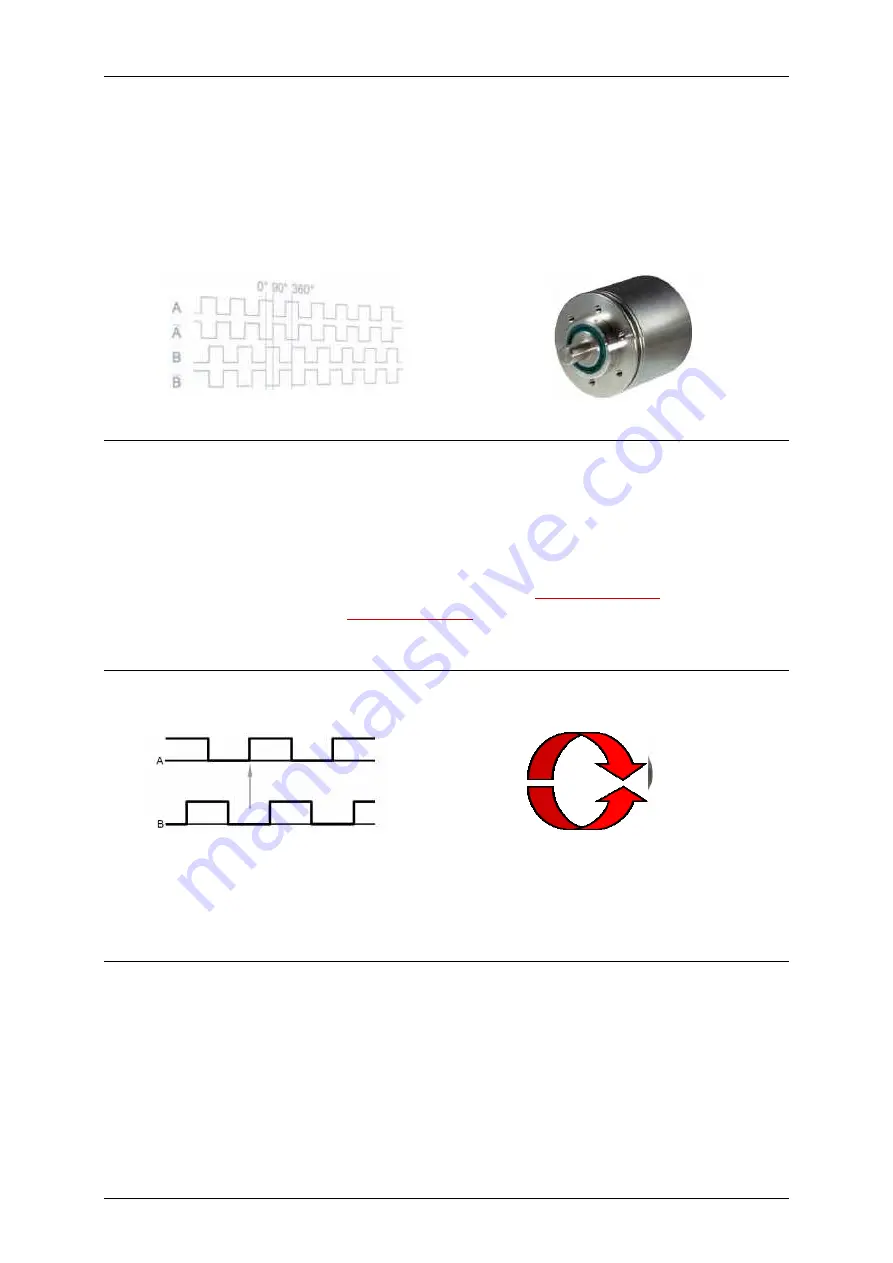
Group 12
Appendix - Encoder Guidelines
Page 383
JET3 Series
Release 2.02
12.3 Encod
er guidelines and “hot
-
plugging” of external devices
Encoders (also called incremental encoder) are used for the dynamic capture of angles of
shafts or to measure distances and speed information.
They are based on a technology which converts mechanical movements like rotation or
linear movement to electrical digital signals. In combination with measurement wheels or
gear racks, encoders can be also used to measure linear movements as e.g. distances.
Types of encoders:
Regarding the different internal technology of the encoders, they are distinguished into two
different principles:
Incremental
encoders:
supply simple “endless” square wave signals
Absolut encoder:
supply digital signals on several data output lines
(parallel signal output)
this encoder type
cannot be used!!!
Direction of rotation:
Typically encoders are supplying two output signals which are shifted 90°.
Just with this two shifted signals a so-
called „direction detection“ can be realized. Due to the
analysis of the phase position of signal „A“ and the phase position of signal “B” the electronic
can detect if the encoder turns forward or backwards.
Control of print width:
With the help of the encoder signals the printer gets information about the distance and the
speed of the current production and is therefore able to regulate an accurate print width of the
printout.
Just due the permanent and current measurement of the encoder, a steady print width can be
ensured even at varying speeds of the production line.
Summary of Contents for JET3
Page 1: ...Operating Manual V2 02 Please keep for future reference ...
Page 2: ......