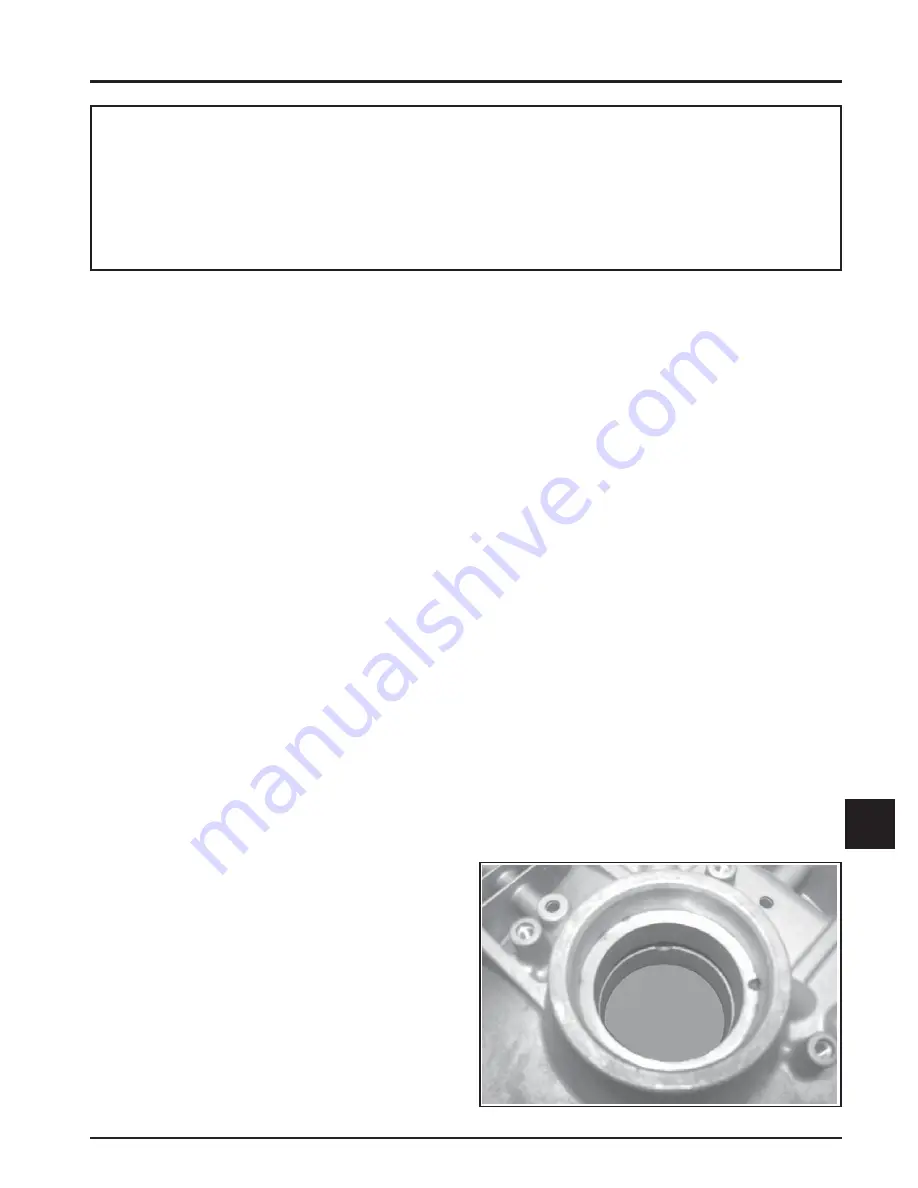
10.1
Section 10
Reassembly
10
Section 10
Reassembly
General
NOTE: Make sure the engine is assembled using
all speci
fi
ed torque values, tightening
sequences, and clearances. Failure to observe
speci
fi
cations could cause severe engine wear
or damage. Always use new gaskets. Apply a
small amount of oil to the threads of critical
fasteners before assembly, unless a Sealant or
Loctite
®
is speci
fi
ed or preapplied.
Make sure all traces of any cleaner are removed before
the engine is assembled and placed into operation.
Even small amounts of these cleaners can quickly
break down the lubricating properties of engine oil.
Check the closure plate, crankcase, cylinder heads,
and valve covers to be certain that all of the old gasket
material has been removed. Use gasket remover,
lacquer thinner, or paint remover to remove any
remaining traces. Clean the surfaces with isopropyl
alcohol, acetone, lacquer thinner, or electrical contact
cleaner.
Typical Reassembly Sequence
The following sequence is suggested for complete
engine reassembly. This procedure assumes that all
components are new or have been reconditioned, and
all component subassembly work has been completed.
The sequence may vary to accommodate options or
special equipment. Detailed procedures follow:
1. Install
fl
ywheel end oil seal.
2. Install li
ft
er feed chamber gaskets and cover.
3. Install
fl
ywheel end main bearing.
4. Install governor sha
ft
s, seal, and governor gear.
5. Install cranksha
ft
.
6. Install connecting rods with pistons and rings.
7. Install camsha
ft
.
8. Install closure plate main bearing and oil seal.
9. Install closure plate assembly.
10. Install oil pickup screen.
11. Install oil reservoir.
12. Check
cranksha
ft
end play.
13. Install breather assembly.
14. Install hydraulic li
ft
ers.
15. Assemble and install cylinder heads.
16. Install push rods and rocker arms.
17. Install valve covers.
18. Install spark plugs.
19. Install
oil
fi
lter adapter.
20. Install intake manifold.
21. Install
oil
fi
lter housing assembly.
22. Install backing shroud assembly.
23. Install stator, wiring harness, and recti
fi
er-
regulator.
24. Install
fl
ywheel.
25. Install ignition modules.
26. Install outer cylinder ba
ffl
es.
27. Install oil cooler.
28. Install cooling fan and grass screen.
29. Install electric starter.
30. Install valley ba
ffl
es.
31. Install
carburetor
32. Install governor lever.
33. Install control bracket and air cleaner assembly.
34. Install
thro
tt
le and choke linkages.
35. Install Oil Sentry™
switch (if equipped).
36. Install blower housing and cylinder shrouds.
37. Install control panel (if equipped).
38. Install
mu
ffl
er.
39. Install
oil
fi
lter and add oil to crankcase.
40. Connect spark plug leads.
Install Flywheel End Oil Seal
1. Make sure that the seal bore of the crankcase is
clean and free of any nicks or burrs. See Figure
10-1.
Figure 10-1. Seal Bore of Crankcase.
Summary of Contents for Comand Pro CH1000
Page 1: ...SERVICE MANUAL HORIZONTAL CRANKSHAFT CH940 CH1000...
Page 2: ......
Page 4: ......
Page 30: ...4 4 Section 4 Air Cleaner and Air Intake System...
Page 52: ...6 6 Section 6 Lubrication System...
Page 96: ...8 16 Section 8 Disassembly...
Page 110: ...Section 9 Inspection and Reconditioning 9 14...
Page 140: ...10 30 Section 10 Reassembly...
Page 141: ......