
from
cold.
In
order to engage the fast idle device when starting from
cold, the accelerator pedal must be pressed right down
and then released before an attempt to start is made. This
is necessary
in order to
release the step cam thus enabling
the latter to take up the position decided by the thermo-
static spring.
The position of the throttle valve is then not governed
by the idling screw any longer but by the position the
stop on the step cam.
n
at
a
temperature
9
sufficient engine
Automatic choke (Modulating choke) as from carburetor
71
TW—JD
USA cars as from carburetor 70 TW—AA
The choke flap is regulated in the same manner as before
by a bimetal spring which reacts to the coolant tempera-
ture.
When the engine is started, a vacuum-actuated piston is
drawn downwards in a cylinder bore and, if the engine is
cold, the choke flap opens somewhat. This is done by a
lever and is necessary in order to supply the engine with
enough air so that it will not "suffocate". The new design
differs from the old one in that there are two slots along
the bore of the cylinder. When the piston descends about
3 mm
(0.12”) the inner slot is exposed above the top of
the piston, and when the latter descends a further 4 mm
(0.16") the outer slot is also exposed. Atmospheric air
can
then
flow
through
the
slots
to
relieve
the
vacuum
on
the underside of the piston, so that the position of the
choke flap is adjusted to the load on the engine.
In the
older type the choke flap opens by about 4.5—5 mm
(0.18—0.20”) with the piston all the way down. The new
type has a longer cylinder bore, so that the choke flap is
wide open when the piston is all the way down.
STARTING
AUTOMATICS
1.
Thermostatic spring
2.
Vacuum piston
3.
Lever
.
4. Thermostatic spring
lever
5. Vacuum 9855593
6.
Fast
idle nap dog
7. Step cam
8.
Link
rod
9. Choke plate shaft
10. Choke plate
200-15
Summary of Contents for 95 1967
Page 1: ......
Page 2: ......
Page 3: ......
Page 4: ......
Page 5: ......
Page 7: ......
Page 43: ......
Page 44: ......
Page 45: ......
Page 46: ......
Page 47: ......
Page 48: ......
Page 49: ......
Page 51: ......
Page 52: ......
Page 53: ......
Page 54: ......
Page 55: ......
Page 56: ......
Page 57: ......
Page 58: ......
Page 59: ......
Page 60: ......
Page 61: ......
Page 62: ......
Page 63: ......
Page 64: ......
Page 65: ......
Page 66: ......
Page 67: ......
Page 68: ......
Page 69: ......
Page 70: ......
Page 71: ......
Page 72: ......
Page 73: ......
Page 74: ......
Page 75: ......
Page 76: ......
Page 77: ......
Page 78: ......
Page 79: ......
Page 80: ......
Page 81: ......
Page 82: ......
Page 83: ......
Page 140: ......
Page 164: ......
Page 206: ......
Page 210: ......
Page 262: ......
Page 266: ......
Page 281: ...WIRING DIAGRAM SAAB 95 R H D MODEL 1967 371 3 March 1979...
Page 283: ...WIRING DIAGRAM SAAB 95 L H D MODEL 1967 371 5 March 1979...
Page 287: ...38 L 1 E l s 67 WIRING DIAGRAM SAAB 96 R H D MODEL 19 371 9 March 1979...
Page 291: ...March 1979 S WIRING DIAGRAM SAAB 96 USA MODEL 1967 371 13...
Page 293: ...DEL 1967 RING DIAGRAM MONTE CARLO R H D MO WI 371 15 March 1979...
Page 295: ...ODEL 1967 CARLO L H D M RAM MONTE WIRING DIAG 371 1 7 March 1979...
Page 297: ...March 1979 Ili EEE late 67 ING DIAGRAM MONTE CARLO USA MODEL 19 WlR S 1392 371 19...
Page 299: ...March 1979 m BE EFTIII l i 18C 68 WIRING DIAGRAM SAAB 95 R H D MODEL 19 371 21...
Page 305: ...o 7 371 27 March 1979...
Page 307: ...March 1979 uni I176 EWEEEEE 68 WIRING DIAGRAM SAAB 96 L H D MODEL 19 371 29...
Page 311: ...March 1979 sessil WIRING DIAGRAM MONTE CARLO L H D MODEL 1968 371 3...
Page 313: ...l iiiiiii WIRING DIAGRAM DE LUXE USA MODEL 1963 371 35 March 1979...
Page 317: ...iriii iill 0 MODEL 1969 WIRING DIAGRAM SAAB 95 L H 371 39 March 1979 an...
Page 325: ...March 1979 3 5 Qt es 3 a 5 E rt 5 z _ a E 0 K i ll 15 tilts ts ii a me e m a 371 47...
Page 327: ...30 Willi 5 1969 WIRING DIAGRAM DE LUXE USA MODEL 371 49 March 1979...
Page 337: ...March 1979 MODEL 1970 DIAGRAM SAAB 96 L H D WIRING m iijiiii W _ 371 59...
Page 339: ...I rmi l llil e e March 1979 371 61...
Page 341: ...gmagaa aaei Jiii D MODEL 1971 WIRING DIAGRAM SAAB 95 R H 371 6 March 1979 m...
Page 343: ...March 1979 liIilli mm ii iiiiiiiiiiigija EEIEEEEE 3 __l I o jiiiii Iii em S 371 65...
Page 345: ...Map d nan mmmi E5 g I I III T31 4 j a n 4 me 5 j 55 35 9 v 3 371 67...
Page 349: ...33 m 71 WIRING DIAGRAM SAAB SEDAN L H D MODEL 19 371 71 March 1979...
Page 351: ...March 1979 4 In Etna mil reiterate lam l WIRING DIAGRAM SAAB 96 USA MODEL 1971...
Page 353: ...ea in 3 or IE __ 1 an WIRING DIAGRAM SAAB 96 R H D MODEL 1972 1974 March 1979 371 75...
Page 355: ...15 6 2 0 a 5 mm mm 72 1973 RING DIAGRAM SAAB 96 L H D MODEL 19 WI March 1979 371 77...
Page 357: ...Ell um am iL 1 EL I L RING DIAGRAM SAAB 96 USA MODEL 1972 1973 WI March 1979 371 79...
Page 359: ...lawman Iii y m a 371 81 MarCh 1979...
Page 361: ...in 2 U 7 WIRING DIAGRAM SAAB 96 R H D MODEL 19 5 371 83 March 1979...
Page 365: ...mu m as gg m I WIRING DIAGRAM SAAB 96 R H D MODEL 1976 371 87 March 1979...
Page 367: ...WIRING DIAGRAM SAAB 96 L H D MODEL 1976 371 89 March 1979...
Page 369: ...WIRING DIAGRAM SAAB 96 L H D MODEL 1977 371 91 March 1979...
Page 371: ...S 5769 1 911 V E m JH WIRING DIAGRAM SAAB 96 L H D MODEL 1977 8 March 1979 371 93...
Page 373: ...WIRING DIAGRAM SAAB 96 L H D MODELS 1978 AND 1979 371 95 March 1979...
Page 376: ...TRANSMISSION 400 2 SAAB Enh 1 11...
Page 388: ......
Page 392: ......
Page 414: ......
Page 424: ......
Page 431: ......
Page 442: ......
Page 478: ...M4 5 WM 55F _L5I COME 5 1m BIZ rm 5IsI 5 5I lI1I OIZI 5I5I M5I 75 5I3I 42 F3 5I RADIAL T m...
Page 486: ......
Page 506: ......
Page 542: ......
Page 551: ...nil 13...
Page 610: ......