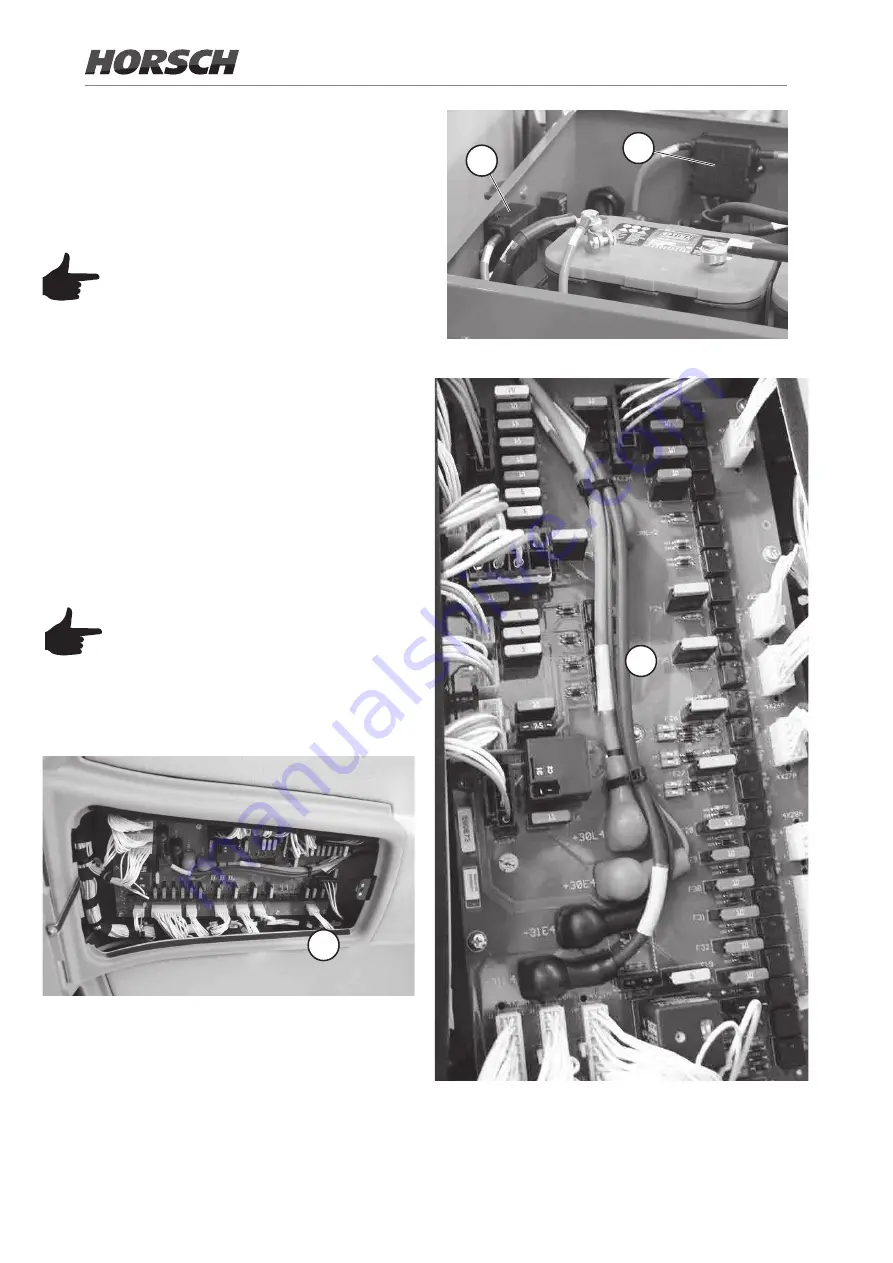
16.10.2
Fuses ISO-BUS interface
The fuses (1) for ISOBUS interface and boom control
(BoomControl) are located inside the battery box.
(1) 12V supply for generator and cabin
(2) 24V supply for cabin, spare fuses
The description of the individual fuses is
located inside the covers (1) and (2).
16.10.3 Cabin-mounted PCB cabin roof
The fuses are centrally located inside the cabin. The
relays are located in the junction box at the front right
hand side under the console, as well as on the fuse
board in the cabin roof (2).
You should have work in the electronic
system solely performed by your
HORSCH Customer Service or our sales
partners!
Fuse and relay designations can be found on the
printed circuit board or on the cover as well as in the
following chapter.
2
2
1
2
178
Summary of Contents for 80910205
Page 2: ......
Page 8: ...8...
Page 39: ...04002623 04003745 04003747 04002625 04002626 39...
Page 44: ...44...
Page 82: ...82...
Page 173: ...11 7 8 9 10 173...
Page 188: ...188...
Page 216: ...216...
Page 217: ......