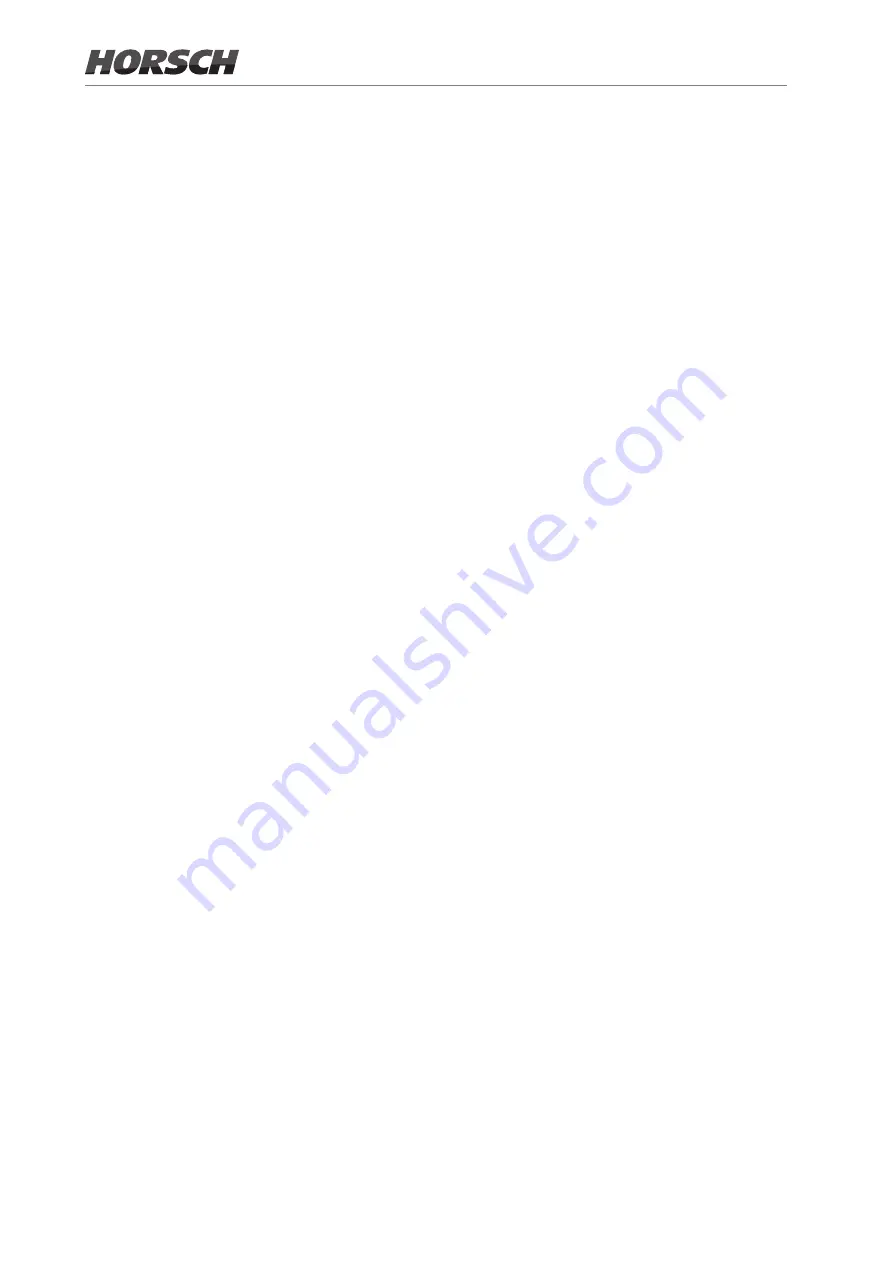
Spraying boom transport lock
Spraying height 149
Spraying line
,
Spraying mixture tank 135,
Spraying mixture tank residue drain 126
Spraying operation
Spraying table 150
Stability 36
Starting aid 100
Start position 59,
Steam jet
Steering 94
Steering and braking ability 36
Steering column adjustment 59
Stickers 33
Stowage bag
Strap
Suction connection for solution tank filling
Suction filter
Sun visor
Switch-over ball valve
Swivelling facility 55
Symbols for travel operation
System continuous inside cleaning 131,
T
table
Target area distance 150
Technical data, spraying line 152
,
,150
Tightening torques 194
Time / date
Transport position
Travel direction selector lever 60
Travel distance 152
Travel drive modes
Travel modes 93
Travel operation 90
Type plate 40
Tyre inspection 113
,113
U
V
W
Warning horn 61
Warning triangle
Warranty
Washing gun
Wheel base 39
Wheel drive
Wheel hub gearbox 112
Windscreen washing system
Windscreen washing water 63
Windscreen wipers 62
Wind speed
Working headlights 46
Working height 150
200
Summary of Contents for LEEB PT 330
Page 4: ......
Page 6: ......
Page 33: ...1 17 Position of safety stickers 33...
Page 34: ...34...
Page 187: ...Diagram a with example 187...
Page 201: ...201...
Page 202: ......