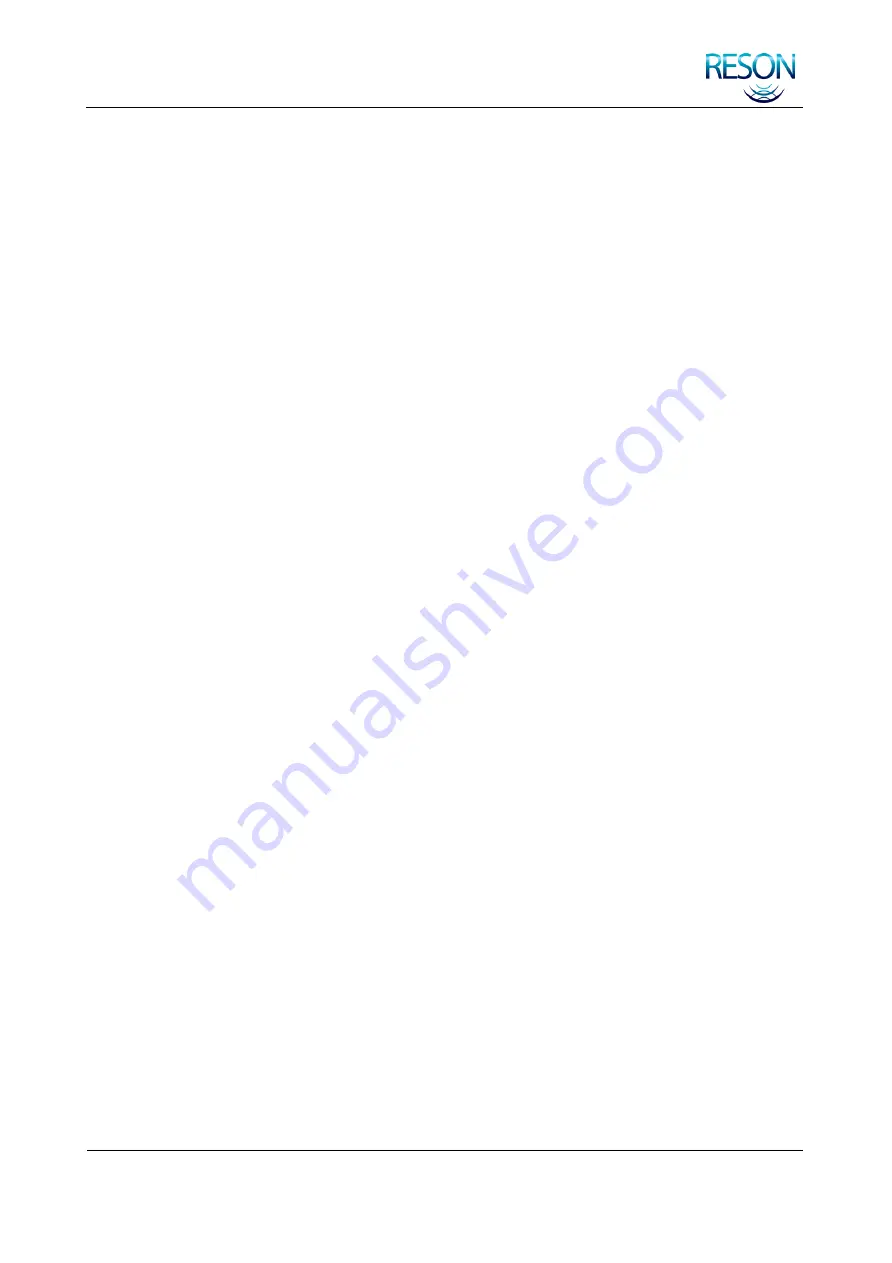
ACTIVE SONAR USAGE
SeaBat 7125 SV2 Operator‟s Manual
Page 113
July 25, 2011
Version 3
6.7 Limitations
Physical limitations in the functionality of the system have to be taken into consideration
when operating the SeaBat system. Some of the limitations are absolutes; others can to
some degree be overcome.
The following subsections provide examples of different kinds of limitations.
6.7.1 Cavitation
Some reduction in the transmitted source level is expected to be caused by cavitation.
For means of compensating for this, see subsections in
6.7.1.1 Propeller Cavitation
Propeller cavitation can be a significant concern for two reasons. First, the frequency of
propeller cavitation noise is in the operating frequency band of most sonar equipment.
Second, the source levels of the propellers installed are expected to be high unless
special quieting techniques have been implemented.
Propeller energy typically propagates to the forward area sonar systems via a direct or
hull-grazing path. The other arrival path of propeller energy is by the bottom bounce
path. This path will be more significant in shallow water depths (less than 500 meters).
The potential impact can be further quantified for particular bottom depths of proposed
operational test sites.
6.7.1.2 Appendage Cavitation
Appendage cavitation can result from rough or unfaired edges on the hull and can even
be present at lower speeds. If the source is located near the sonar installation area, it
can be a significant noise deficiency. It is difficult to predict the occurrence of appendage
cavitation without under-hull drawings, pictures, or visual inspection of the ship when in
dry-dock.
6.7.2 Machinery Noise
Machinery noise should not be a major factor for sonars that operate at frequencies
above 5kHz. Mechanical machinery noise is usually prevalent at 2kHz and below,
though it is occasionally detected at higher frequencies when fluid flow through pipes or
cavitating pumps are involved.
Typically, the most important consideration for machinery noise is the proximity of the
acoustic sensor to the machinery source. There has been one observed case where
diesel engine piston frequency harmonics have been the controlling noise source at
12kHz, but in this situation, the engine room and the sonar compartment shared a
common bulkhead. Normally, acoustic devices are sufficiently distanced from major
machinery noise sources that machinery noise does not interfere.
A concern remains that there may be some auxiliary machinery (or other unusual
equipment) located near the sonar that could produce noise interference. An inspection
of the installation site and ship drawings to verify the position and proximity of all
Summary of Contents for SeaBat 7125 SV2
Page 2: ...This page intentionally left blank...
Page 211: ......