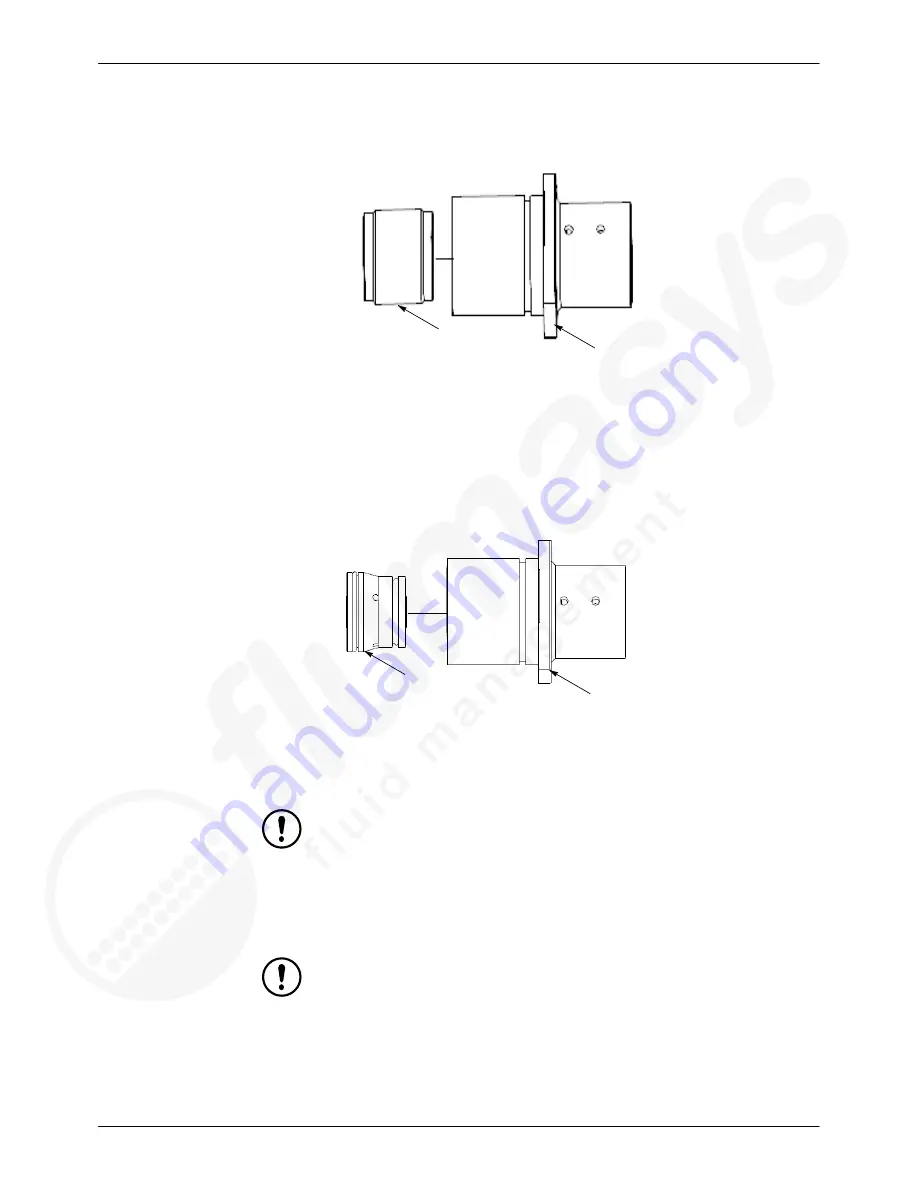
Disassembly and Assembly
11-9
Part 7440274
2017 Nordson Corporation
16. Remove bearing (2) from metering cylinder body (1).
1
2
Figure 11-70 Bearing Removal From Metering Cylinder Body
17. Remove lantern ring (2) from metering cylinder body (1).
NOTE:
Utilize seal removal tool, or equivalent, to remove lantern ring from
metering cylinder body.
1
2
Figure 11-71 Lantern Ring Removal From Metering Cylinder Body
18. Utilize a plastic pick with a blunt tip, or equivalent tool, to remove O
−
ring
(1) from lantern ring (4). See Figure 11-72.
CAUTION:
Do not use sharp or pointed tools to remove O
−
ring.
Do not reuse O
−
ring.
19. Utilize a plastic pick with a blunt tip, or equivalent tool, to remove cap (2)
from lantern ring (4). See Figure 11-72.
CAUTION:
Do not use sharp or pointed tools to remove cap.
Do not reuse cap.