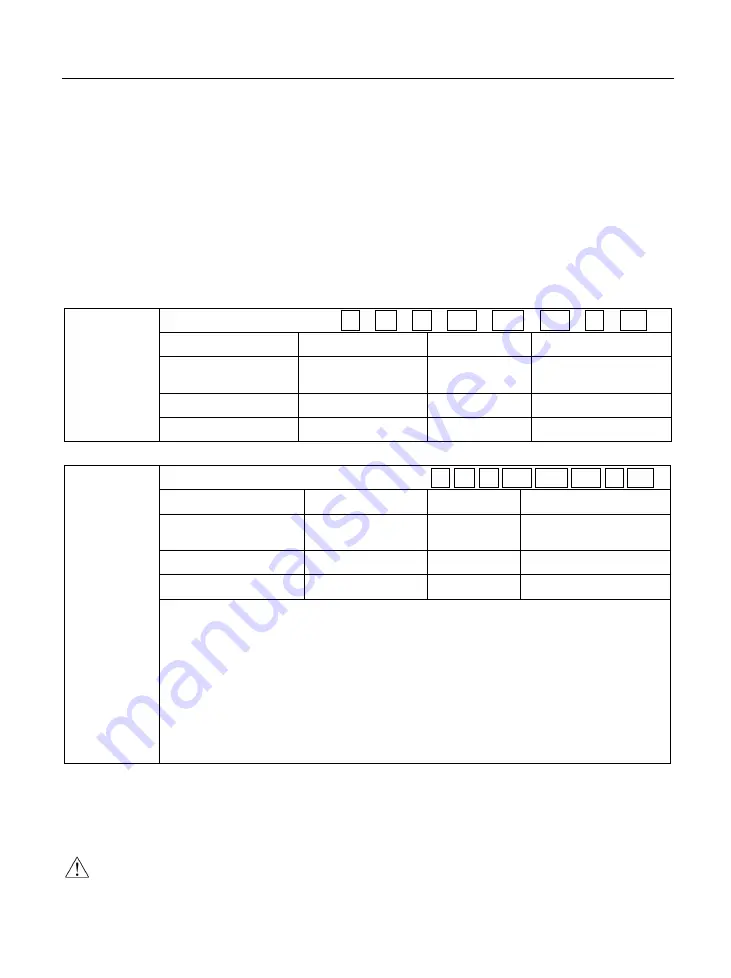
FL20-C Series
108
After a servo motor is changed, if user does not know encoder electric angle and whether motor
phase sequence is correct, user can make the servo motor operate normally by using electric
angle indication function. Before electric angle indication, please make sure the following steps:
(1)
Motor actual power.
(2)
Ensure that the servomotor encoder cable is connected properly.
(3)
Ensure that the servomotor is connected to zero.
(4)
Ensure that the servo is in the OFF status.
When 2008h-1 Ah=3, please input motor actual power to servo drive, then identify parameters.
2006h-0Ch
Motor rated power PP PV PT CSP CSV CST PP HM
Setting range
Setting unit
Mfr’s value
When enabled
1
~
30000
0.01KW
—
Effective
Immediately
Function code
Mapping
Data type
Assessibilty
Ho011
N
UINT16
RW
2008h-1Ah
Motor parameter identification setting PP PV PT CSP CSV CST PP HM
Setting range
Setting unit
Mfr’s value
When enabled
0
~
4
N/A
0
Effective
Immediately
Function code
Mapping
Data type
Assessibilty
So-25
N
UINT16
RW
0: no motor parameter indentification
1: indentify motor resistor, inductance, pole pairs numbers and encoder
installation angle
2: lock motor shaft
3:indentify motor resistor, inductance and estimate motor EMF
4: indentify motor resistor, inductance, pole pairs numbers, motor EMF and
encoder installation angle
When 2008h-1Ah is set to 1, enter So-14 jogging control mode. System starts automatic testing ,
panel displays flashing “TEST”. After indentification is finished, panel will return to So-14
interface, and electrical angle is saved in 2006h-13h. If line sequence error occurs, panel
displays AL-05, please stop the motor and adjust the line sequence before next operation.
: When line sequence error occurs, reverse two phases, and then repeat the electrical angle
identification.