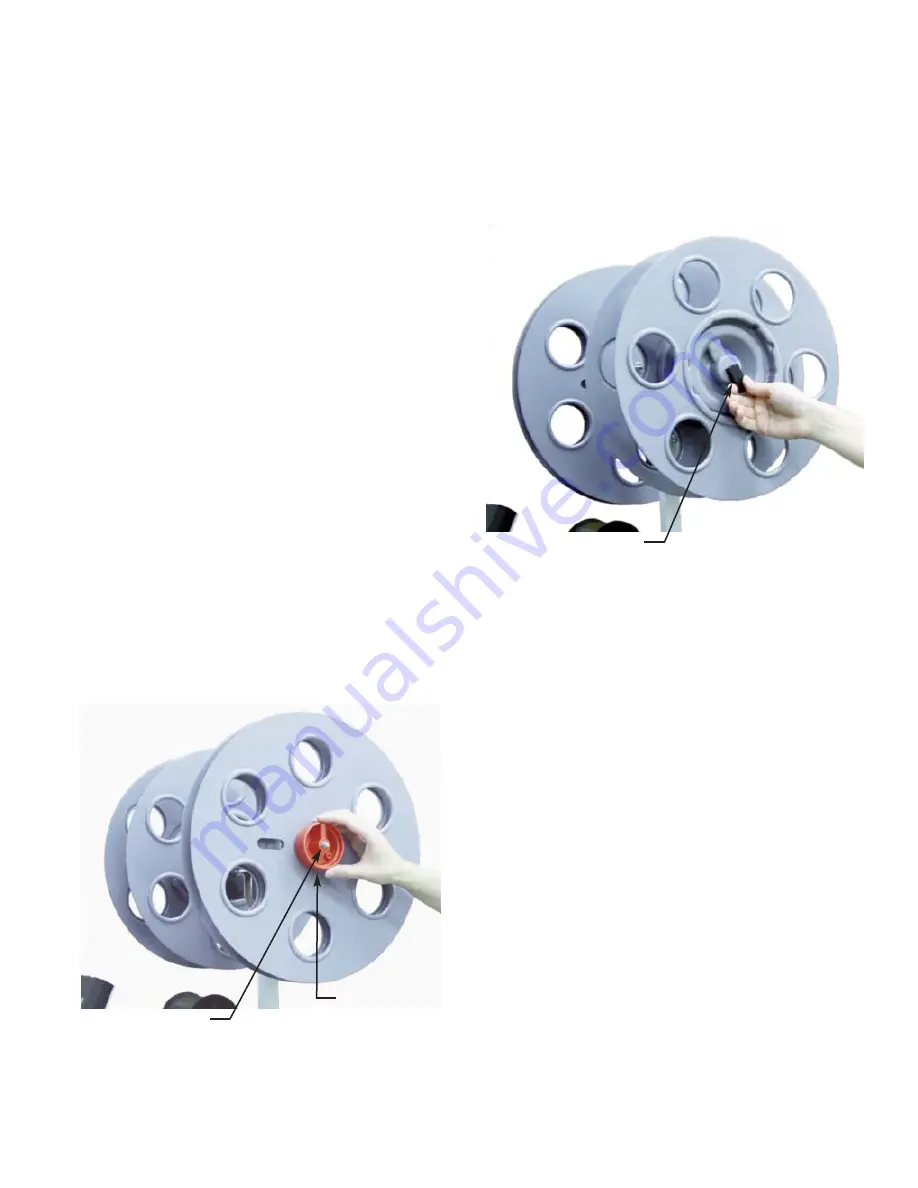
P 4.1
SECTION IV
Operation
A. LOADING CLOSURE ROLL:
Figure 4.1
The lok track shim must be installed in the lok track
when running closures without labels.
1.
Remove the reel front plate by grasping and
pulling the reel knob off the reel detent pin.
2.
Mount a roll of closures on the reel hub bearing.
The closures must always be mounted with the
closure opening facing the oncoming product.
When properly loaded, the closure opening is
facing toward the front reel plate.
3.
Replace the reel front plate.
B. LOADING A ROLL OF CLOSURE-LABELS:
Figure 4.2 - 4.3
A shim (Item 13 Page 8.14 Parts Identification) is
installed in the lok track and must be removed when
closing with closure-labels. Grasp the top of the
shim and pull up to remove it from the track. There
are two studs located on the closer mast, designed
893 09 12
to hang the lok track shim when it is not in use. The
shim must be installed in the lok track when running
closures without labels.
1.
Release the reel plate latch by pulling the hand
away from the reel plate and remove the label
cassette from the closer.
2.
Release the two reel plates latches and separate
the cassette.
3.
Discard the closure-label core. Press a new roll
of closure-labels onto the label cassette.
(Closure-labels must always be mounted with
the closure opening facing the front reel plate of
the label cassette.)
4.
Snap the label cassette together and engage the
latches.
5.
Re-install the cassette onto the closing machine,
pressing down on the latch to secure.
NOTE: Multiple reel cassettes can be used for faster
installation of closure-labels, or for storage of
partially used closure-label rolls.
Figure 4.1
Reel knob
Reel detent pin
Reel plate latch
Figure 4.2
Summary of Contents for 893A ULTRA
Page 10: ...This page intentionally blank ...
Page 16: ...This page intentionally blank ...
Page 26: ...This page intentionally blank ...
Page 56: ......
Page 60: ...This page intentionally blank ...
Page 80: ...ELECTRICAL COMPONENTS Figure 8 11 893 05 15 SECTION VIII Parts Identification P 8 20 ...
Page 82: ...COVERS AND GUARDS Figure 8 12 P 8 22 SECTION VIII Parts Identification 893 05 15 ...
Page 97: ...This page intentionally blank ...
Page 100: ...This page intentionally blank ...