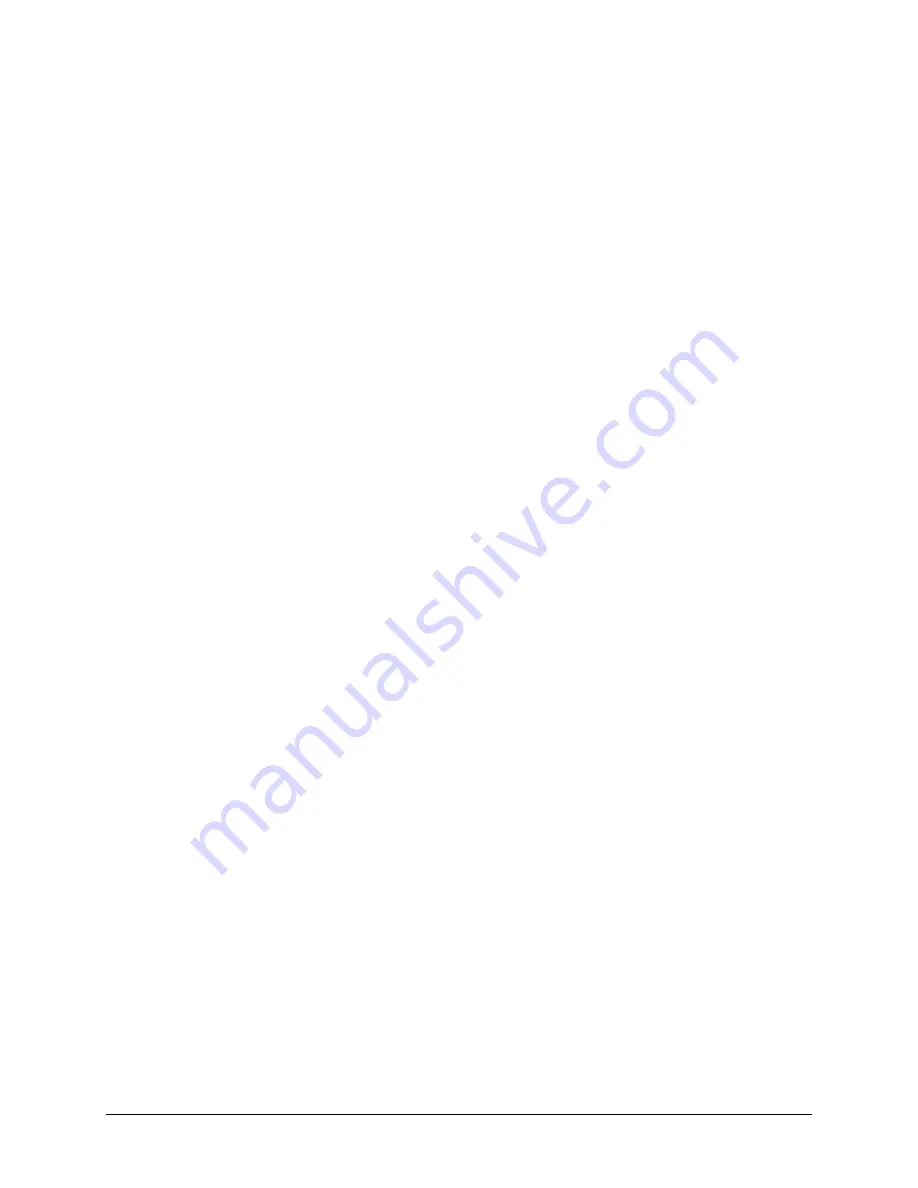
LumaSMART
®
User Manual
Installation of Probes and Accessories
•
30
3.2
Installation Philosophy
LumaSense has been a leader in the use of fiber optics to measure temperature in transformers for more than 25
years. During this time, LumaSense has continuously developed improved products and procedures to meet
customer needs. This section provides general guidelines to help determine where and how the measuring device
(FOT probes) should be installed.
3.2.1
General Guidelines for FOT Installation
FOT probes are usually installed in windings of transformers to detect winding hot spots. They may also be
installed for measurement of top-oil temperatures and core temperatures. These applications provide data for
evaluation of the transformer during temperature rise testing to ensure transformers meet the guaranteed values
and to determine what additional MVA capability is available in the transformer.
The measured temperatures during operation provide data to determine life consumption, loading by hot spot
temperature during dynamic load changes, transformer cooling control, over temperature alarms, and over
temperature tripping functions. There are special applications where probes may be installed in other areas, such
as oil duct temperature, bottom oil temperature, tie rod temperature or core temperature, but these applications
would be user specific and often are conducted as type tests for a first design of a transformer.
The following FOT probe installations represent the basic, general configurations. The sample specification
supplied by LumaSense states that probes must be installed in the hottest winding at the hot spot. This location
should be determined by the transformer design engineer who has the responsibility of ensuring that the
transformer meets specified temperature rise criteria, and should know the location of the hottest spot in the
windings. The hot spot is usually determined by use of finite element evaluation of leakage flux and current density
in the winding conductors represented at maximum loading of the transformer. Therefore, the designer can
provide the specific location of the hot spot under different load conditions and for differing tap positions.
For a core form transformer, the hot spot will typically be near the top of the winding that is closest to the core,
because the leakage flux at rated load will pass through the conductors as the flux concentrates to reenter the
core. This concentrated flux causes induced currents, increasing the heating. Shell form transformers will have a
different configuration and again the location of the probe will be determined by the design engineer.
It is recommended that the FOT location be discussed with the designer and agreed upon before manufacturing
begins. The designer should be able to predict the hot spot with a difference of no greater than 5 °C. It should be
expected that the measured hot spot when compared to the calculated hot spot will be lower than calculated
during the design.
Under no circumstances should the FOT hot spot be higher than calculated hot spot. If it is higher, this is a strong
indication that something is wrong with the transformer or a calculation error has occurred and requires the
manufacturer to provide detailed resolution which may include defective cooling ducts. The measured hotspot
should not be less than the calculated value on the average of 5°C below the value calculated during the
temperature rise test. If the measured hot spot is more than 10°C below the calculated value, the FOT may not
have been properly installed and there may be oil flow occurring around the installed FOT.
Typically, the FOT probes will be installed in disc type windings that are usually used in modern transformers sized
10 MVA and larger. Smaller sized transformers may have fiber optics installed if they are critical transformers or
specially designed transformers. A spacer will be replaced during block assembly, with a modified spacer that
contains the fiber optic probe. The tip of the probe should be placed such that the tip is adjacent to the hottest
spot. This will most likely be near the center of the disc winding.
The FOT tip placed into the spacer must be sealed so that no oil can circulate into the slot cut into the spacer or
along the parallel conductors of the disc windings. This may require that insulating paper be attached to both sides
of the spacer and sufficient fill be provided to seal any possible oil paths. The spacer and FOT tip area will be oil
impregnated during the transformer processing, so it is not necessary to leave any openings. The following
chapters of this manual show the proper way to ensure sealing.