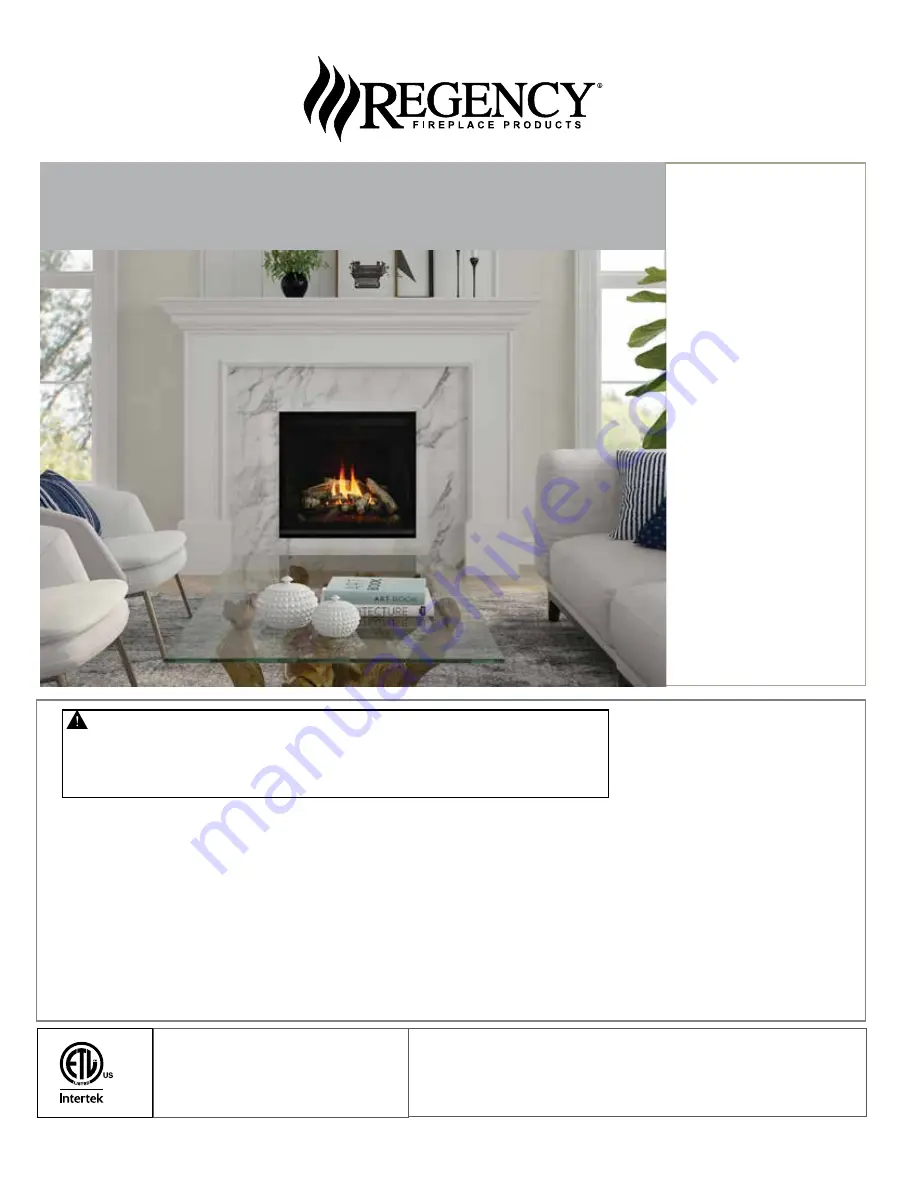
920-268b
FPI FIREPLACE PRODUCTS INTERNATIONAL LTD. 6988 Venture St., Delta, BC Canada, V4G 1H4
10.06.21
Grandview
®
G600C
Gas Fireplace
Owners &
Installation Manual
www.regency-fire.com
MODEL: G600C
Medium DV Gas Fireplace
Do not store or use gasoline or other flammable vapors and liquids in the vicinity of this or any other appliance.
WHAT TO DO IF YOU SMELL GAS
•
Do not try to light any appliance.
• Do not touch any electrical switch: do not use any phone in your building.
Leave the building immediately.
• Immediately call your gas supplier from a neighbour's phone. Follow the gas supplier's instructions.
• If you cannot reach your gas supplier, call the fire department.
Installation and service must be performed by a qualified installer, service agency or the gas supplier.
Installer:
Please complete the details on the back cover and leave
this manual with the homeowner.
Homeowner
:
Please keep these instructions for future reference.
Certified to/Certifié pour: ANSI Z21.88-2019
Tested by:
Warning
Fire or Explosion Hazard
Failure to follow safety warnings exactly could result in serious
injury, death, or property damage.
Summary of Contents for Grandview G600C
Page 100: ...100 Grandview G600C Gas Fireplace warranty ...
Page 101: ... Grandview G600C Gas Fireplace 101 notes ...
Page 102: ...102 Grandview G600C Gas Fireplace notes ...
Page 103: ......