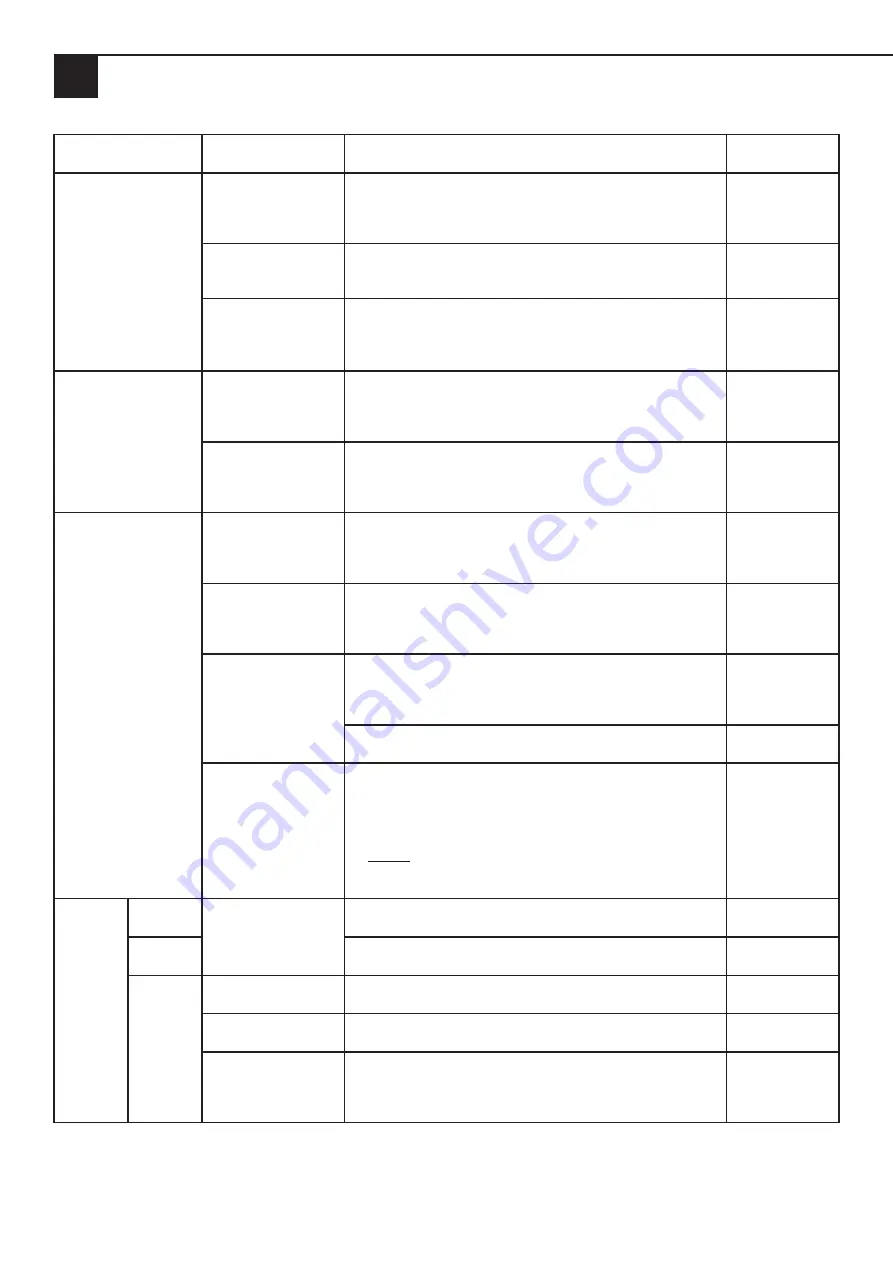
Page 44
EN
Chapter 12 Faults, causes and solutions
Symptom
Potential cause
Check / solution
Personnel
qualification
Machinery cannot be
switched on.
No input voltage
available.
• Have the voltage supply checked at the worksite distribution
board, at the sockets, the supply cables and the fuse protec-
tion.
• Have the voltage supply restored if it was interrupted.
Service
technician/
qualified
electrician
No or too low water
pressure.
• Check the water supply.
• If necessary, clean the dirt trap sieve.
• Check the water pump.
Machine
operator
Pump drive motor is
folded up or the ma-
chine is not level.
• Fold the motor onto the mixing zone and lock the side tilting
flange.
• Make sure the machine is horizontal.
Machine
operator
Pressure booster pump
isn’t running.
Motor protection
switch of the booster
pump has tripped.
• Switch on the motor protection switch.
Service
technician/
qualified
electrician
Pressure booster
pump impeller is
blocked.
• Arrange for the pressure booster pump to be dismantled and
the impeller to be made operable again.
• Have the pressure booster pump replaced if it is defective.
Service
technician/
qualified
electrician
The machine has
stopped.
Pump unit motor
protection switch has
tripped.
• Switch on the motor protection switch.
Service
technician/
qualified
electrician
Mixing coil or
rotor/stator mechani-
cally blocked.
• Check whether any hardened material or foreign bodies are
around the mixing coil or in the rotor/stator; if necessary, re-
move the hardened material or foreign bodies.
Machine
operator /
Service
technician
Star feeder motor
protection switch has
tripped.
• Switch on the motor protection switch.
Service
technician/
qualified
electrician
• Clean the material hopper and the star feeder.
Machine
operator
Delivery pressure too
high because the ma-
terial is too thick, the
conveyor hose is too
long or a smoke plug
has formed.
• Set the material consistency correctly.
• Shorten the conveyor hose or use a larger hose diameter.
• Change the direction of rotation on the phase-change
switch until the pressure on the mortar pressure gauge
shows 0 bar. Then clean the hoses and remove the plug.
Danger: Open hose couplings only when the display is de-
pressurised, your face is turned away and you are wearing
protective goggles.
Machine
operator
Material
consistency
too thick
Fine adjustment valve
is set incorrectly.
• Open the fine adjustment valve.
Machine
operator
too thin
• Close the fine adjustment valve.
Machine
operator
Consisten-
cy fluctua-
tions
Dry material supply is
not uniform.
• Check the material flow
• If necessary, clean the mixing pipe inlet
Machine
operator
The pump unit (rotor/
stator) is worn out.
• Replace the pump unit (rotor/stator)
Machine
operator
The pressure reducer
is set incorrectly
• Have the pressure reducer setting checked and adjusted cor-
rectly if necessary.
Service
technician/
qualified
electrician