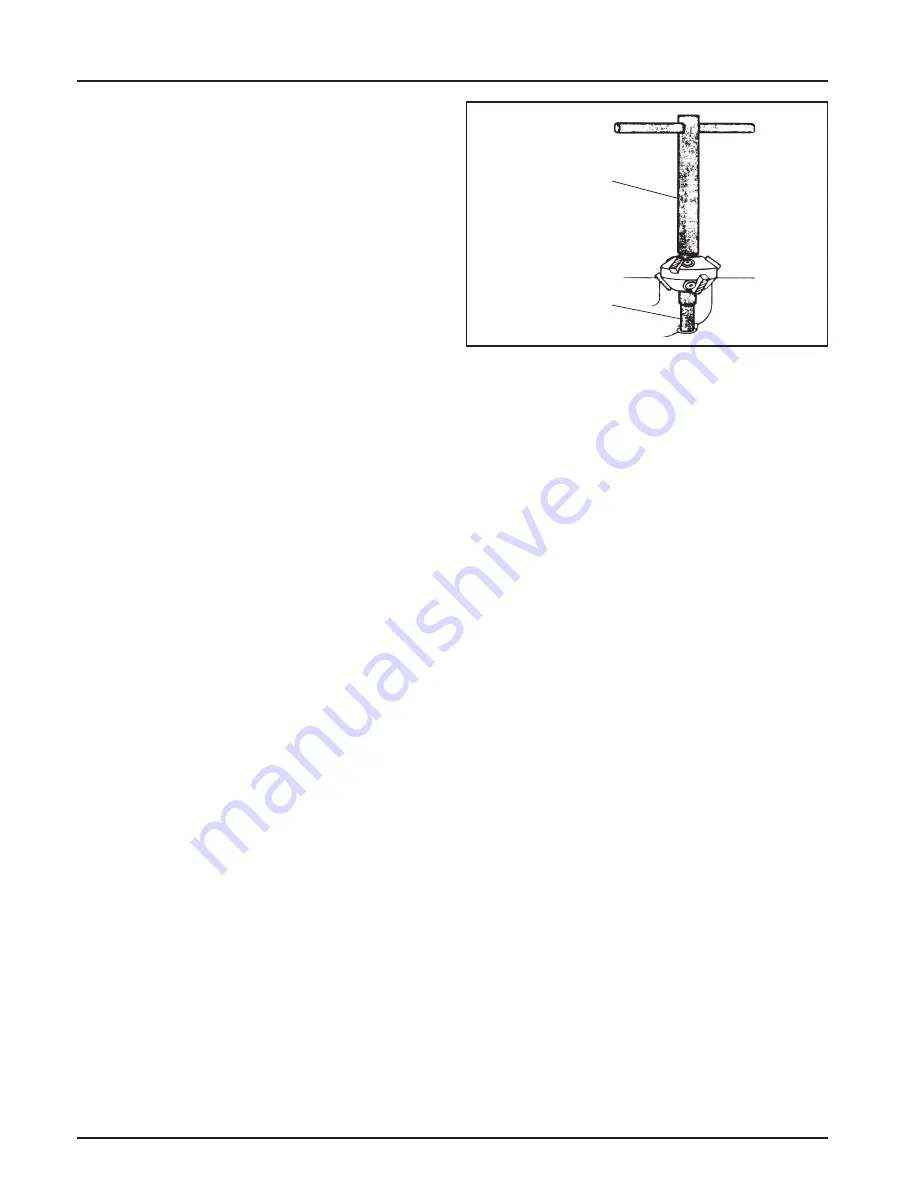
Section 9
Inspection and Reconditioning
9.8
Valve Guides
If a valve guide is worn beyond speci
fi
cations, it will
not guide the valve in a straight line. This may result
in burnt valve faces or seats, loss of compression, and
excessive oil consumption.
