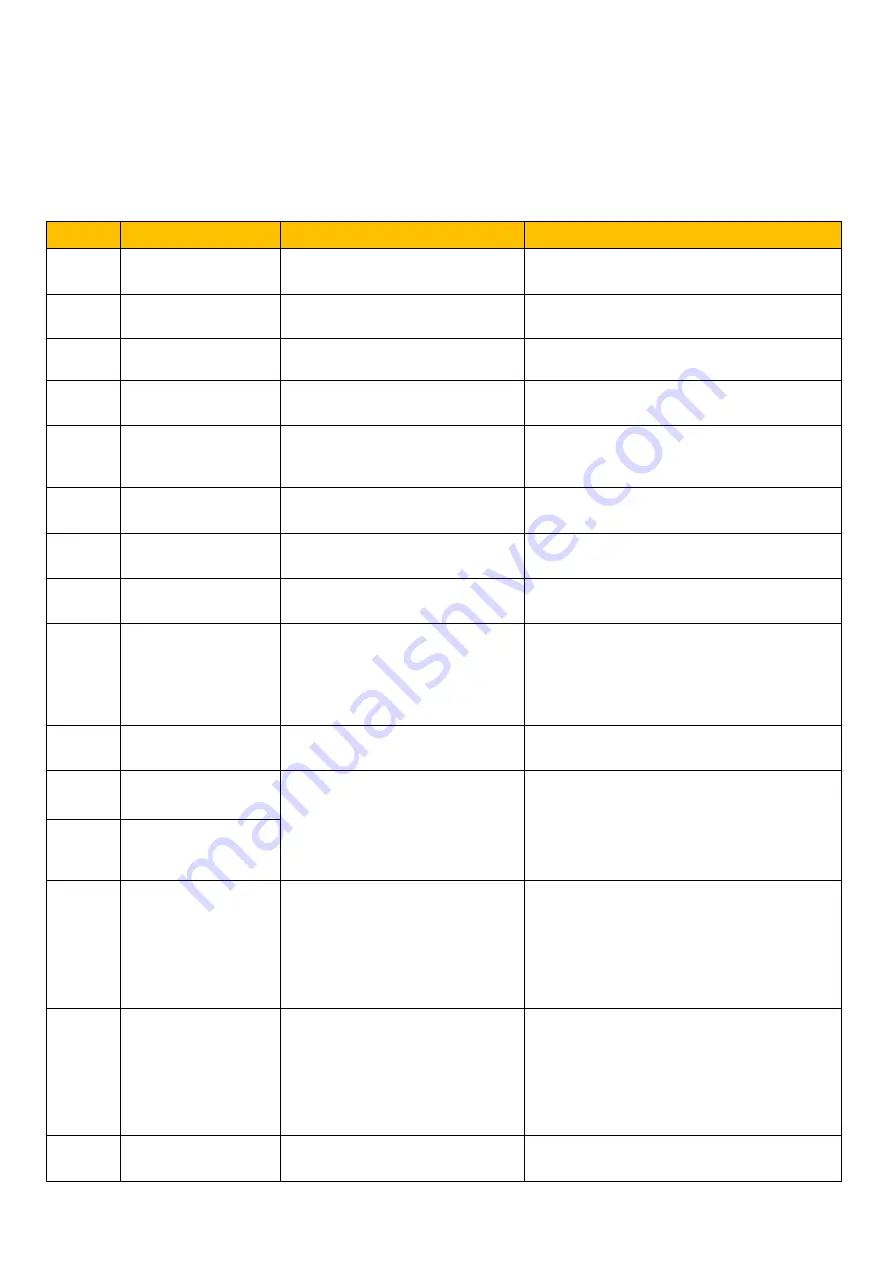
Troubleshooting
10-1
AC10 Inverter
Chapter 10
Troubleshooting
When the inverter is tripped check what the cause is and rectify as required.
Take counter measures by referring to this manual in case of any malfunctions on inverter. Should it still
be unsolved, contact the manufacturer. Never attempt any repairs without due authorization.
Table 10-1
In
verter’s Common Cases of Malfunctions
Fault
Description
Causes
Possible Solution
AErr
Line Disconnected
Analog signal line disconnected
Signal source is broken
Change the signal line
Change the signal source
CE
Communication
Timeout
Communication fault
PC/PLC does not send command at fixed time
Check communication line for reliable connected
Err1
Password is Wrong
When password function is
enabled, password is set wrong
Set password correctly
Err2
Tuning Parameters
Wrong
incorrect motor parameters
entered
Connect motor correctly
Enter correct motor data
Err3
Current Malfunction
Before Running
Current alarm signal exists
before running
Check if control board is properly
connected to power board
Contact Parker
Err4
Current Zero
Excursion Malfunction
Flat cable is loosened
Current detector is broken
Check the flat cable
Contact Parker
Err5
PID Parameters are
set Wrong
PID parameters are set wrong.
Set the parameters correctly
FL
Flycatching Fault
Flycatching failure
Track again
Contact manufacturer
GP
Ground fault
Motor cable is broken and short-
circuit to earth
The insulation of motor is broken
and short circuit to earth
Inverter has fault
Change motor cable
Repair or replace motor
SEE ALSO: OC, OC2 and ERR4
L.U.
Under-Voltage
Protection
Low voltage on the input side
Check if supply voltage is normal
Check if parameter setting is correct
OC/OC2
(Note)
Overcurrent
Too short acceleration time
Short circuit at output side
Locked rotor with motor
Parameter tuning is not correct
Prolong acceleration time
Ask if motor is cable broken
Check if motor overloads
Reduce VVVF compensation value
Measure parameter correctly
OC1
Overcurrent 1
O.E.
DC Over-Voltage
Supply voltage too high
Load inertia too big
Deceleration time too short
Motor inertia rise again
Parameter of speed loop PID is
set abnormally
Check if rated voltage is input
Add braking resistance(optional)
Increase deceleration time
Set the parameter of rotary speed loop PID
correctly
O.H.
Heatsink
Overheat
Environment temperature too
high
Poor ventilation
Fan damaged
Carrier wave frequency or
compensation curve is too high
Improve ventilation
Clean air inlet and outlet and radiator
Install as required
Change fan
Decrease carrier wave frequency or
compensation curve
O.L1
Inverter Overload
Load too heavy
Reduce load; *check drive ratio
Increase inverter’s capacity
Summary of Contents for 10G-46-0600-BF
Page 2: ......
Page 18: ...Installation 3 3 AC10 Inverter 3 3 Inverters Installed in a Control Cabinet...
Page 26: ...Installation Connection 7 2 AC10 Inverter Metal Cover Layout Frames 6 11...
Page 112: ...The Default Applications 13 2 AC10 Inverter 13 1Application 1 Basic Speed Control F228 1...
Page 114: ...The Default Applications 13 4 AC10 Inverter 13 2 Application 2 Auto Manual Control F228 2...
Page 116: ...The Default Applications 13 6 AC10 Inverter 13 3 Application 3 Preset Speeds F228 3...
Page 118: ...The Default Applications 13 8 AC10 Inverter 13 4 Application 4 Raise Lower Secondary F228 4...
Page 120: ...The Default Applications 13 10 AC10 Inverter 13 5Application 5 PID F228 5...