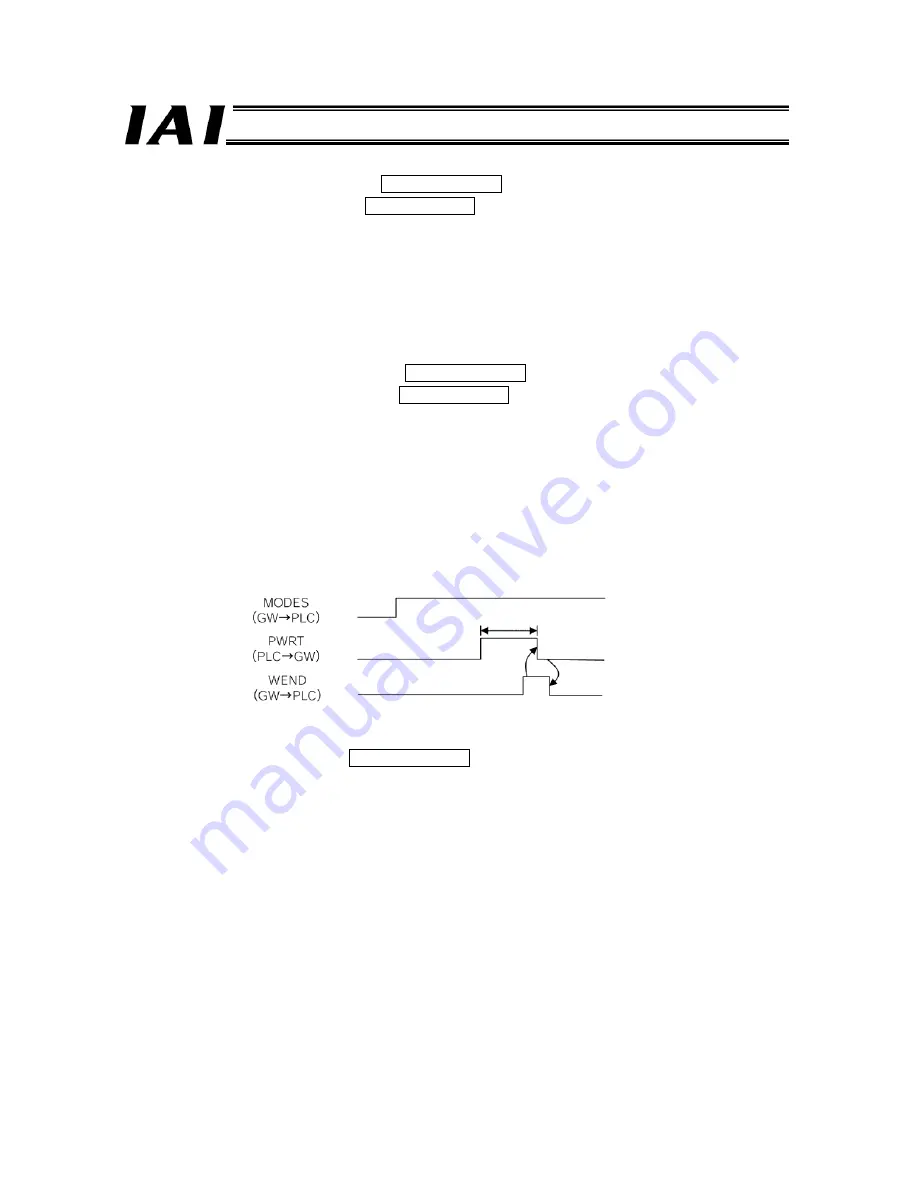
82
Part 1 Specification
(17) Teaching Mode Command (MODE) PLC Output Signal
(Effective only in the positioner mode)
Teaching Mode Status (MODES) PLC Input Signal
When this signal is turned “1,” the controller will switch from the normal operation mode to the teaching mode. After
switching to the teaching mode, each axis controller will output the teaching mode status (MODES) signal.
Turning the MODE signal “1” (ON) switches the normal operation mode to the teaching mode.
When the teaching mode becomes effective, the MODES signal for each controller axis turns “1” (ON).
Teaching should be performed on the PLC side after confirming that the MODES signal has turned “1” (ON).
Switching from the normal operation mode to the teaching mode is permitted in the following conditions:
•
The actuator (motor) is stopped
•
The JOG+ signal and JOG- signal are “0” (OFF)
•
The position data load command (PWRT) signal and positioning start (CSTR) signal are “0” (OFF)
(18) Position Data Load Command (PWRT) PLC Output Signal (In the positioner mode only)
Position Data Load Complete (WEND) PLC Input Signal
The PWRT signal is effective when the MODES signal is “1” (ON).
When the PWRT signal remains “1” (ON) for 20 msec or more (*1), the current position data will be written to the
“Position” field under the position number (PC1 to PC512) currently specified by the PLC. (*2)
When the writing is complete, the WEND signal turns “1” (ON).
The host PLC should turn the PWRT signal “0” (OFF) after the WEND signal has turned “1” (ON).
If the PWRT signal is turned “0” (OFF) before the WEND signal turns “1” (ON), the WEND signal will not turn “1” (ON).
When the PWRT signal is turned “0” (OFF), the WEND signal turns “0” (OFF).
*1 If the signal only remains “1” (ON) for less than 20 msec, the data may not be written.
*2 If any data other than position is not yet defined, the default value of the corresponding parameter will be written.
(19) Forced Brake Release (BKRL) PLC Output Signal
The brake can be forcibly released by turning this signal “1” (ON).
20 msec or more
Summary of Contents for RoboNet
Page 1: ...Operation Manual Forth Edition ROBONET ...
Page 257: ...237 Part 2 Startup Chapter X Installed face down X Installed face up ...
Page 354: ...334 ...
Page 395: ...375 ...
Page 396: ...376 ...
Page 397: ...377 ...