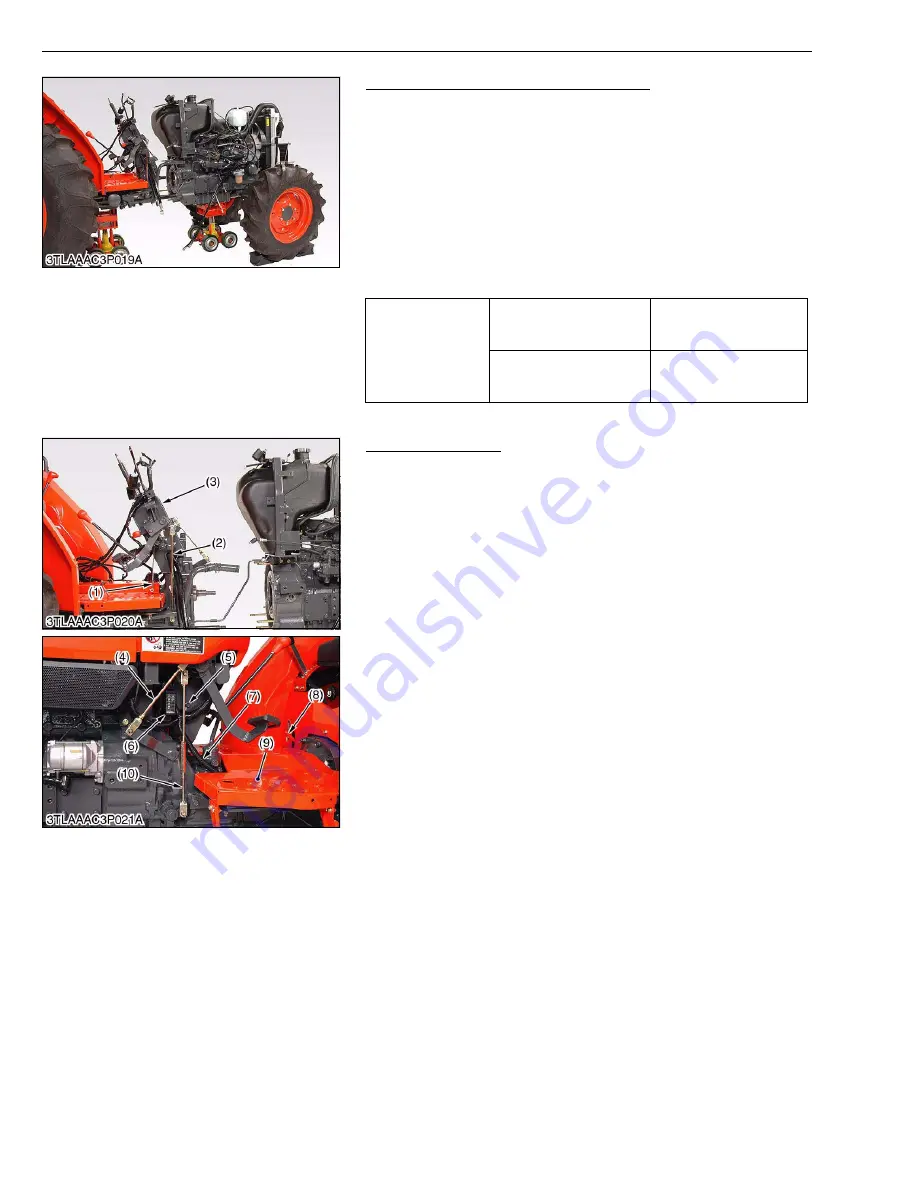
2-S20
L4400 , WSM
CLUTCH
Separating Engine from Clutch Housing
1. Place the disassembling stand under the engine and clutch
housing case.
2. Remove the steering support plates connecting steering support
and rear bonnet support.
3. Remove the engine and clutch housing mounting screws and
nuts.
4. Separate the engine and clutch housing.
(When reassembling)
• Apply grease to the spline of clutch shaft.
• Apply liquid gasket (Three Bond 1208D or equivalent) to joint
face of the flywheel housing and clutch housing.
(2) Separating Clutch Housing Mid Case
Outer Components
1. Disconnect foot accelerator rod (1).
2. Remove brake rod R.H. (2) and L.H. (10).
3. Remove mounting bolts and steering support (3).
4. Remove clutch rod (4).
5. Remove fuse box (6) and ground cable (5).
6. Disconnect differential lock pedal (8).
7. Remove step (9) and wiring (7).
W1028969
Tightening torque
Engine and clutch housing
mounting screw and nut
M12, grade 7
77.5 to 90.2 N·m
7.9 to 9.2 kgf·m
57.1 to 66.5 ft-lbs
Engine and clutch housing
mounting stud bolt
39.2 to 49.0 N·m
4.0 to 5.0 kgf·m
28.9 to 36.2 ft-lbs
(1) Foot Accelerator Rod
(2) Brake Rod R.H.
(3) Steering Support
(4) Clutch Rod
(5) Ground Cable
(6) Fuse Box
(7) Wiring Harness
(8) Differential Lock Pedal
(9) Step
(10) Brake Rod L.H.
KiSC issued 07, 2007 A
Tractor Manuals Scotland - Please Do Not Copy
Tractor Manuals Scotland