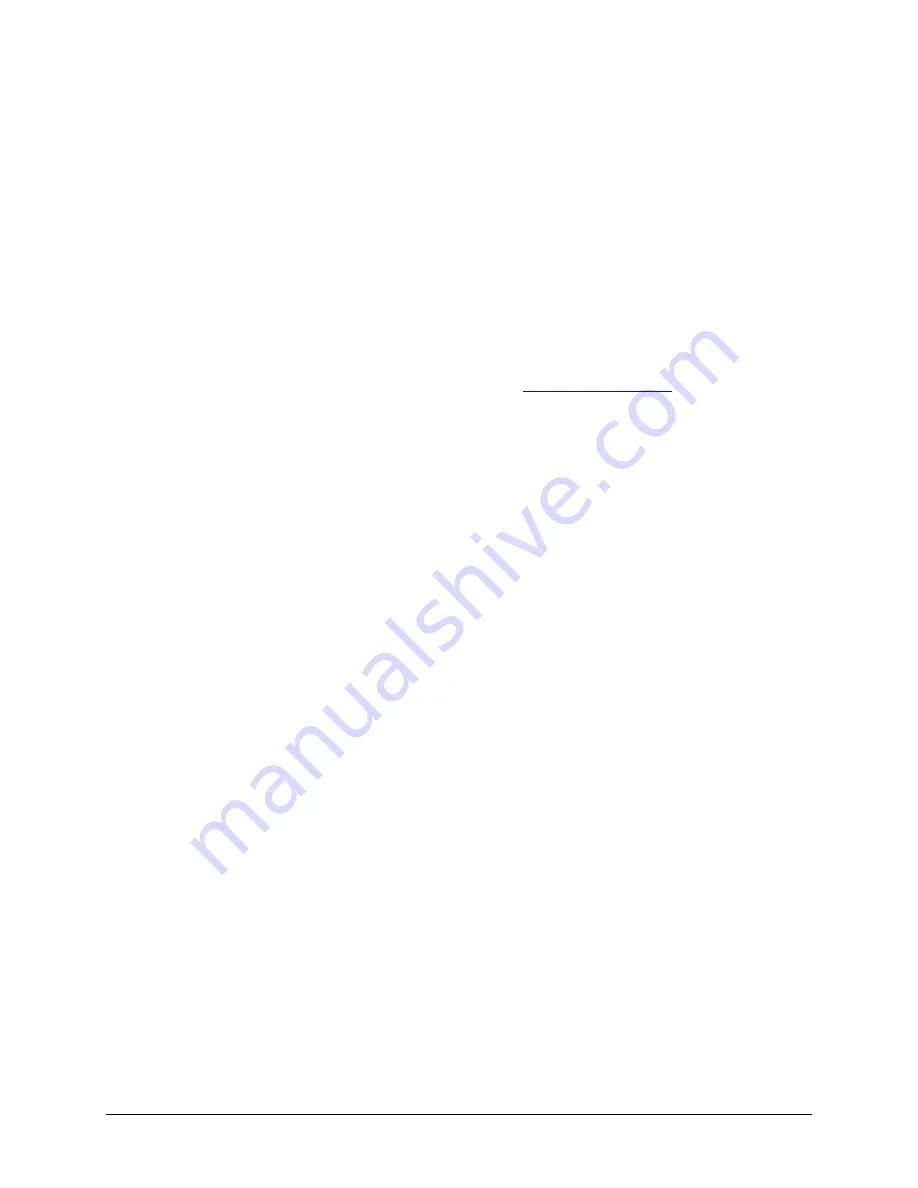
LumaSMART
®
User Manual
Introduction
•
27
After internal connections are made, external extension cables can be connected to the outside of the tank wall
penetrators and run to the LumaSMART controller. Standard lengths are available and special lengths are available
on request.
The hardware is designed to allow for simple and inexpensive sensor installation. Self-testing capabilities in the
LumaSMART controller can be used to check the probes and fiber optic cables during installation.
Service Life
LumaSense probes are designed to survive in hot transformer oil for the life of the transformer. The LumaSMART
controller electronics are designed to withstand the temperature, humidity, electromagnetically induced surges,
and coupled noise pulses encountered in this field. The LED measurement signal light source is designed to endure
for the life of the LumaSMART controller.
2.3.3
Diagnostic Instrument
LumaSense offers the Luxtron 812, which is a two-channel test monitor instrument that can be used for checking
probes during installation. Find more information on our website at
2.4
User Benefits
The LumaSMART controller has many user benefits:
•
Transformer design integrity and manufacturing quality verification
•
Transformer protection and life extension with real-time cooling control
•
Increased transformer loading to the safe maximum
•
External communication and monitoring connections
•
Extract additional MVA rating existing in every transformer design
2.4.1
Transformer Design Integrity and Manufacturing Quality Verification
Hot spot temperature rise at rated load is a necessary parameter for determining the loading capability of all
transformers. IEEE Standard C57.12.00 requires that the hot spot temperature rise above ambient does not exceed
80 °C. Further work was performed to correct this situation, in hopes that the hot spot rise could be determined
from oil temperature measurements and average winding rise by measurement of resistance during standard
commercial tests in accordance with IEEE C57.12.90 (that is, heat run).
However, test results reported by the IEEE and IEC indicate that the temperatures calculated using simulated
measurement methods deviate significantly from direct measurement using fiber optic probes taken from hot
spots on the winding. Only by directly measuring the hot spots using fiber optic technology can the temperature
rise truly be known. The LumaSMART controller provides this capability.
2.4.2
Transformer Protection and Life Extension with Real-Time Cooling Control
When transformer loading exceeds the nameplate rating, continuously or on a transient basis, increased winding
temperature causes insulation deterioration, thereby reducing transformer life. LumaSense fiber optic probes
directly measure winding temperature in real time. With the LumaSMART controller, temperature Alarm setpoints
are programmed to critical values. The LumaSMART controller relays activate when winding temperatures exceed
setpoint values. By connecting these relays to the transformer cooling equipment, the winding temperature can be
kept at a safe value.
Many transformers experience transient overloads lasting only a few hours. However, even for this short period of
time, insulation deterioration and resulting loss of transformer life occurs and accumulates with each repetition. A
major weakness of the traditional Winding Temperature Indicator (WTI), in addition to its poor accuracy, is its
response time of several hours. This is due to basing the simulated readings on top oil temperature measurement.
Therefore, a transient overload can occur and the WTI may never sense it. The instant response time of the
LumaSMART controller, on the other hand, immediately activates cooling.