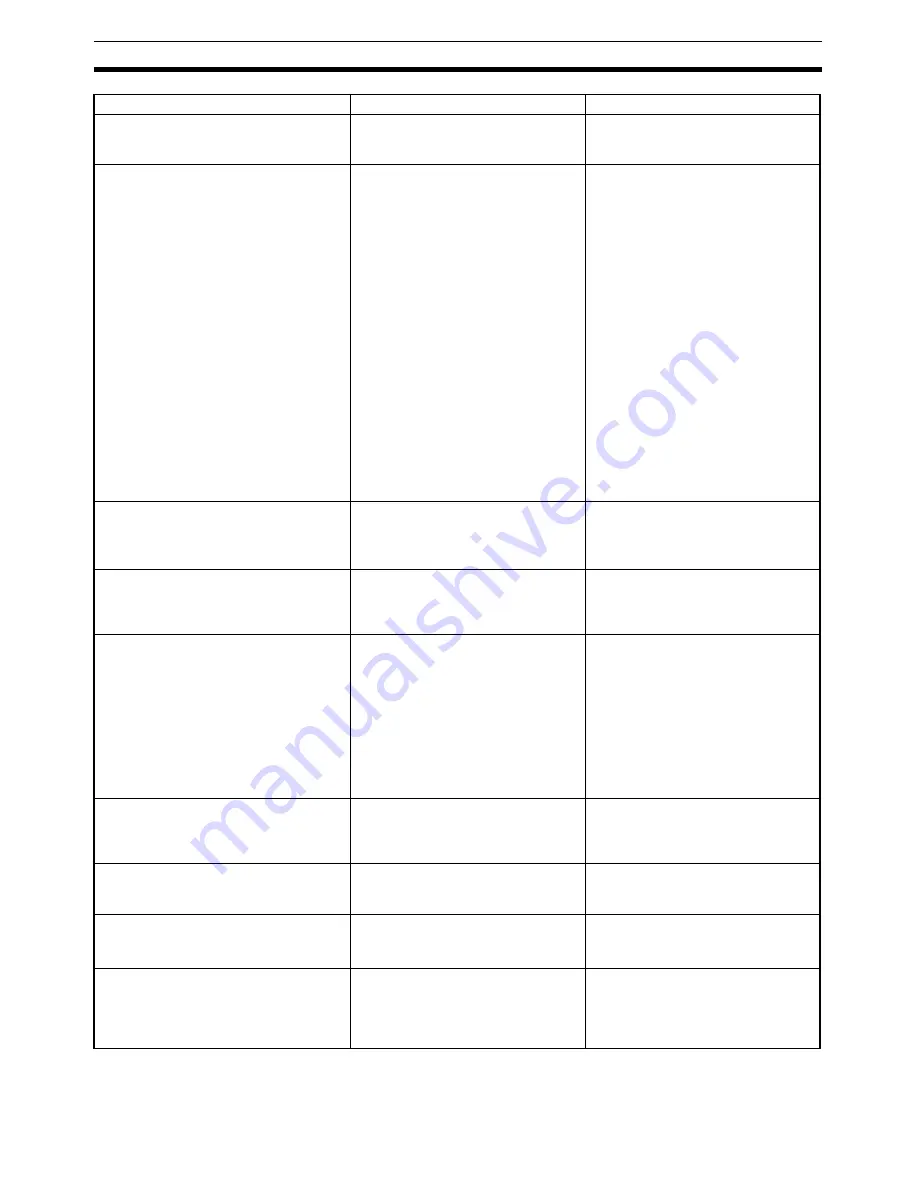
96
Troubleshooting
Section 15-1
514: No unit with the specified unit num-
ber address
User tried to transfer the data to an
MC Unit that is not connected to the
PLC.
Check the hardware unit number and
correct it accordingly.
515, 8196, 8452: The specified data not
available in MC Unit
Program Read:
• The specified program does not
exist.
• An error has occurred in the pro-
gram memory.
CAM Read:
• The specified CAM table does not
exist.
• An error has occurred in the CAM
data memory.
Servo Parameter Read:
• The specified data has not been
written.
Clear Program:
• The specified program does not
exist.
Clear CAM:
• The specified CAM data does not
exist.
Make sure the data exist in MC Unit
8456: Cannot write the parameter
• The content of parameter data is
incorrect.
• An attempt was made to transfer a
parameter value that was too large.
Check the parameter values before
transfer.
10001: No Servo information found in MC
Unit, cannot perform transfer from MC
Unit
An attempt was made to transfer the
servo parameters but there is no
servo information in the MC Unit.
Configure the MC Unit with the proper
servo parameter and motor parame-
ter information before doing the trans-
fer operation.
1: Servo Transfer - Servo parameter has
been transferred successfully to MC Unit.
However servo parameters could not be
transferred to Servo drive. Please check
the servo drive connection.
1: Save Servo Parameter - Servo param-
eters saved in MC Unit. However failed to
save in Servo drive
This error occurs when:
• Servo drive is not connected
• Mismatch of axis numbers in project
and the servo drives connected to
MC Unit.
• Series or models in the project and
servo drive are different.
1. Check whether servo drive is con-
nected.
2. Check whether the axis numbers in
servo drives and the project are
same and correct them if they are
different.
3. Check whether the servo drive
series or models are the same as
in servo drives and correct them if
they are different.
513: Remote network has not been
started (destination node not part of the
network). Communication with slave not
possible, or not allocated as servo axis
An attempt was made to read the data
from a servo drive but servo drive is
not connected to MC Unit.
Connect the proper servo drive and
configure the drive with proper infor-
mation, then try to read the data.
10002: Motor Parameter not set in hard-
ware, Hence fail to read
Servo parameters and motor parame-
ter are not set in the servo and thus
cannot be read.
Write the parameters before reading
them.
10000: MC Model you have selected
does not match with unit connected.
An attempt was made to read or write
data to or from an MC Unit from a dif-
ferent MC series.
1. Use the same PLC and MC series
as those connected to computer.
2. Check the unit number.
66: A communication monitor time error
occurred.
Communications with the PLC were
disconnected for more than a certain
period of time while the CX-Motion-
MCH was in monitor mode.
Switch other Support Software,
including the CX-Programmer, to
offline status or increase the baud
rate, and then switch the CX-Motion-
MCH back to monitor mode.
Message
Probable cause
Remedy
Summary of Contents for CX-MOTION - 06-2008
Page 1: ...CX Motion MCH Cat No W448 E1 04 OPERATION MANUAL...
Page 2: ...CXONE AL C V3 CXONE AL D V3 CX Motion MCH Operation Manual Revised June 2008...
Page 3: ...iv...
Page 5: ...vi...
Page 9: ...x TABLE OF CONTENTS...
Page 15: ...xvi Note All new functions can be used in Motion Control Units with unit version 3 0 or later...
Page 31: ...12 Connecting to a PLC Section 2 2...
Page 47: ...28 Operations Listed by Purpose Section 3 2...
Page 71: ...52 Exporting File Section 6 4...
Page 91: ...72 Debugging the Program Section 9 3...
Page 95: ...76 Data Traces Section 10 1...
Page 99: ...80 Verifying Backup File with MC Unit Section 11 3...
Page 109: ...90 Printing Section 13 1...
Page 133: ...114 Error Codes Section 15 2...