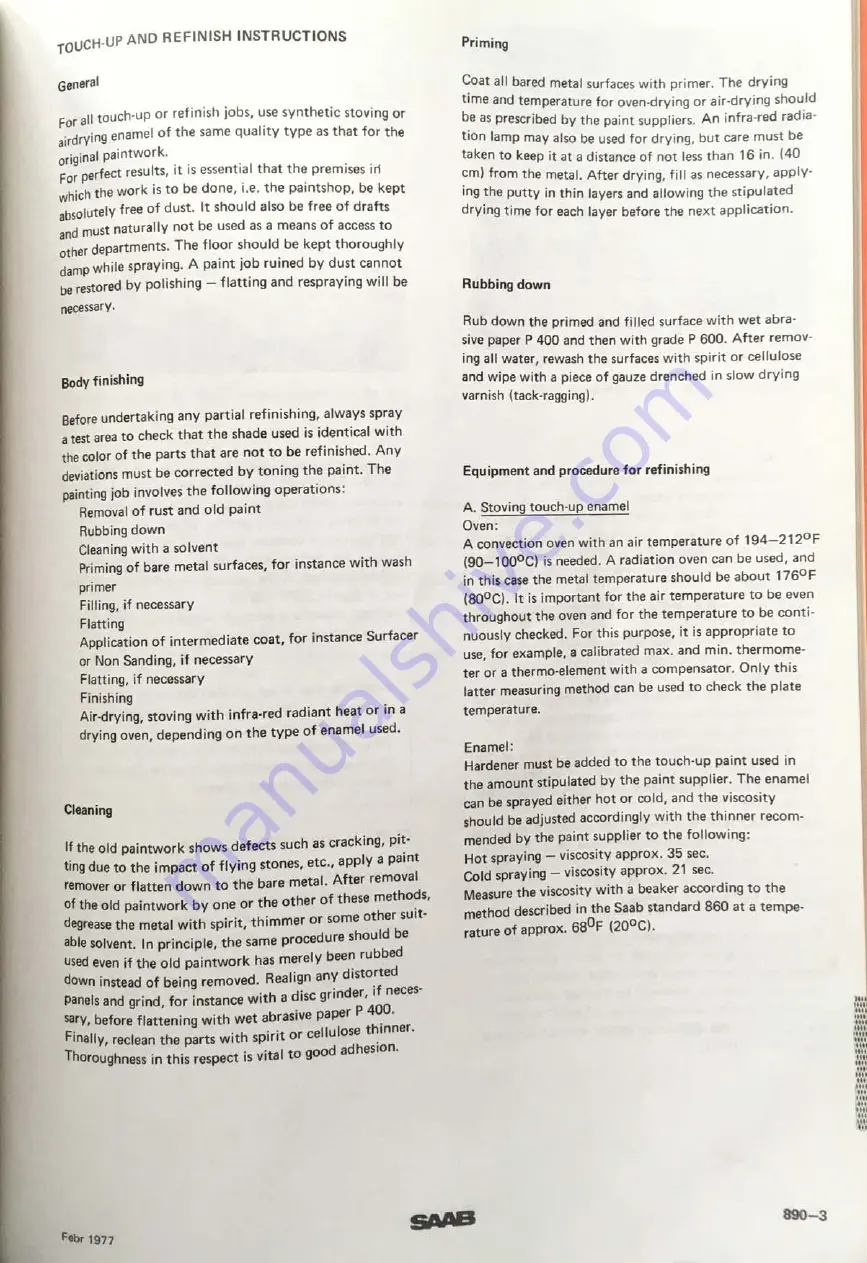
TOUCH'UF Ann; In.-
Il‘v-
General
For all touch-up or refinish jobs, use synthetic stoving or
airdryjng enamel of the same quality type as that for the
original paintwork.
For perfect results, it is essential that the premises in
which the work is to be done, Le. the paintshop, be kept
absolutely free of dust. It should also be free of drafts
and must naturally not be used as a means of access to
other departments. The floor should be kept thoroughly
damp while spraying. A paint job ruined by dust cannot
be restored by polishing —— flatting and
respraying will
be
necessal'Y-
Body finishing
Before undertaking any partial refinishing, always spray
a
test
area
to
check
that
the
shade
used
is
identical
with
the color of the parts that are not to be refinished.
