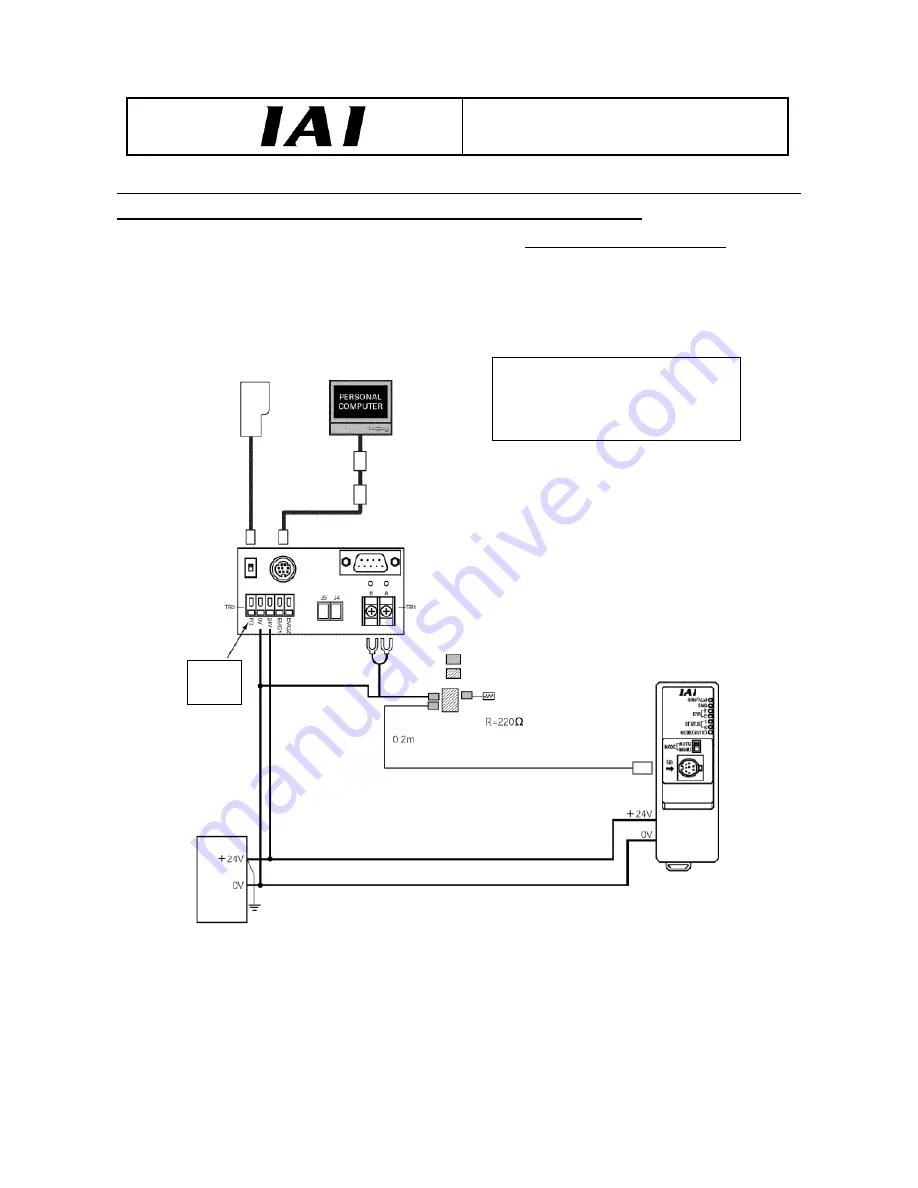
CAUTION
Teaching pendant
PC, etc.
Do not
connect
the FG.
Do not connect the FG of the PC to ground.
If the FC may be connected to ground
through other COM port, disconnect the
communication cable from the applicable
COM port.
PC software
RS232 connection type
<Model: RCM-101-MW>
USB connection type
<Model: RCM-101-USB>
* The cable is supplied with the PC software.
SIO converter (optional)
(with built-in terminal resistor)
Model: RCB-TU-SIO-A (B)
* One e-CON connector, one junction and one
terminal resistor are supplied with one
controller link cable.
e-CON connector (3-1473562-4 by AMP)
Junction (5-1473574-4 by AMP)
GateWay
R unit
Terminal resistor
Controller link cable
Model: CB-RCB-CTL002
24-V power supply
Notes on Connecting PC and Teaching Pendant to ROBONET Whose
24-V Power Supply Is Grounded at Positive Terminal
If the positive terminal of the ROBONET’s 24-V power supply is grounded, use a SIO converter as shown below to connect a
teaching pendant or PC to the GateWayR unit.
At this time, do not connect the FG of the SIO converter.
Summary of Contents for RoboNet
Page 1: ...Operation Manual Forth Edition ROBONET ...
Page 257: ...237 Part 2 Startup Chapter X Installed face down X Installed face up ...
Page 354: ...334 ...
Page 395: ...375 ...
Page 396: ...376 ...
Page 397: ...377 ...