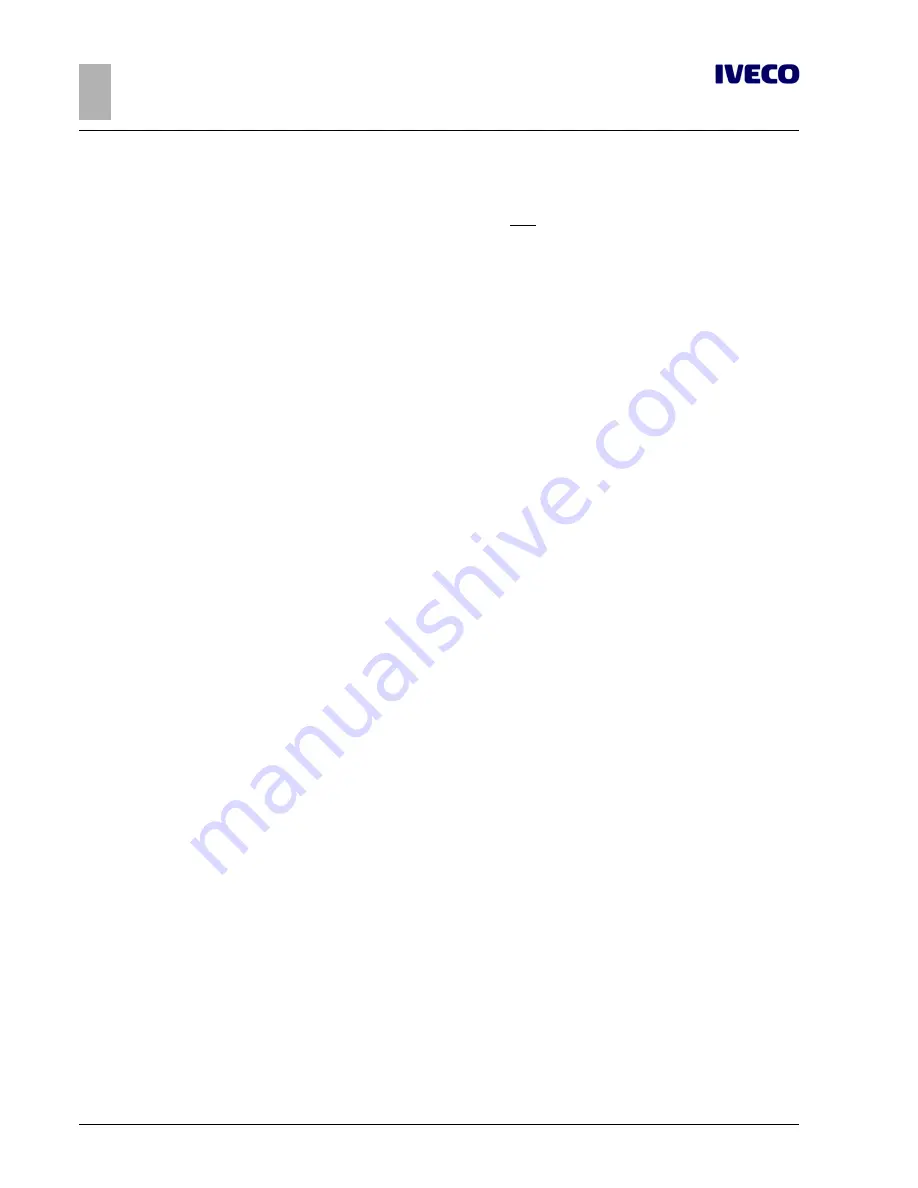
44
EUROCARGO Euro 6
–
CHASSIS INTERVENTIONS
CHASSIS INTERVENTIONS
2.10
MODIFYING THE ENGINE COOLING SYSTEM
–
Printed 603.95.747
–
1st Ed. - Base 12/2013
Engine exhaust
Given the compaction of the “Hi-e SCR” system (see Section 6 (
➠
Page 5)) and the optimal arrangement of its assemblies on
the chassis, any modifications to the exhaust pipe formation may be permitted only for the realization of a vertical exhaust outlet,
differing from that offered as optional 180.