Any
deviations must be corrected by toning the paint. The
painting job involves the following operations:
Removal of rust and old paint
Rubbing down
Cleaning with a solvent
Priming of bare metal surfaces, for instance with wash
primer
Filling, if necessary
Flatting
Application of intermediate coat, for instance Surfacer
or
Non
Sanding,
if
necessary
Flatting, if necessary
Finishing
Air-drying, stoving with infra-red radiant heat or in a
drying oven, depending on the type of enamel used.
Cleaning
If the old paintwork shows defects such as cracking, pit-
ting due to the impact of flying stones, etc., apply a Paint
remover or flatten down
to the
bare
metal.
After
removal
of the old paintwork by one or the other of these methods,
degrease the metal with spirit, thimmer or some other suit-
able solvent.
In principle, the same procedure should be
“Sed even if the old paintwork has merely been rubbed
°°Wh instead of being removed. Realign any distorted
Banals and grind, for instance with a disc grinder, ‘f neces-
sary, before flattening with wet abrasive paper P 490-
Finally, reclean the parts with spirit or cellulose thinner.
Th°'°U9hness in this respect is vital to 900d adhesnon.
Priming
Coat all bared metal surfaces with primer. The drying
time and temperature for oven-drying or air-drying should
he as prescribed by the paint suppliers. An infra—red radia-
no"
lamp may also
be
used
for drying,
but care
must
be
taken to keep it at a distance of not less than 16 in.
(40
om) from the metal. After drying, fill as necessary, apply-
"‘9 the Way in thin layers and allowing the stipulated
drYihQ time for each layer before the next application.
Rubbing down
Rub down the primed and filled surface with wet abra-
sive paper P 400 and then with grade P 600. After remov-
ing all water, rewash the surfaces with spirit or cellulose
and wipe with a piece of gauze drenched
in slow drying
varnish (tack-ragging).
Equipment and procedure for refinishing
A. Stoving touch-up enamel
Oven:
A convection oven with an air temperature of 194—2120F
(90—100°C) is needed. A radiation oven can be used, and
in this case the metal temperature should be about 176°F
(80°C). It is important for the air temperature to be even
throughout the oven and for the temperature to be conti-
nuously checked. For this purpose, it is appropriate to
use, for example, a calibrated
max. and
min. thermome-
ter or a thermo-element with
a
compensator.
Only this
latter measuring method can be used to check the plate
temperature.
Enamel:
Hardener must be added to the touch-up paint used in
the amount stipulated by the paint supplier. The enamel
can
be
sprayed
either
hot
or
cold,
and
the
viscosity
should be adjusted accordingly with the thinner recom-
mended by the paint supplier to the following:
Hot spraying — viscosity approx. 35 sec.
Cold spraying —- viscosity approx. 21
sec.
Measure the viscosity with a beaker according to the
method described in the Saab standard 860 at a tempe-
rature of approx.
68°F
(20°C).
aso—a
Summary of Contents for 95 1967
Page 1: ......
Page 2: ......
Page 3: ......
Page 4: ......
Page 5: ......
Page 7: ......
Page 43: ......
Page 44: ......
Page 45: ......
Page 46: ......
Page 47: ......
Page 48: ......
Page 49: ......
Page 51: ......
Page 52: ......
Page 53: ......
Page 54: ......
Page 55: ......
Page 56: ......
Page 57: ......
Page 58: ......
Page 59: ......
Page 60: ......
Page 61: ......
Page 62: ......
Page 63: ......
Page 64: ......
Page 65: ......
Page 66: ......
Page 67: ......
Page 68: ......
Page 69: ......
Page 70: ......
Page 71: ......
Page 72: ......
Page 73: ......
Page 74: ......
Page 75: ......
Page 76: ......
Page 77: ......
Page 78: ......
Page 79: ......
Page 80: ......
Page 81: ......
Page 82: ......
Page 83: ......
Page 140: ......
Page 164: ......
Page 206: ......
Page 210: ......
Page 262: ......
Page 266: ......
Page 281: ...WIRING DIAGRAM SAAB 95 R H D MODEL 1967 371 3 March 1979...
Page 283: ...WIRING DIAGRAM SAAB 95 L H D MODEL 1967 371 5 March 1979...
Page 287: ...38 L 1 E l s 67 WIRING DIAGRAM SAAB 96 R H D MODEL 19 371 9 March 1979...
