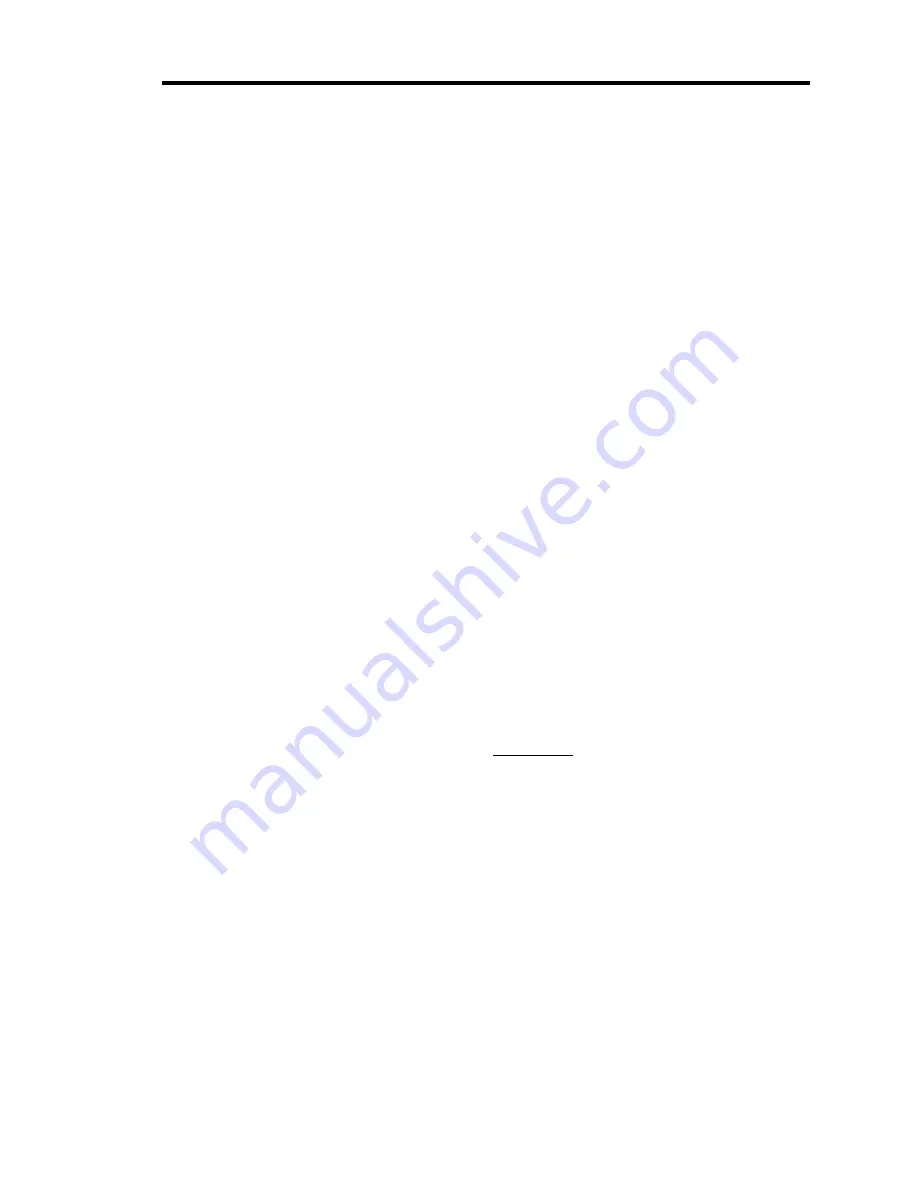
Chapter Three: Overview
System Design Elements
91
The 146 instrument utilizes Proportional-Integral-Derivative (PID) control found in most
industrial controllers today. The P-I-D parameters operate according to an equation. These
parameters are:
1. Proportional control action (Gain) is used as a constant to create a valve drive signal that
is proportional to the error signal, (the error signal is the result of comparing actual
pressure with the set point). The error signal is then multiplied by a gain setting, thus
creating a proportional valve drive signal. The higher the gain, the greater the change in
the valve drive signal. Thus, the response is proportional to the gain.
Provided that the gain is not set too high, adjusting it allows the system to approach set
point more quickly than if a lower gain setting is used. The best tuned gain is
maximized without promoting overshoot.
Valve Drive Signal = K
1
x Error Signal
(K1 is adjusted by changing the gain setting)
2. Integral control action creates a valve drive signal that is proportional to the magnitude
and sign of the area under the error signal curve (error signal with respect to time).
Valve Drive Signal = K
2
x
∫
(Error Signal)dt
As time passes the valve position is changed. Due to integration (and good control), the
error signal approaches and is reduced to zero. An increase in the integral value
increases the period of time over which the error signal is generated, and system response
gets slower. This helps offset potential oscillation caused by a high gain setting.
3. Derivative control action (Phase Lead) creates a valve drive signal that is proportional to
the rate of change of the sensor pressure reading. Derivative is the lead, or anticipation
factor.
Valve Drive Signal = K
3
x d(pressure)
dt
(K3 is adjusted by changing the lead setting)
Part of the lag in a control system is caused by the fact that the current pressure reading
is no longer accurate by the time it is used in the PID calculations. To overcome this, the
current reading is compared with a previous reading, and then the rate of change is
extrapolated to arrive at a new pressure reading. The new reading more accurately
represents the true pressure. The new pressure reading is substituted for the current
reading in PID calculations. Thus, the derivative control mode provides an anticipation
element. The valve drive signal then causes the control valve to approach its steady state
position sooner than it would if there was no derivative in the above equation.
Artisan Technology Group - Quality Instrumentation ... Guaranteed | (888) 88-SOURCE | www.artisantg.com