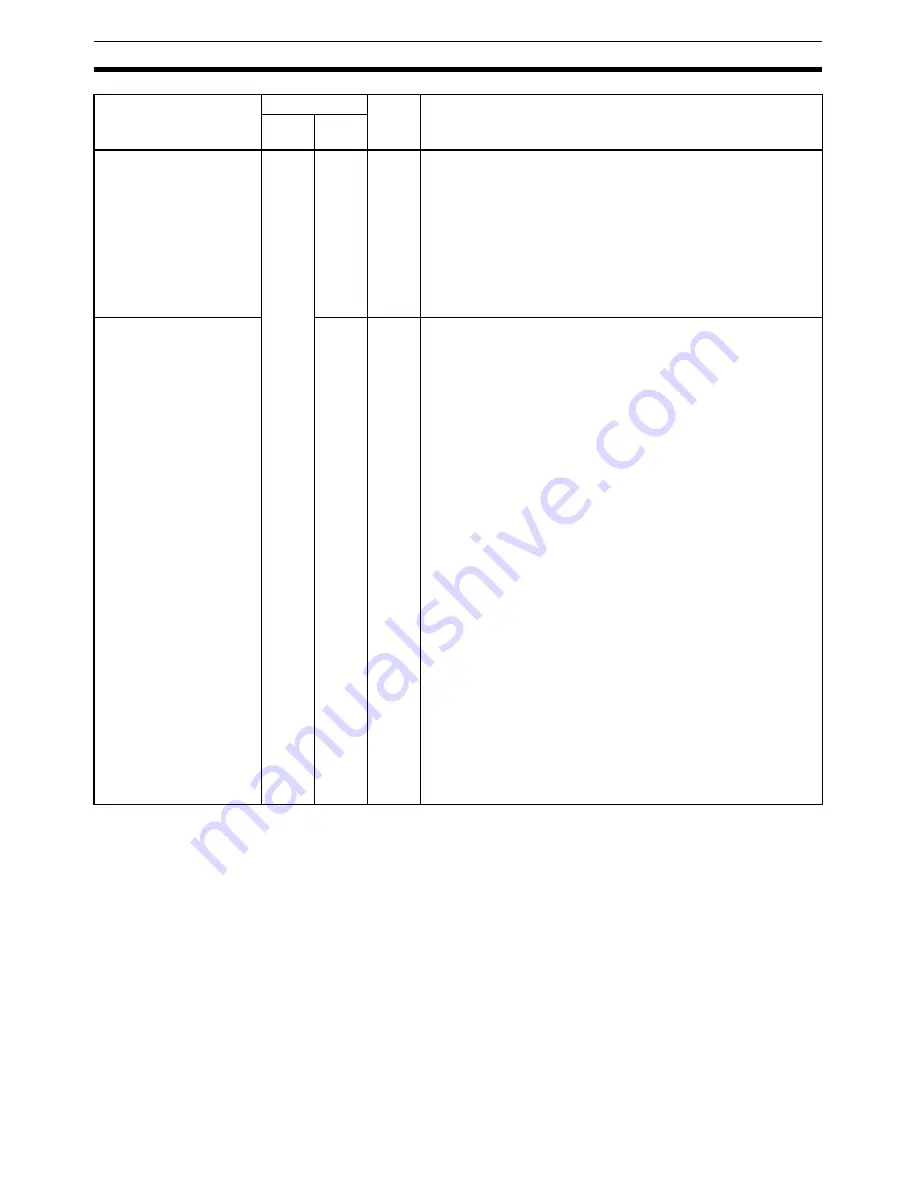
110
Error Codes
Section 15-2
Command timeout
037Ah
-
0399h
300Ch
300Ch
A MECHATROLINK command could not be completed within a
fixed period of time (10 seconds). The followings are the possible
causes:
• Disconnection, breakage of MECHATROLINK cable
Check the MECHATROLINK cable.
• Communications error caused by noise
Remove the cause of the noise.
When this error persists even after providing these remedies, the
Driver (NS115) or MC Unit may be broken. Replace the broken
one with a new unit.
Absolute encoder error
300Dh
300Dh
Data from the ABS encoder could not be processed normally.
• Initial multi-turn value exceeds the multi-turn limit.
Set the same value in the driver parameter [Pn205: Multi-turn
limit setting] and the motor parameter [900C: Multi-turn limit].
After the setting is completed, restore the power, reset the alarm,
and perform the origin setting.
• After origin setting, the following values related to B/A were
changed.
Note
B = No. of encoder pulses
×
P5AA05
A = P5AA04
×
P5AA06
B/A is integer calculation and the result is to be reduced.
After the change was made (saving to F-ROM), restore the
power, reset the alarm, and perform origin setting.
• The multi-turn limit value in the driver parameter or the motor
parameter was changed after origin setting.
After the change was made (saving to F-ROM), restore the
power, reset the alarm, and perform origin setting. (When the
multi-turn value of the driver parameter was changed, make sure
to perform “Absolute encoder multi-turn amount setting change”
on the driver.)
• Servo driver is set as an incremental encoder. Set the driver
parameter Pn002 digit No. 2 to “0” (used as an absolute encoder)
and restore the power.
• Disconnection, breakage of encoder cable
Check the encoder cable.
• Communications error caused by noise
Remove the cause of the noise.
When this error persists even after providing these remedies, the
encoder or MC Unit may be broken. Replace the broken one with
a new unit.
Name
Error log
Alarm
code
Cause and remedy
Error
code
Detail
code
Summary of Contents for CX-MOTION - 06-2008
Page 1: ...CX Motion MCH Cat No W448 E1 04 OPERATION MANUAL...
Page 2: ...CXONE AL C V3 CXONE AL D V3 CX Motion MCH Operation Manual Revised June 2008...
Page 3: ...iv...
Page 5: ...vi...
Page 9: ...x TABLE OF CONTENTS...
Page 15: ...xvi Note All new functions can be used in Motion Control Units with unit version 3 0 or later...
Page 31: ...12 Connecting to a PLC Section 2 2...
Page 47: ...28 Operations Listed by Purpose Section 3 2...
Page 71: ...52 Exporting File Section 6 4...
Page 91: ...72 Debugging the Program Section 9 3...
Page 95: ...76 Data Traces Section 10 1...
Page 99: ...80 Verifying Backup File with MC Unit Section 11 3...
Page 109: ...90 Printing Section 13 1...
Page 133: ...114 Error Codes Section 15 2...