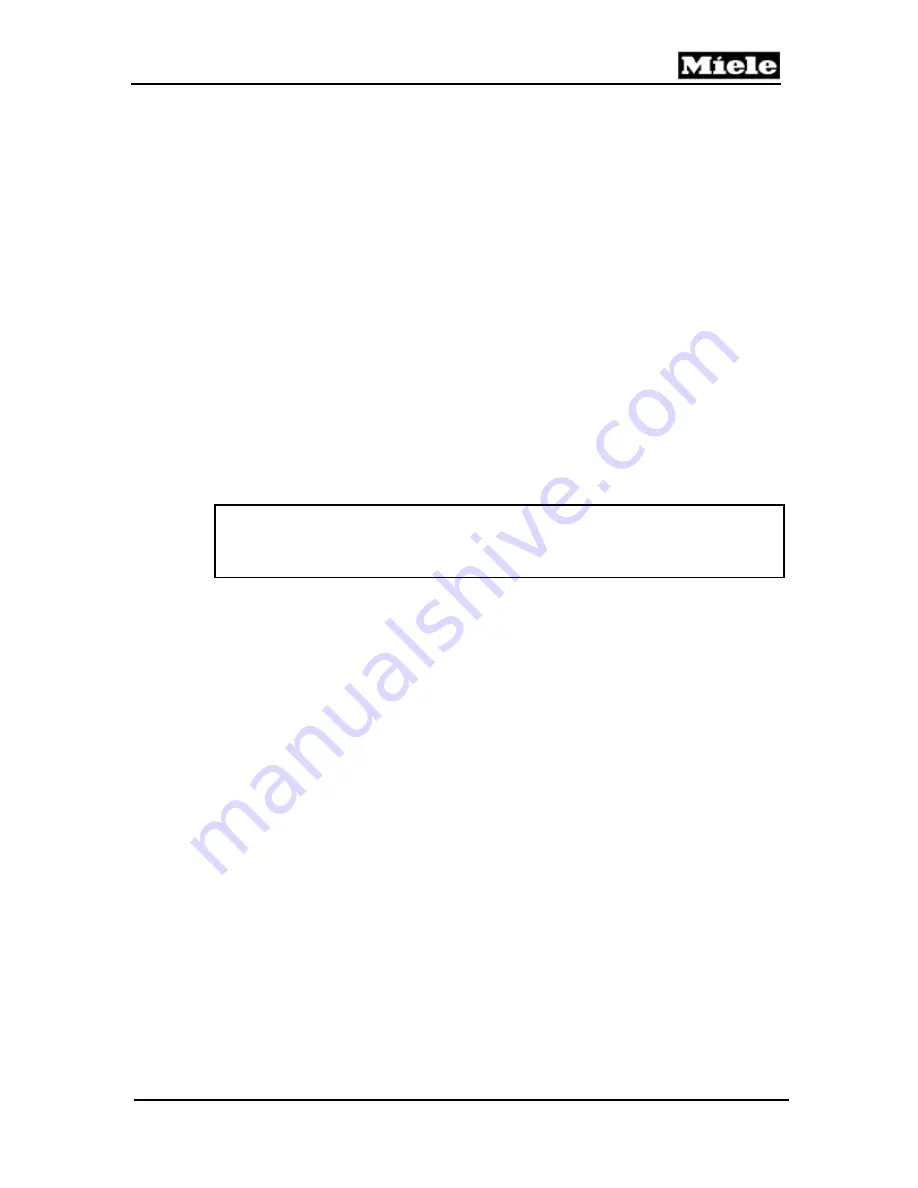
Technical Information
221
G 1xxx/G 2xxx
3 Fault
Repair
3.1
On/Off Button Jams
Symptom:
In machines with plastic panels, the On/Off button can get stuck.
Cause:
Cutout in panel for switch is too narrow.
Remedy:
Cutout was modified in machines 79249108 and later.
In older machines, use an appropriate tool to widen the cutout.
3.2
Display Steams Up
Symptom:
Inside of the display steams up during drying.
Cause:
Condensation conduit with open capillary barrier (mat. no. 5829110).
Remedy:
Replace the conduit.
Note:
Since August 2005, machines have been fitted with condensation conduits
featuring closed capillary barriers (mat. no. 6208972).
Summary of Contents for ADVANTA G 2170
Page 1: ...TECHNICAL INFORMATION G 1xxx and G 2xxx Dishwashers All US Models 2012 Miele USA ...
Page 43: ...Technical Information 43 G 1xxx G 2xxx 010 Casing ...
Page 47: ...Technical Information 47 G 1xxx G 2xxx Figure 010 5 Side Hinge Retaining Screw ...
Page 48: ...Technical Information 48 G 1xxx G 2xxx 020 Door ...
Page 64: ...Technical Information 64 G 1xxx G 2xxx 030 Front Panel ...
Page 68: ...Technical Information 68 G 1xxx G 2xxx 040 Inner Cabinet ...
Page 77: ...Technical Information 77 G 1xxx G 2xxx 050 Water Paths ...
Page 220: ...Technical Information 220 G 1xxx G 2xxx 100 Fascia Panel Touchtronic Navitronic Incognito ...
Page 226: ...Technical Information 226 G 1xxx G 2xxx 130 Cutlery Tray ...