Page 291: ...March 1979 S WIRING DIAGRAM SAAB 96 USA MODEL 1967 371 13...
Page 293: ...DEL 1967 RING DIAGRAM MONTE CARLO R H D MO WI 371 15 March 1979...
Page 295: ...ODEL 1967 CARLO L H D M RAM MONTE WIRING DIAG 371 1 7 March 1979...
Page 297: ...March 1979 Ili EEE late 67 ING DIAGRAM MONTE CARLO USA MODEL 19 WlR S 1392 371 19...
Page 299: ...March 1979 m BE EFTIII l i 18C 68 WIRING DIAGRAM SAAB 95 R H D MODEL 19 371 21...
Page 305: ...o 7 371 27 March 1979...
Page 307: ...March 1979 uni I176 EWEEEEE 68 WIRING DIAGRAM SAAB 96 L H D MODEL 19 371 29...
Page 311: ...March 1979 sessil WIRING DIAGRAM MONTE CARLO L H D MODEL 1968 371 3...
Page 313: ...l iiiiiii WIRING DIAGRAM DE LUXE USA MODEL 1963 371 35 March 1979...
Page 317: ...iriii iill 0 MODEL 1969 WIRING DIAGRAM SAAB 95 L H 371 39 March 1979 an...
Page 325: ...March 1979 3 5 Qt es 3 a 5 E rt 5 z _ a E 0 K i ll 15 tilts ts ii a me e m a 371 47...
Page 327: ...30 Willi 5 1969 WIRING DIAGRAM DE LUXE USA MODEL 371 49 March 1979...
Page 337: ...March 1979 MODEL 1970 DIAGRAM SAAB 96 L H D WIRING m iijiiii W _ 371 59...
Page 339: ...I rmi l llil e e March 1979 371 61...
Page 341: ...gmagaa aaei Jiii D MODEL 1971 WIRING DIAGRAM SAAB 95 R H 371 6 March 1979 m...
Page 343: ...March 1979 liIilli mm ii iiiiiiiiiiigija EEIEEEEE 3 __l I o jiiiii Iii em S 371 65...
Page 345: ...Map d nan mmmi E5 g I I III T31 4 j a n 4 me 5 j 55 35 9 v 3 371 67...
Page 349: ...33 m 71 WIRING DIAGRAM SAAB SEDAN L H D MODEL 19 371 71 March 1979...
Page 351: ...March 1979 4 In Etna mil reiterate lam l WIRING DIAGRAM SAAB 96 USA MODEL 1971...
Page 353: ...ea in 3 or IE __ 1 an WIRING DIAGRAM SAAB 96 R H D MODEL 1972 1974 March 1979 371 75...
Page 355: ...15 6 2 0 a 5 mm mm 72 1973 RING DIAGRAM SAAB 96 L H D MODEL 19 WI March 1979 371 77...
Page 357: ...Ell um am iL 1 EL I L RING DIAGRAM SAAB 96 USA MODEL 1972 1973 WI March 1979 371 79...
Page 359: ...lawman Iii y m a 371 81 MarCh 1979...
Page 361: ...in 2 U 7 WIRING DIAGRAM SAAB 96 R H D MODEL 19 5 371 83 March 1979...
Page 365: ...mu m as gg m I WIRING DIAGRAM SAAB 96 R H D MODEL 1976 371 87 March 1979...
Page 367: ...WIRING DIAGRAM SAAB 96 L H D MODEL 1976 371 89 March 1979...
Page 369: ...WIRING DIAGRAM SAAB 96 L H D MODEL 1977 371 91 March 1979...
Page 371: ...S 5769 1 911 V E m JH WIRING DIAGRAM SAAB 96 L H D MODEL 1977 8 March 1979 371 93...
Page 373: ...WIRING DIAGRAM SAAB 96 L H D MODELS 1978 AND 1979 371 95 March 1979...
Page 376: ...TRANSMISSION 400 2 SAAB Enh 1 11...
Page 388: ......
Page 392: ......
Page 414: ......
Page 424: ......
Page 431: ......
Page 442: ......
Page 478: ...M4 5 WM 55F _L5I COME 5 1m BIZ rm 5IsI 5 5I lI1I OIZI 5I5I M5I 75 5I3I 42 F3 5I RADIAL T m...
Page 486: ......
Page 506: ......
Page 542: ......
Page 551: ...nil 13...
Page 610: ......