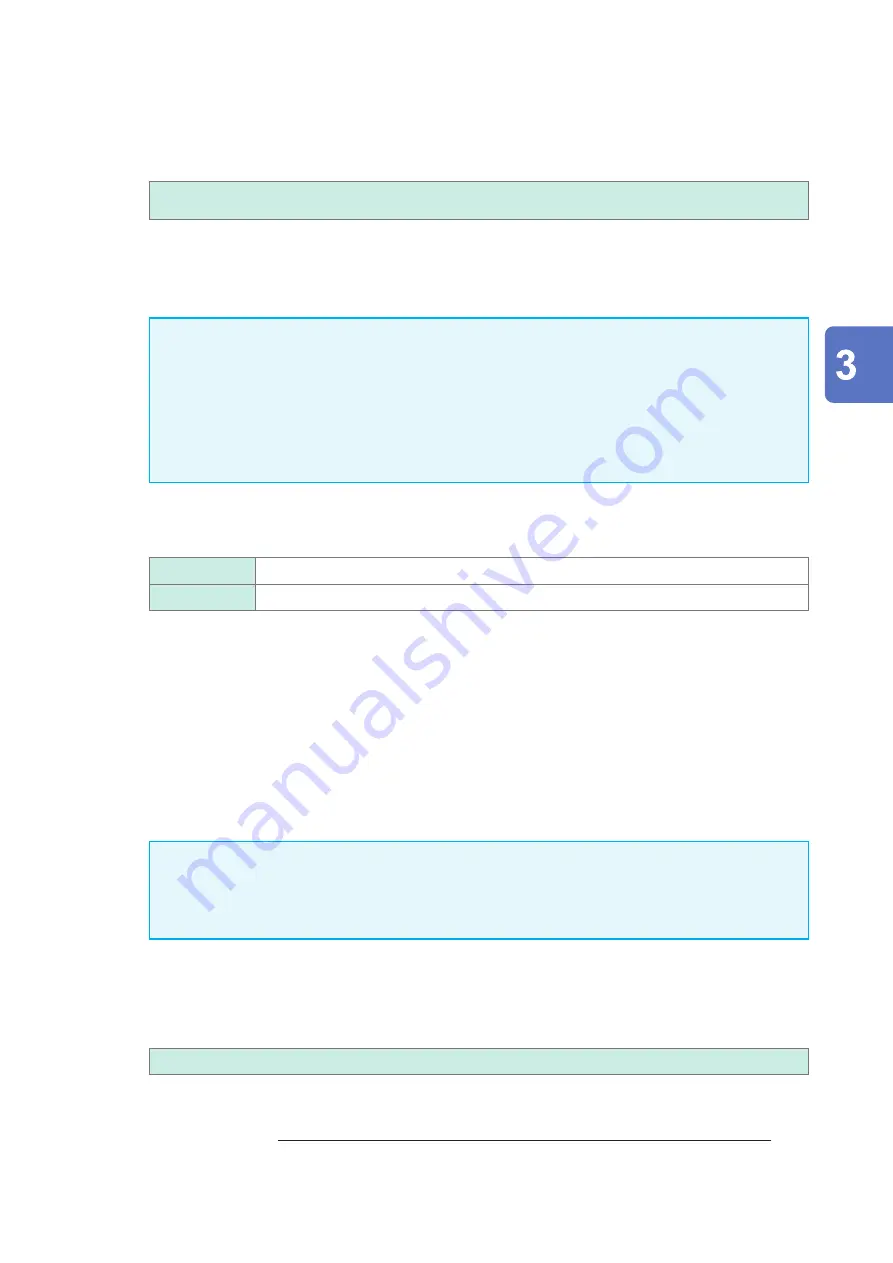
85
Motor Measurement (Motor Analysis-Equipped Model)
4
Tap the
[Sync. source]
box to open the settings window.
Set the source that determines the period that serves as the basis for calculating motor analysis parameters.
Motor analysis parameters are measured using intervals of the source selected here.
See “Synchronization source” (p. 58).
U1
to
U8
,
I1
to
I8
,
DC
,
Ext1
to
Ext4
,
Zph1
,
Zph3
CH B
,
CH D
,
CH F
,
CH H
When setting Ch. H to the origin signal (Origin), you can select
[Zph1]
or
[Zph3]
as the synchronization
source.
The set motor synchronization source is displayed in
[Sync]
at the top of the screen when
[A-D]
or
[E-H]
is
displayed on
[Meas]
> the
[Basic]
screen.
IMPORTANT
•
When
[DC]
is selected as the synchronization source, segments will be matched with the data
refresh interval.
(10 ms, 50 ms, 200 ms)
•
When measuring motor efficiency under a fluctuating load, select the same synchronization
source as that for the motor input measurement channel. Efficiency can be measured more
accurately by using the same calculation interval for motor input and motor output.
5
Tap the
[LPF/PNF]
box and select a low-pass filter or pulse noise filter from the list.
LPF
OFF (20 kHz)
,
1 kHz
PNF
OFF
,
Strong (100 kHz)
,
Weak (1.8 MHz)
Low-pass filter (
LPF)
When the input of Ch. A, Ch. C, Ch. E, or Ch. G is set to the analog DC setting, you can set the filter to
eliminate harmonic noise.
Set the filter to
[1 kHz]
if external noise in analog DC input destabilizes measurement.
The LPF setting has no effect on input when input is not set to analog DC input.
Pulse noise filter (PNF)
When the input of Ch. A, Ch. C, Ch. E, or Ch. G is set to
[Pulse]
or
[Frequency]
, you can set the filter to
eliminate the input pulse noise for Ch. B, Ch. D, Ch. F, or Ch. H, respectively.
Use this setting when the measured values for frequency or RPM data input using a pulse signal are unstable
due to noise.
IMPORTANT
•
This setting has no effect on channels for which the input is set to analog DC input.
•
When the PNF is set to
[Weak (1.8 MHz)]
, pulses of approx. 1.8 MHz or higher will not be
detected; when it is set to
[Strong (100 kHz)]
, pulses of 100 kHz or higher will not be detected.
6
Tap the
[Slip]
box, then select a input frequency source from the list.
This sets the frequency of the measurement channel inputted to the motor in order to calculate the motor’s
slip.
fu1
,
fI1
,
fu2
,
fI2
,
fu3
,
fI3
,
fu4
,
fI4
,
fu5
,
fI5
,
fu6
,
fI6
,
fu7
,
fI7
,
fu8
,
fI8
Slip equations
When the
unit is r/min 100
×
2
×
60
×
(input frequency) − |RPM|
×
(setting value of the number of motor poles)
2
×
60
×
(input frequency)
Select the voltage or current supplied to the motor, whichever is more stable, as the input frequency source.
Displaying Power Numerically
HIOKI PW8001A961-00
Summary of Contents for PW8001-01
Page 2: ...HIOKI PW8001A961 00...
Page 6: ...Contents iv HIOKI PW8001A961 00...
Page 56: ...50 Checking Connections HIOKI PW8001A961 00...
Page 120: ...114 Power Calculation Method HIOKI PW8001A961 00...
Page 162: ...156 Controlling Integration with External Signals HIOKI PW8001A961 00...
Page 236: ...230 U7005 15MS s Input Unit HIOKI PW8001A961 00...
Page 258: ...252 Index HIOKI PW8001A961 00...
Page 259: ...HIOKI PW8001A961 00...
Page 260: ...HIOKI PW8001A961 00...
Page 261: ...HIOKI PW8001A961 00...
Page 262: ...www hioki com HIOKI PW8001A961 00...