To check valve guide-to-valve stem clearance,
thoroughly clean the valve guide and, using a
split-ball gauge, measure the inside diameter of
the guide. Then, using an outside micrometer,
measure the diameter of the valve stem at several
points on the stem where it moves in the valve
guide. Use the largest stem diameter to calculate
the clearance by subtracting the stem diameter from
the guide diameter. If the intake clearance exceeds
0.038/0.076 mm (0.0015/0.0030 in.)
,
or the exhaust
clearance exceeds
0.050/0.088 mm (0.0020/0.0035 in.)
,
determine whether the valve stem or guide is
responsible for the excessive clearance.
The maximum (I.D.) wear on the intake valve guide
is
7.135 mm (0.2809 in.)
while
7.159 mm (0.2819 in.)
is the maximum allowed on the exhaust guide. The
guides are not removable but can be reamed
0.25 mm
(0.010 in.)
oversize. Valves with 0.25 mm oversize
stems must then be used.
If the guides are within limits but the valve stems are
worn beyond limits, install new valves.
Valve Seat Inserts
Hardened steel alloy intake and exhaust valve seat
inserts are press
fi
tt
ed into the cylinder head. The
inserts are not replaceable but can be reconditioned if
not too badly pi
tt
ed or distorted. If cracked or badly
warped, the cylinder head should be replaced.
Recondition the valve seat inserts following the
instructions provided with the valve seat cu
tt
er being
used. A typical cu
tt
er is shown in Figure 9-7. The
fi
nal
cut should be made with an 89° cu
tt
er as speci
fi
ed
for the valve seat angle in Figure 9-6. Cu
tt
ing the
proper 45° valve face angle as speci
fi
ed in Figure
9-6, and the proper valve seat angle (44.5°, half of the
full 89° angle), will achieve the desired 0.5° (1.0° full
cut) interference angle where the maximum pressure
occurs on the outside diameters of the valve face and
seat.
Valve Seat Cutter
Pilot
Figure 9-7. Typical Valve Seat Cutter.
Lapping Valves
Reground or new valves must be lapped in, to provide
proper
fi
t. Use a hand valve grinder with a suction
cup for
fi
nal lapping. Lightly coat the valve face with
a
fi
ne grade of grinding compound, then rotate the
valve on its seat with the grinder. Continue grinding
until a smooth surface is obtained on the seat and on
the valve face. Thoroughly clean the cylinder head in
soap and hot water to remove all traces of grinding
compound. A
ft
er drying the cylinder head, apply a
light coating of
SAE 10
oil to prevent rusting.
Valve Stem Seals
These engines use valve stem seals on the intake and
exhaust valves. Always use new seals when the valves
are removed from the cylinder head. The seals should
also be replaced if deteriorated or damaged in any
way.
Never reuse an old seal.
Pistons and Rings
Inspection
Scu
ffi
ng and scoring of pistons and cylinder walls
occurs when internal engine temperatures approach
the welding point of the piston. Temperatures high
enough to do this are created by friction, which is
usually a
tt
ributed to improper lubrication and/or
overheating of the engine.
Normally, very li
tt
le wear takes place in the piston
boss-piston pin area. If the original piston and
connecting rod can be reused a
ft
er new rings are
installed, the original pin can also be reused but new
piston pin retainers are required. The piston pin is
included as part of the piston assembly – if the pin
boss in the piston or the pin are worn or damaged, a
new piston assembly is required.
Summary of Contents for Comand Pro CH1000
Page 1: ...SERVICE MANUAL HORIZONTAL CRANKSHAFT CH940 CH1000...
Page 2: ......
Page 4: ......
Page 30: ...4 4 Section 4 Air Cleaner and Air Intake System...
Page 52: ...6 6 Section 6 Lubrication System...
Page 96: ...8 16 Section 8 Disassembly...
Page 110: ...Section 9 Inspection and Reconditioning 9 14...
Page 140: ...10 30 Section 10 Reassembly...
Page 141: ......