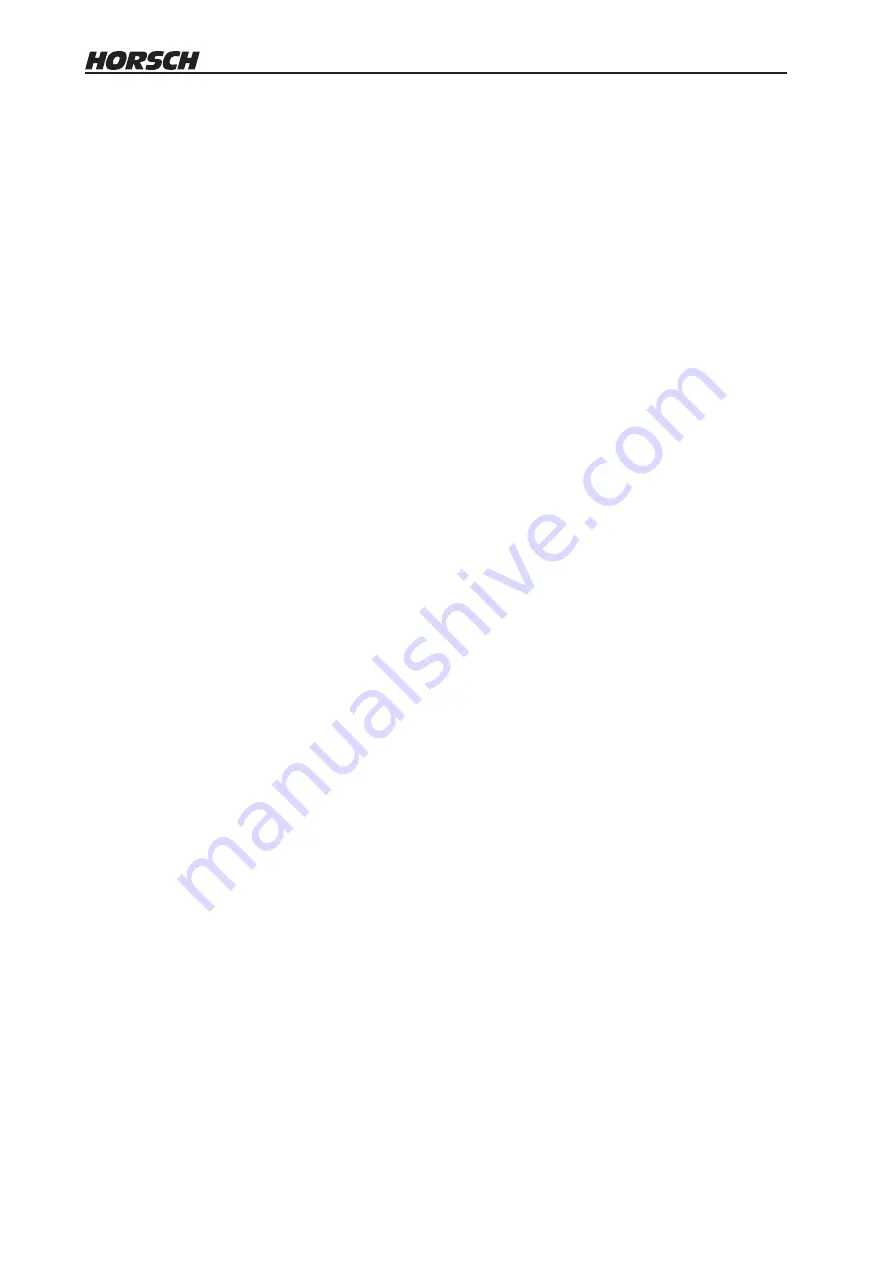
150
,
O
order number and explanations on sticker 32
P
,
,
,
,
,
,
,
,
pressure accumulator 20
pressure agitator 39
,
→
agitator
,
,
,
,
,
,
,
,
,
,
→
spraying pump
Q
,
R
,
,
residual quantity, diluted 108
,
road traffic licensing regulation 16
S
safeguarding tractor / machine 83
,
safety and accident prevention instructions 17
safety and protective features 17
,
,
,
,
safety notes on the machine 29
,
,
,
,
,
,
,
,
,
,
,
,
,
,
,
spraying boom 105
Spraying boom 71
→
folding boom
,
,
spraying operation, preparation 92
,
,
Summary of Contents for Leeb 6 GS
Page 4: ......
Page 6: ......
Page 123: ...123 Fig 9 3 1a Fig 9 3 1 c Fig 9 3 1 d Fig 9 3 1 f Fig 9 3 1b Fig 9 3 1 e...
Page 140: ...140 Diagram a with example...
Page 147: ...147...
Page 152: ......
Page 153: ......