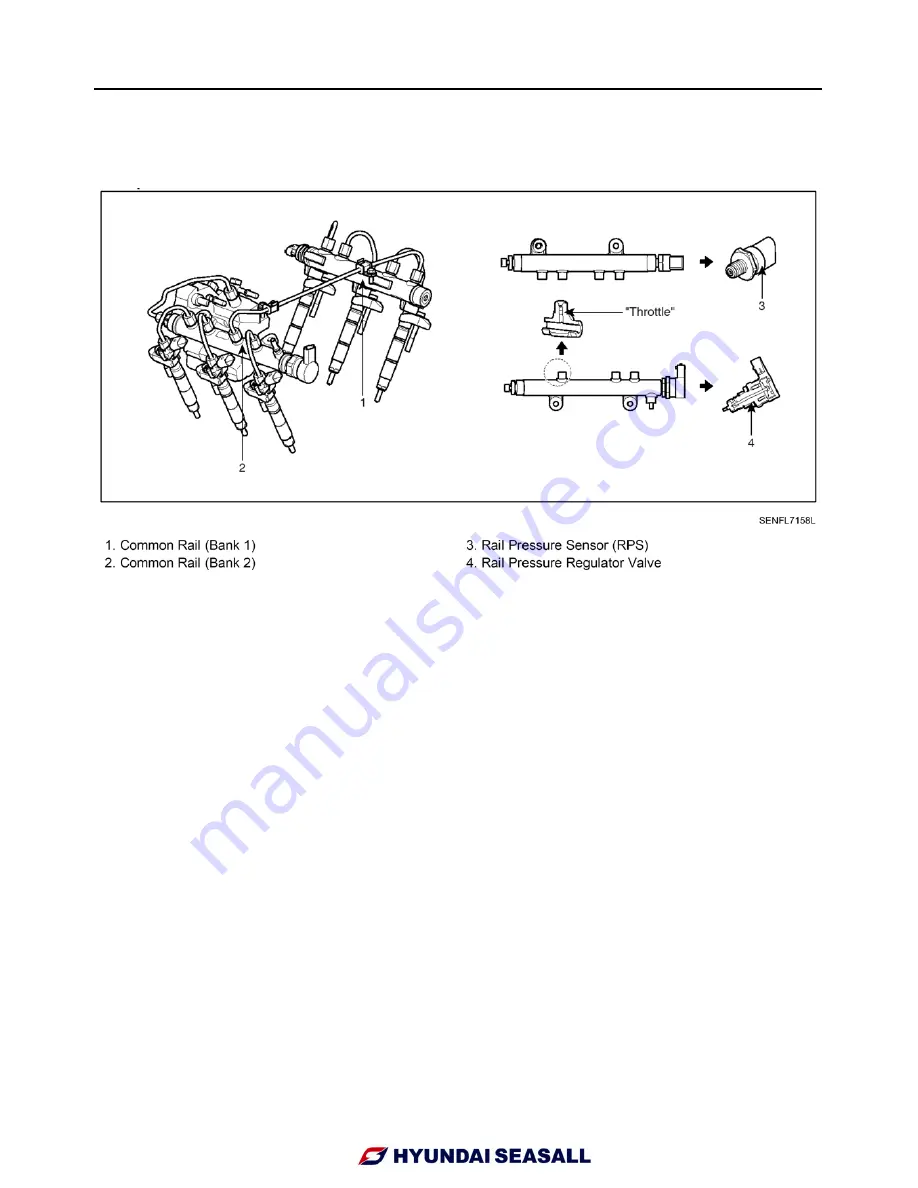
Fuel System
138 Fuel Delivery System
Common Rail
Component
Removal
☢
WARNING
As the Piezo-Injector operates under maximum DC
200V, there may be a risk of an electric shock caused
by shorted control line etc. So when repairing the
injector or its wiring, disconnect the battery negative (-
) terminal from the battery and wait for about 30
seconds.
◉
CAUTION
▪ Common Rail Fuel Injection System operates with
extremely high pressure (approximately 1,600bar), so
never perform any work on injection system with
engine running or within 30 seconds after the engine
stops.
▪ Keep cleanly the parts and the working area.
▪ Pay attention to a foreign substance.
▪ Just before installing injector, tube or hose, remove
the protect-cap attached on them.
▪ Do not remove injector except for special case.
▪ When installing Injector
-Wash the contact area of the injector and replace
the O-ring with a new one. -Spread oil on the
injector O-ring. -To protect damage caused by
shock, vertically
insert the injector into the cylinder head.
▪ When installing High Pressure Fuel Pipe
-Do not use again the used high pressure fuel pipe.
-Install the flange nut correctly.
Summary of Contents for S220P
Page 3: ...Engine Mechanical System 2 General Information General Information Specifications ...
Page 4: ...Engine Mechanical System 3 General Information Specifications ...
Page 5: ...Engine Mechanical System 4 General Information Specifications ...
Page 10: ...Engine Mechanical System 9 Cooling System Special Service Tools ...
Page 11: ...Engine Mechanical System 10 Cooling System Special Service Tools ...
Page 18: ...Engine Mechanical System 17 Cooling System ...
Page 19: ...Engine Mechanical System 18 Cooling System Thermostat ...
Page 55: ...Engine Mechanical System 54 Lubrication System ...
Page 73: ...Engine Electrical System 72 General Information Troubleshooting Charging system ...
Page 74: ...Engine Electrical System 73 General Information Starting system Special service tools ...
Page 75: ...Engine Electrical System 74 Charging System Charging system Alternator ...
Page 80: ...Engine Electrical System 79 Starting System Components ...
Page 91: ...Fuel System 90 General Information Special Service Tools ...
Page 112: ...Fuel System 111 Diesel Control System EOI Engine Operating Indicator System Circuit Diagram 1 ...
Page 117: ...Fuel System 116 Diesel Control System Specification Circuit Diagram ...