The realization of a vertical exhaust requires the following:
●
a considerable distance from the air intake conveyor;
●
the simplest possible pipe route (curvatures with radii of no less than 2.5 times the outer diameter, passage sections no smal-
ler than those of the original solution, absence of throttling);
●
suitable distances (min. 150 mm) from electrical systems and plastic pipes (shorter distances progressively require plate guards,
thermal insulators or the replacement of plastic pipes with steel ones);
●
a support structure for the vertical part fastened to the vehicle chassis and braced, if necessary;
●
a flexible pipe between the part of the exhaust connected to the engine and the part rigidly fastened to the chassis;
●
a solution that prevents water entering from the top of the pipe (e.g. curvature).
2.10
MODIFYING THE ENGINE COOLING SYSTEM
The good operating conditions of the original system must not be altered, especially for what concerns the radiator, free surface of
the radiator and pipes (dimension and layout).
In any case, if modifications are required (e.g: cab modifications) that entail interventions on the engine cooling system, keep in mind
that:
●
The air passageway area for radiator cooling must not be less than that on vehicles with series standard cabs;
●
maximum air expulsion from the engine compartment must be guaranteed, making sure that there are no hot air pockets of
recirculation by adopting guards or deflectors;
●
fan performance must not be modified;
●
any modifications of the water piping must not compromise complete filling of the circuit (done with a steady flow and
without any backflow from the intake until the circuit is filled) and regular water flow; in addition, these modifications must not
alter maximum water stabilisation temperature, even in the most demanding conditions of use;
●
pipe layout must be done so as to avoid the formation of air pockets (e.g. eliminating siphoning bends or installing required
vents) that may make water circulation difficult;
●
check that water pump activation at engine start-up and successive operation during idling is immediate (accelerate a few
times), even when circuit is not pressurised. During checks make sure that the water pump supply pressure, with engine at
top speed and no load, is less than 1 bar.
To check the operation of the cooling circuit we must account for the water supply, bleed and circulation proceeding as follows:
●
open the supply valve of the heating system and the heater bleed valves;
●
fill the circuit while the engine is off with a flow rate of 8 - 10 l/min, until water seeps from the overflow vent;
●
one bled, close the heater bleed valves;
●
start the engine and run idle for 5 minutes, successively check to see that the water level in the supply tank has not dropped
below minimum level;
●
gradually rev the engine, checking that average pressure in the water pump outlet pipes steadily increases without and discon-
tinuities;
●
keep accelerating the engine until the thermostat opens, causing air bubbles to pass through transparent pipes installed
between:
■
engine output and radiator;
■
water supply tank and water pump;
■
engine bleed and water supply tank;
●
check, after the thermostat has be open for 15 minutes, that there are no more bubbles in the circuit;
Summary of Contents for EUROCARGO
Page 1: ...EUROCARGO EURO 6 M E D I U M R A N G E BODYBUILDERS INSTRUCTIONS ISSUE 2013 ...
Page 4: ... Printed 603 95 747 Base 12 2013 ...
Page 6: ... Printed 603 95 747 Base 12 2013 ...
Page 8: ... Printed 603 95 747 Base 12 2013 ...
Page 9: ... Printed 603 95 747 Base 12 2013 SECTION 1 GENERAL INFORMATION ...
Page 10: ... Printed 603 95 747 Base 12 2013 ...
Page 29: ... Printed 603 95 747 Base 12 2013 SECTION 2 CHASSIS INTERVENTIONS ...
Page 30: ... Printed 603 95 747 Base 12 2013 ...
Page 91: ... Printed 603 95 747 Base 12 2013 SECTION 3 APPLICATIONS OF SUPERSTRUCTURES ...
Page 92: ... Printed 603 95 747 Base 12 2013 ...
Page 135: ... Printed 603 95 747 Base 12 2013 SECTION 4 POWER TAKE OFFS ...
Page 136: ... Printed 603 95 747 Base 12 2013 ...
Page 138: ...4 EUROCARGO Euro 6 POWER TAKE OFFS POWER TAKE OFFS Printed 603 95 747 1st Ed Base 12 2013 ...
Page 160: ...26 EUROCARGO Euro 6 POWER TAKE OFFS POWER TAKE OFFS Printed 603 95 747 1st Ed Base 12 2013 ...
Page 161: ... Printed 603 95 747 Base 12 2013 SECTION 5 ELECTRONIC SUB SYSTEMS ...
Page 162: ... Printed 603 95 747 Base 12 2013 ...
Page 215: ... Printed 603 95 747 Base 12 2013 SECTION 6 SPECIAL INSTRUCTIONS FOR SCR EXHAUST SYSTEM ...
Page 216: ... Printed 603 95 747 Base 12 2013 ...
Page 226: ... Printed 603 95 747 Base 12 2013 ...