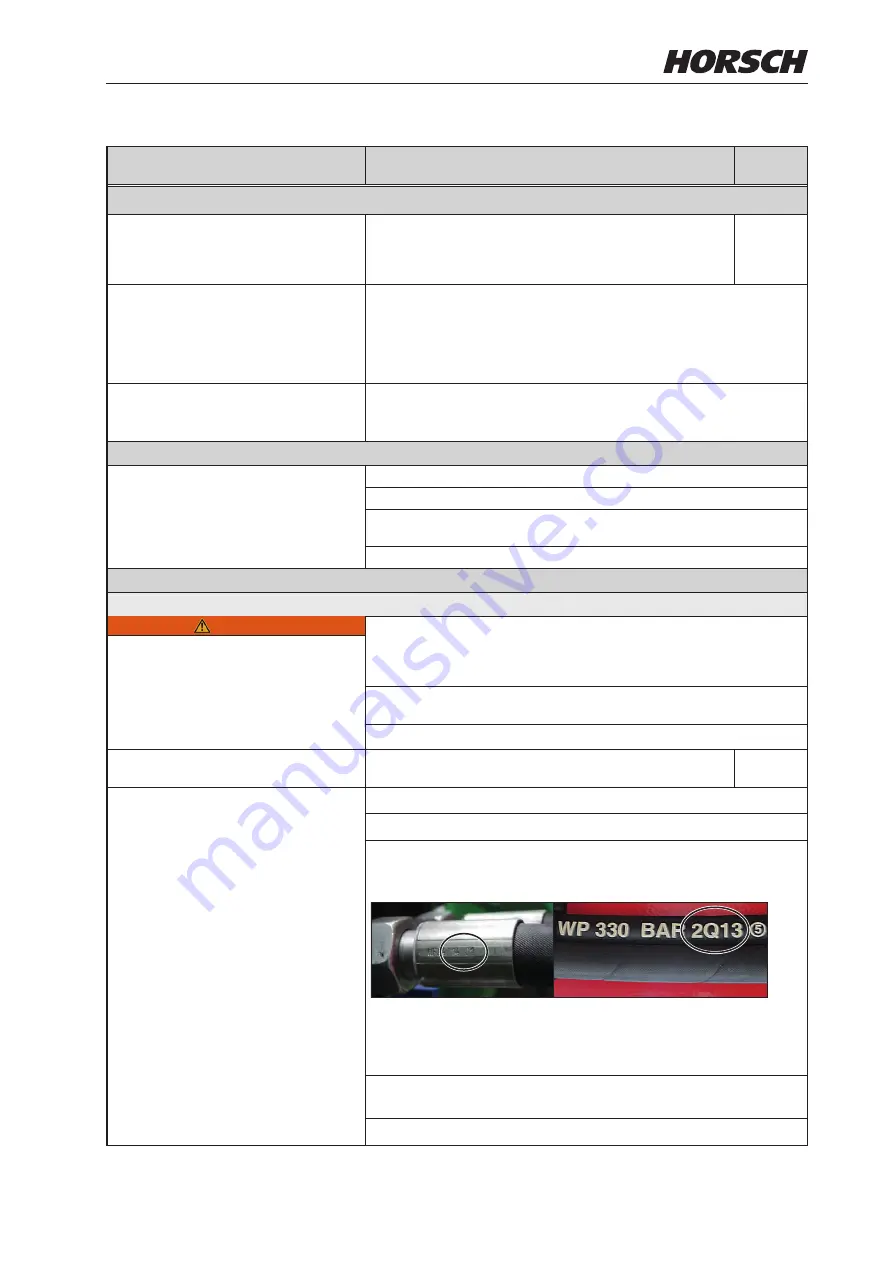
Maintenance overview Maestro CV
Maintenance location
Work instructions
Interval
After 10 operating hours
Retighten all screw and plug-in
connections as well as the hydraulic
connections.
Even firmly tightened screw connections can come loose
(e.g. because of material settlement or paint residues between
the screw elements). This can lead to loose screw connections
and leaking hydraulic connections.
once
Retighten all wheel nuts
M18 x 1.5 - 300 Nm
M22 x 1.5 - 510 Nm
¾
initially after 10 hours or 50 km
¾
again after 10 hours or 50 km
¾
then retighten daily until the screws have settled and further tightening
is no longer possible
¾
then always before the start of the season and every 50 operating hours
Retighten all screws on the clamping
plates of the drill units, see section
Clamping plates
(torque 180 Nm)
¾
for the first time after 10 hours
¾
once more after 50 hours
Before the season
Complete machine
Read the operating instructions carefully as a refresher.
Check all screw connections for firm seating and retighten as necessary
Check condition and function of all protective features and replace,
if necessary
Check electrical lines for damage and replace, if necessary.
In use
Hydraulics
WARNING
Lower all hydraulically lifted parts (e.g. wings, packer, undercarriage,
etc.) to the ground before performing any work on the hydraulic system.
Depressurise the hydraulics on the tractor and implement side! Empty
the pressure accumulators.
Risk of scalding! Allow hydraulic oil and hydraulic components heated
during operation to cool down before any work on the hydraulic system.
Observe the notes on hydraulics in the chapter
Safety and responsibility
.
Hydraulic system and components
Check all hydraulic components and hoses for function,
leak tightness, fastening and chafing
40 h
Hydraulic hoses
Check the hydraulic hoses regularly for damage (cracks, chafing, etc.).
Replace damaged and faulty hoses immediately.
Hydraulic hoses must be replaced after 6 years. Pay attention to the
manufacturing date on the crimp sleeve (year/month) and the hose
(quarter/year):
Crimp sleeve
Hose
Depending on the conditions of use (e.g. weather influences) or in case
of higher strains on the machine the hoses may need to be replaced
earlier.
Have the hydraulic system checked by an expert at least once every
year.
Follow the country-specific regulations and directives.
127
Summary of Contents for Maestro 12.45 CV
Page 2: ......
Page 5: ......
Page 27: ...Maestro 8 CV 5470 665 3900 6500 3000 5900 8 70 CV 6360 8 75 CV 6570 8 80 CV 6790 23...
Page 28: ...5470 6500 3900 615 3000 Maestro 9 CV 6700 9 70 CV 7590 9 75 CV 7160 9 80 CV 7590 24...
Page 29: ...Maestro 12 CV 5550 6500 665 3900 3000 6790 5900 25...
Page 145: ...WARNING Never park the machine unsecured with the axle dismantled 141...
Page 154: ......