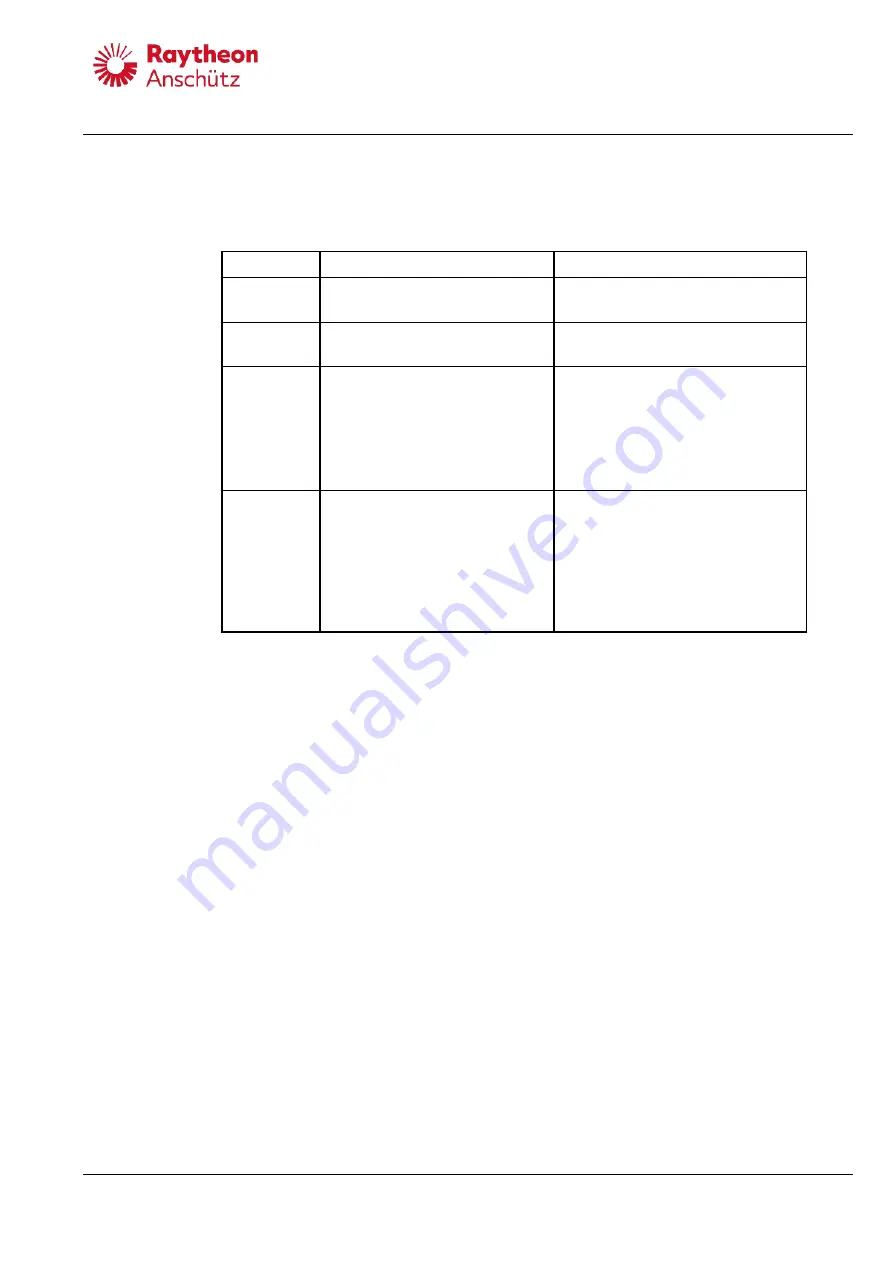
NautoPilot® 5000 Series
102-890.NG001-NG003
Operator Manual
Edition: 003
137
10000001052
the value changes until the joystick is brought back to its initial position.
Table 41
Joystick operation
Direction
One movement
Held in
Forwards
(Rad +)
The turning radius increases
0.1 NM
Changes of the values until re-
leased.
Backwards
(Rad- )
The turning radius reduces
0.1 NM
Changes the course or heading
to be steered until released.
Left
(Port)
Changes the course or heading
to be steered
1
to port.
Note: If a course with a
decimal value (e.g. 315.7
)
is still set, this value is
rounded off the first
movement.
Changes the course or heading to
be steered
until released.
Right
(Stbd)
Changes the course or
heading to be steered 1
to
starboard.
Note: If a course with decimal
value (e.g. 315.3
) is still set,
this value is rounded up with
the first movement.
Changes the course or heading to
be steered
until released.
The settings are displayed in the section AUTOPILOT VALUES.